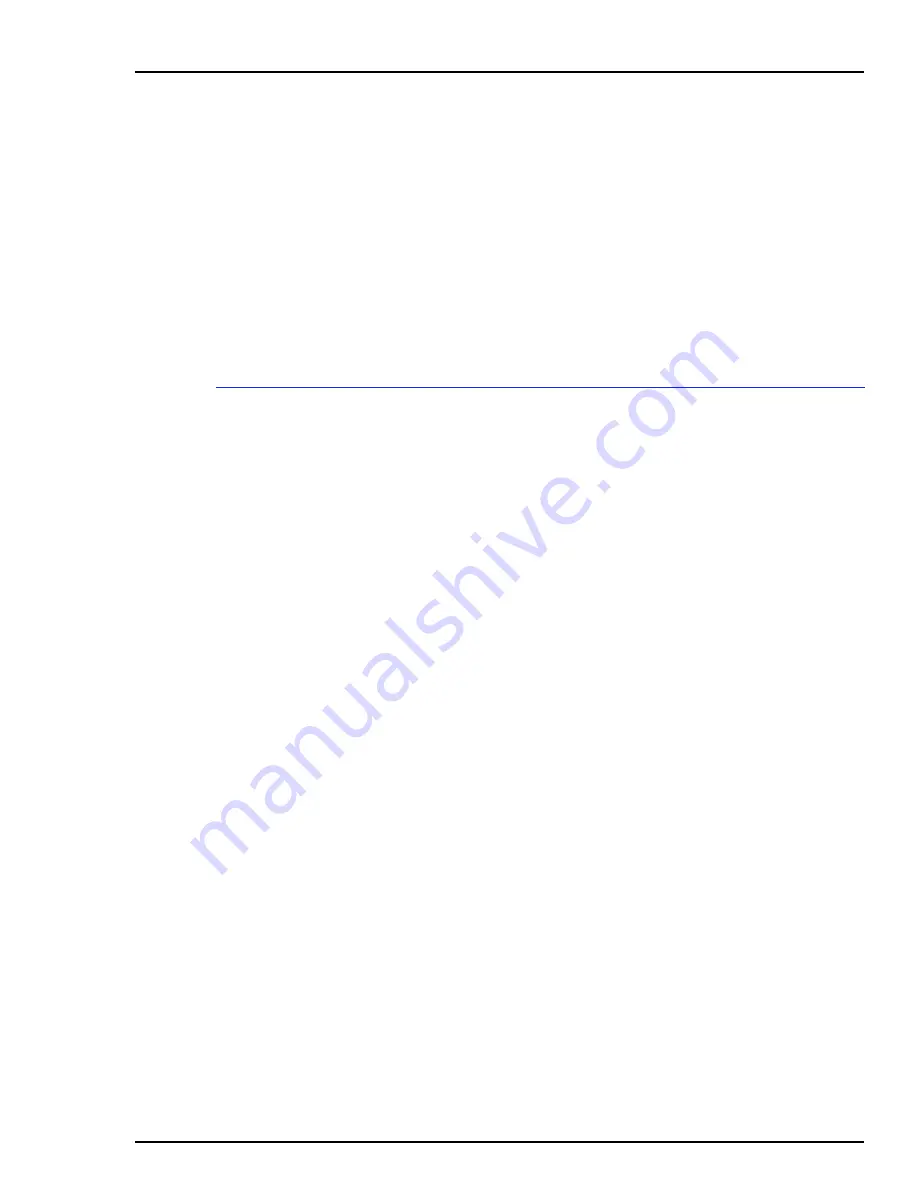
FUNCTION CODE 150 CALIBRATION
ANALOG CONTROL TUNING THEORY
I-E96-322A
B - 3
time. While the actuator is held against the 0% end of travel
stop, function code 150 records the LVDT differential voltage at
0% in specification S8. After recording the 0% reading, the
actuator moves at the selected stroke time to the position
demand from the multi-function processor module. The 100%
to 0% cycle repeats if the number of calibration cycles specified
in S7 is more than 1. When the calibration cycles are complete,
the actuator ramps to the position demand from the
multi-function processor module.
13. Allow the cycle to complete. Specifications S8 (0%) and S9
(100%) store the value of the LVDT differential voltages deter-
mined during the calibration cycle. The new values replace the
initial values or previous calibration values.
ANALOG CONTROL TUNING THEORY
Because there are many aspects of a control loop that affect the
system response, it is impractical to develop a mathematical
model to calculate the optimum controller gain. Control loop
characteristics that affect the system response are:
1. The characteristics of the servo valve, LVDT transformer
and hydraulic actuator such as operating specifications,
impedance tolerances, line loses, hydraulic system efficiency,
actuator spring tolerance and transformer performance.
2. Lag time inherent in a closed loop (feedback) control
system.
Response time and system stability are the primary concerns
in determining the controller gain. The objective of analog con-
trol tuning is to have a high frequency response while main-
taining system stability. The hydraulic servo module is a
proportional plus integral plus derivative controller (PID). PID
controllers readily meet the analog control tuning objectives.
The derivative action of PID controllers increases and stabilizes
the frequency response by compensating for lag time in the
control loop.
PID controllers are complex and tuning them is difficult. The
most common method (90 to 95 percent of the time) of tuning
PID controllers is the trial and error or practical method. The
HSS module is designed with the derivative and integral action
constant (not tunable). Tuning is accomplished by changing
the proportional gain. Increasing the proportional gain
decreases system stability and increases frequency response.
The practical method finds the gain that is one level below the
gain that causes instability (oscillation).