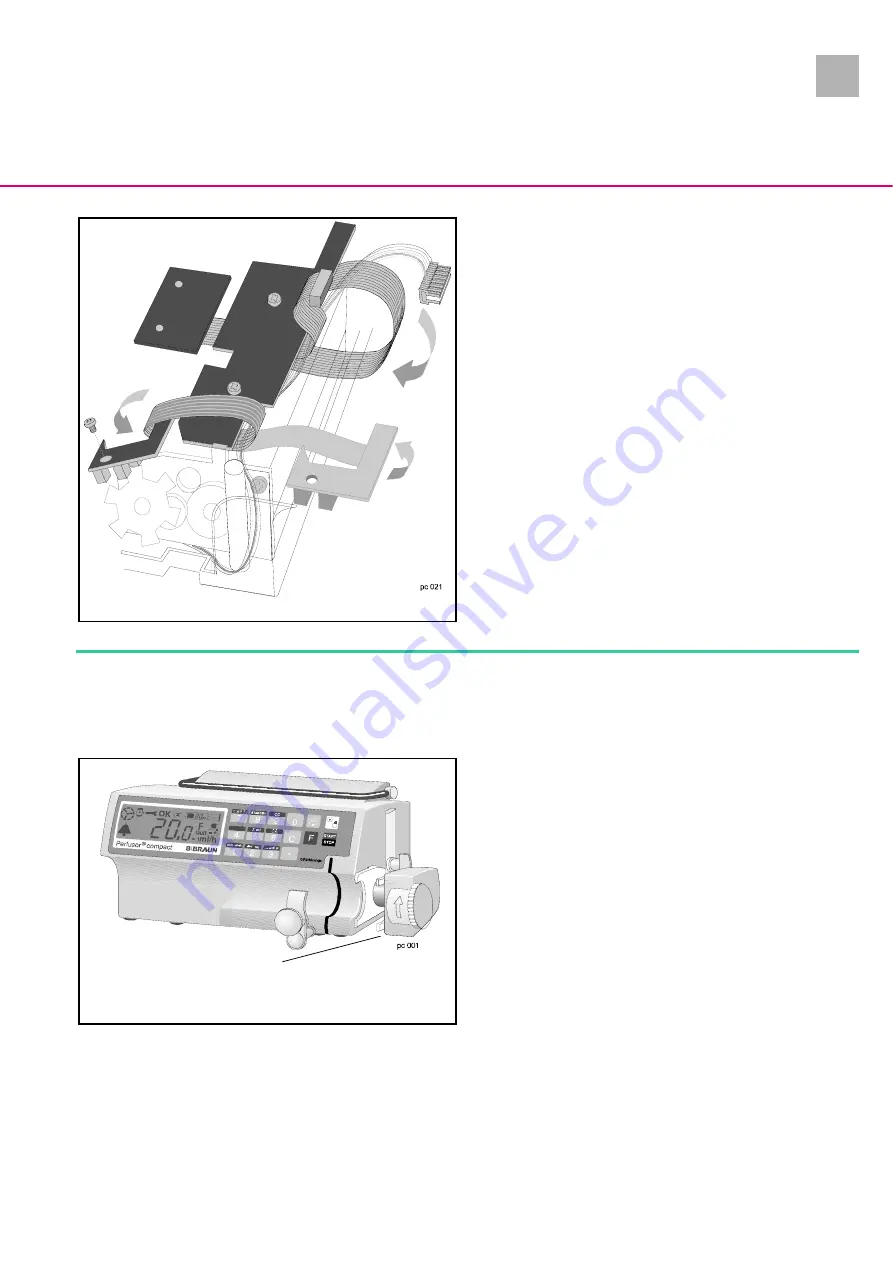
Unit Elements
4
Perfusor® compact, 2.1 gb
4 - 15
11. Calibrate in Service Program
(see „Calibration after Replace-
4.16 Drive Head
Designation
Ord. No.
Drive head, complete . . . . . . . . . . . . . . . . . . . . . . . . . . 3450 1720
Toggle . . . . . . . . . . . . . . . . . . . . . . . . . . . . . . . . . . . . . . . 3450 1711
Exchange
1.
Open toggle, pull out drive head and close toggle again.
2.
Pierce tamper-proof caps in drive head with a pointed screw
driver and remove caps.
Fig.: 4 - 18
Fig.: 4 - 19
Drive head with lock
and push-button sensor
Summary of Contents for Perfusor compact
Page 1: ...Service Manual Perfusor compact Version 2 1 english 0 0 10...
Page 10: ...Contact Persons 0 0 10 Perfusor compact 2 1 gb For your notes...
Page 14: ...System Overview 1 1 4 Perfusor compact 2 1 gb For your notes...
Page 20: ...Software 2 2 6 Perfusor compact 2 1 gb For your notes...
Page 54: ...Unit Elements 4 4 18 Perfusor compact 2 1 gb For your notes...
Page 60: ...Checks after Repair 5 5 6 Perfusor compact 2 1 gb For your notes...
Page 62: ...Maintenance 6 6 2 Perfusor compact 2 1 gb For your notes...
Page 69: ...Procedural Instructions on the TSC 8 8 5 Perfusor compact 2 1 gb...
Page 70: ...Procedural Instructions on the TSC 8 8 6 Perfusor compact 2 1 gb For your notes...
Page 72: ...Test Equipment and Special Tools 9 9 2 Perfusor compact 2 1 gb For your notes...
Page 76: ...10 4 Perfusor compact 2 1 gb For your notes...
Page 80: ...Appendix A A A 2 Perfusor compact 2 1 gb For your notes...
Page 82: ...Modification Instructions for Syringe Holder B B 2 Perfusor compact 2 1 gb For your notes...