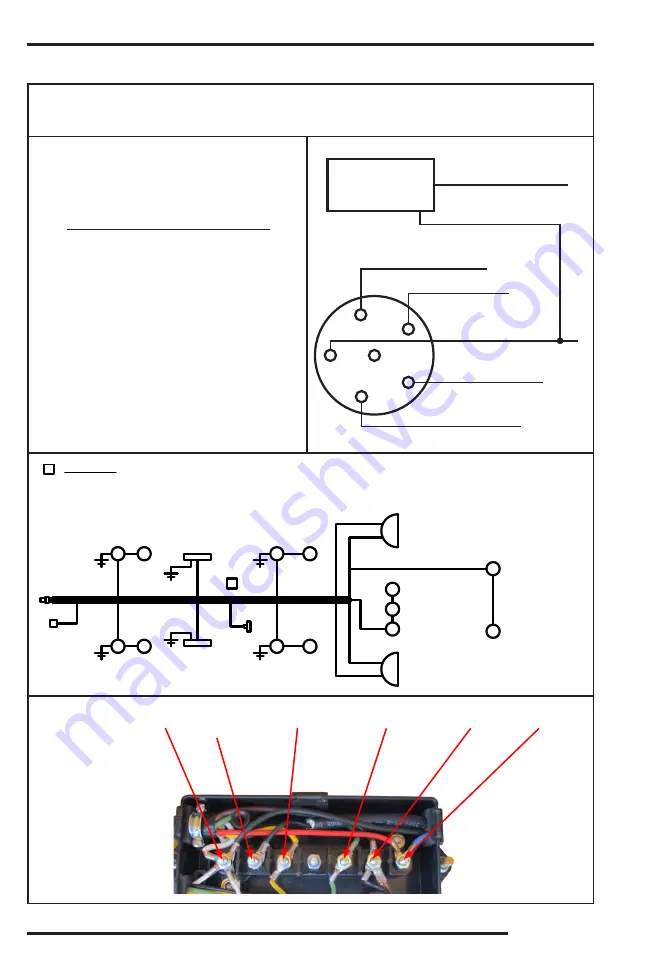
54
Copyright 3/20
Bandit
MODEL 1425
ELECTRICAL
TYPICAL ELECTRICAL WIRING DIAGRAMS
WIRING FOR STANDARD 6 PRONG PLUG
AND 6 WIRE MAIN CABLE
JUNCTION BOX
Left Turn & Brakes
(Y)
Ground
(W)
Power For
Brakes
(BL)
Right Turn & Brakes
(G)
Running Lights
(BR)
Electric Brakes
(BL)
RIGHT TURN-GREEN WIRE
LEFT TURN-YELLOW WIRE
GROUND-WHITE WIRE
RUNNING LIGHTS-BROWN WIRE
RT
LT
S
A
TM
GD
BREAKAWAY
SWITCH
POWER TO BREAKAWAY -
BLACK WIRE
ELECTRIC BRAKES-RED WIRE
6 Wire Main Cable Color Code
Red R (Brakes & Breakaway Switch)
White W (Ground)
Green G (Right Turn)
Yellow Y (Left Turn)
Brown BR (Running Lights)
Black BL (Power to Breakaway Switch)
BR
Y
BR
BR
R
BR
BR
R
BR
W
W
W
W
W
W
BR
LICENSE PLATE
LIGHT
ELECTRIC
BRAKES
ELECTRIC
BRAKES
RED MARKER
LIGHTS
RED MARKER
AMBER MARKER
LIGHTS
AMBER MARKER
LIGHTS
TAIL LIGHT & RIGHT TURN
TAIL LIGHT & LEFT TURN
J
G
BREAK AWAY
SWITCH
RED MARKER
LIGHT
RED MARKER
LIGHT
TRAILER PLUG
= JUNCTION BOX
END OF DISCHARGE
WIRES SPLICED
TOGETHER WHITE
WIRES GROUNDED
J
RED MARKER
LIGHT
BR
BR