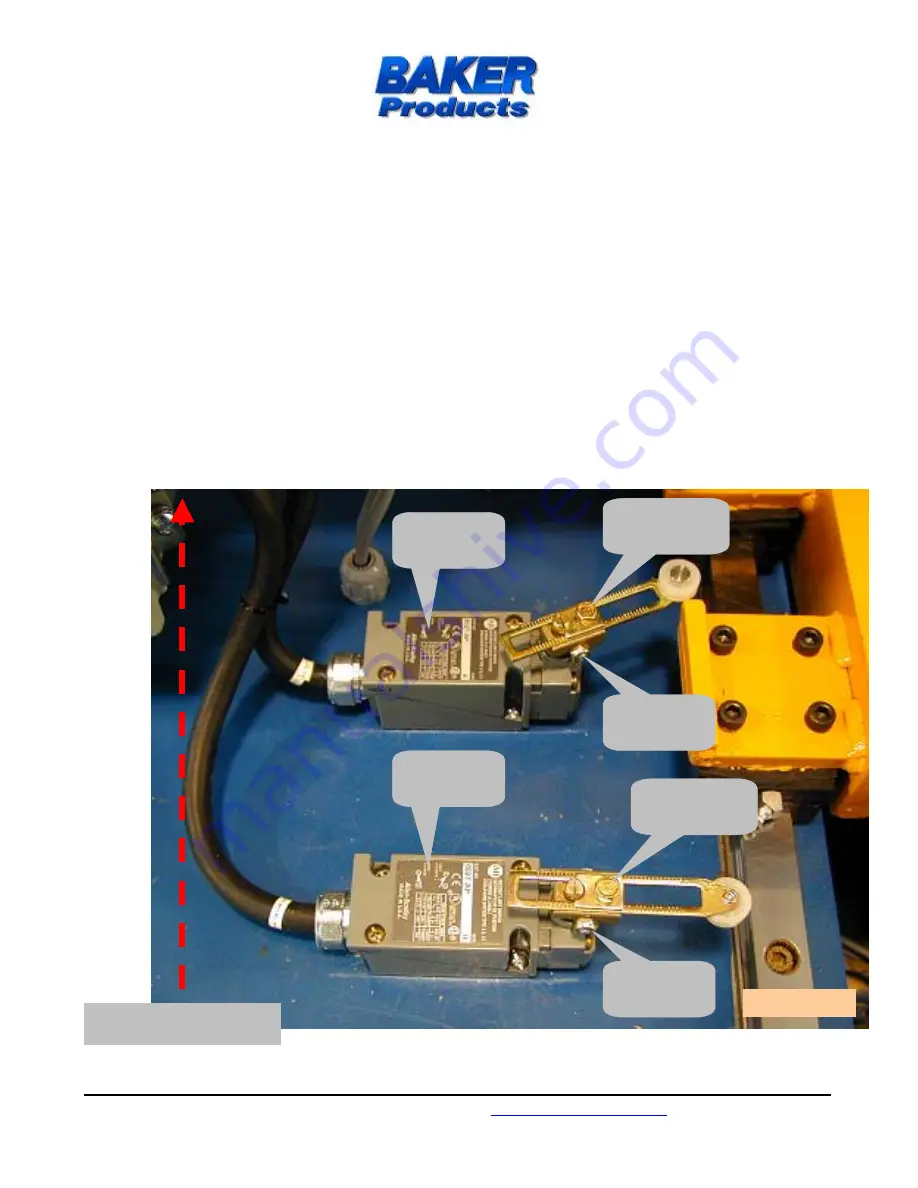
Baker Double Notcher - Rev 2, 09/07
;
WWW.BAKER-ONLINE.COM
23
Pusher Stroke
The stroke distance of the pusher can be adjusted to accept thicker or thinner wood,
depending on the positioning of the limit switches.
Turn the machine off and lock-out / tag-out the electrical panel.
The position of the front limit switch determines how far the pusher will move forward. If
an adjustment is necessary, loosen the angle adjuster nut and position the limit switch
forward for a shorter stroke, or backward for a longer stroke (
Figure 23
).
The position of the rear limit switch determines how far the pusher will move backward.
Adjustments to this switch are made using the same method used in setting the front limit
switch.
Note:
You may have to make a few test passes to achieve the correct stroke to fit your
material thickness. To achieve optimum performance, the pusher should not travel back
farther than necessary. You want just enough of an open area to allow material to drop into
position.
Figure 23
Front Limit
Switch
Rear Limit
Switch
Angle
Adjustors
Angle
Adjustors
Stroke
Adjuster Arm
Stroke
Adjuster Arm
Direction of Pusher