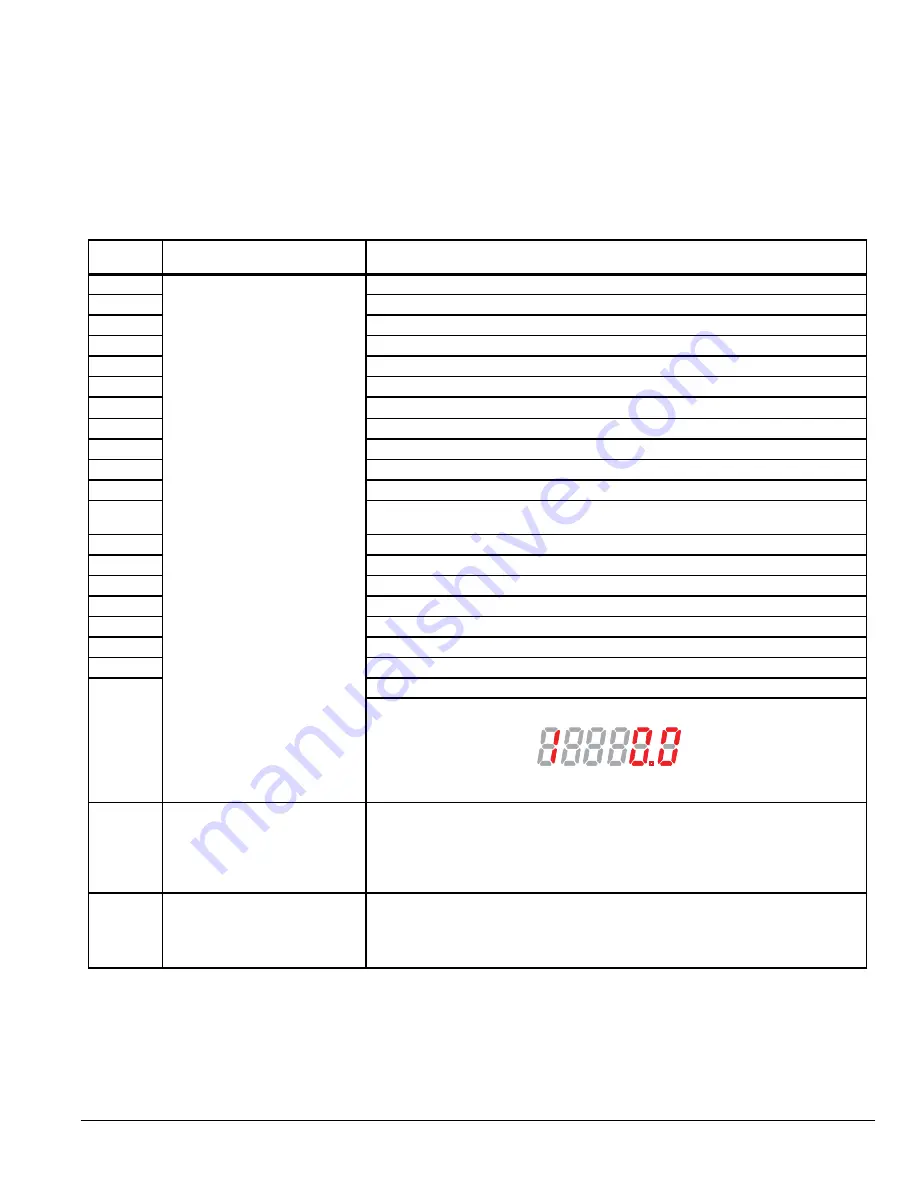
Parameter Descriptions 7-1
MN762
Chapter 7
Parameter Descriptions
7.1 Overview
Parameters P00 through P-45 are presented in this Chapter and each setting is explained. Selecting P00 and pressing
ENT/PROG accesses a read-only menu to monitor internal drive values. Once in the display view, the UP and DOWN arrows
will scroll between the read only variables shown below.
Table 7-1 Parameter Descriptions
Number
Name
(Display Level)
Value Range, Description and Preset Value
P00-01
Read Only
Analog Input 1 Value (100%=Max Vin).
P00-02
Parameters
Analog Input 2 Value (100%=Max Vin).
P00-03
Speed Reference Input -P-06 to P-06 (Hz if P-04=0, RPM if P-04≥1)
P00-04
Digital Input Status
P00-05
Reserved
P00-06
Reserved
P00-07
Motor Voltage
P00-08
DC Bus Voltage
P00-09
Internal Heatsink Temperature (in °C)
P00-10
Total Hours Run Time (Power applied)
P00-11
Run time since last trip. Reset on next enable after trip or power down.
P00-12
Run time since last trip. Reset on next enable after trip. Not by Undervolt trip or
power down (unless after a trip condition).
P00-13
Run time since drive enabled. Reset on next enable after disable.
P00-14
PWM Frequency. May be less than selected by P-21 if drive is hot.
P00-15
DC Bus Volts Log. Last 8 sample values (every 250 msec).
P00-16
Thermistor temperature log. Last 8 sample values (every 500 msec).
P00-17
Motor Current. Last 8 sample values (every 250 msec).
P00-18
Software ID, I/O Processor & Motor Control versions.
P00-19
Drive Serial Number.
P00-20
Drive Identifier. (Drive Rating & Type).
1=Analog Input 1 Value
Display Number Value Value (0.0% of Max Vin)
P-01
Motor Rated Volts
Range:
0, 20V to 250V= 230VAC
0, 20V to 500V= 460VAC (400VAC)
Preset:
230 or 400 (460V)
Rated (nameplate) voltage of the motor (Volts). Value limited to 250V for low
voltage drives. Setting to zero disables voltage compensation.
P-02
Motor Rated Current
Range:
25% to 100% rated drive current (A)
Preset:
4.3
The (FLA) Full Load Amps of the motor (listed on the motor nameplate). The drive
will fault on a motor overload if the value set in this parameter is exceeded.
.