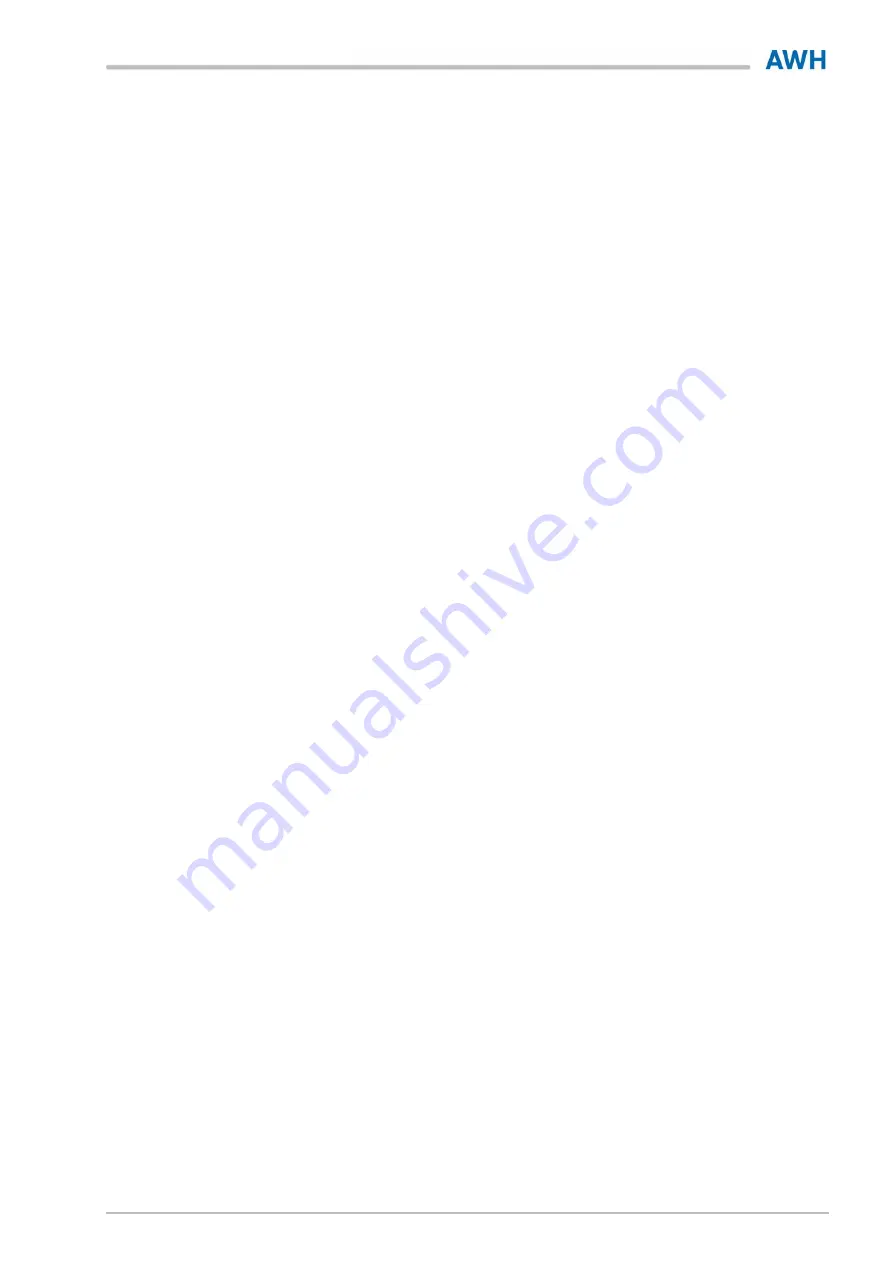
ATEX Retractor System TANKO-RT/-RTS
3 Design and Function
Translation - Operating/installation instructions 2020/01
31/121
If the compressed air fails for a significant period, this ensures that the retracted power cylinder does
not unintentionally lower into the container where it could collide with the internal fittings inside.
Before every movement of the power cylinder, the locking cylinder must first unlock it, i.e. compressed
air must be applied using a valve. Once the relevant end position is reached, the compressed air should
be disconnected and the locking cylinder moves to the locking position.
The program sequence for these movements must be defined in the customer control system.
When starting up the plant, including after a malfunction, it must be ensured that before extending or
retracting the power cylinder the opposite side is vented (i.e. placed under pressure) and the locking
cylinder is unlocked.
The owner must specify the control system (e.g. EMERGENCY STOP circuit) according to the specific
operational requirements. The corresponding guidelines and safety guidelines must be observed.
The typical operating pressure range for the side of the TANKO-RT/-RTS with cleaning medium flowing
through it is 3 - 6 bar (43.5 - 87 psi g), and the maximum pressure may not exceed 6 bar (87 psi g).
The consumption of cleaning water is significantly lower than that of conventional spray heads.
If the retractor system is used within the operating area of internal fittings, i.e. if there is a possibility of
collision between the extended spray head and moving internal fittings in the container, safe operation
of the retractor system is only possible with additional protection measures. The operator should also
conduct a hazard or risk assessment to identify and implement the functional requirements for the
retractor system controller, and, if necessary, additional monitoring equipment on the container to
prevent collisions between the spray head and any internal fittings. The following functions and
associated monitoring must be ensured:
–
Air pressure loss; the container with the retractor system must be removed for safety reasons.
–
The rest position of moving internal fittings must be defined and monitored.
–
When you switch off the cleaning medium, you should reckon with a run-on time of 1 minute until the
spray head comes to a stop. The spray head should only be retracted after this time.
–
The process may only be started again after completing a cleaning process if the power cylinder of
the TANKO-RT/-RTS is in the retracted (closed) position and the locking cylinder has locked it.
–
When the retractor system is in rest position (power cylinder in “retracted” position, G1 and G2
signal) and during operation of the plant, compressed air must be present at the pneumatic
connection E on the power cylinder (retract power cylinder).
–
The entire system for monitoring the position of the “retracted” power cylinder (two limit switches,
G1 and G2) must comply with at least the ignition protection system b2, EN ISO 80079-37 in the
currently applicable version, or equivalent.
–
The entire system for monitoring the position of the locking cylinder (limit switches J and K) must
comply with at least the ignition protection system b1, EN ISO 80079-37 in the currently applicable
version, or equivalent.