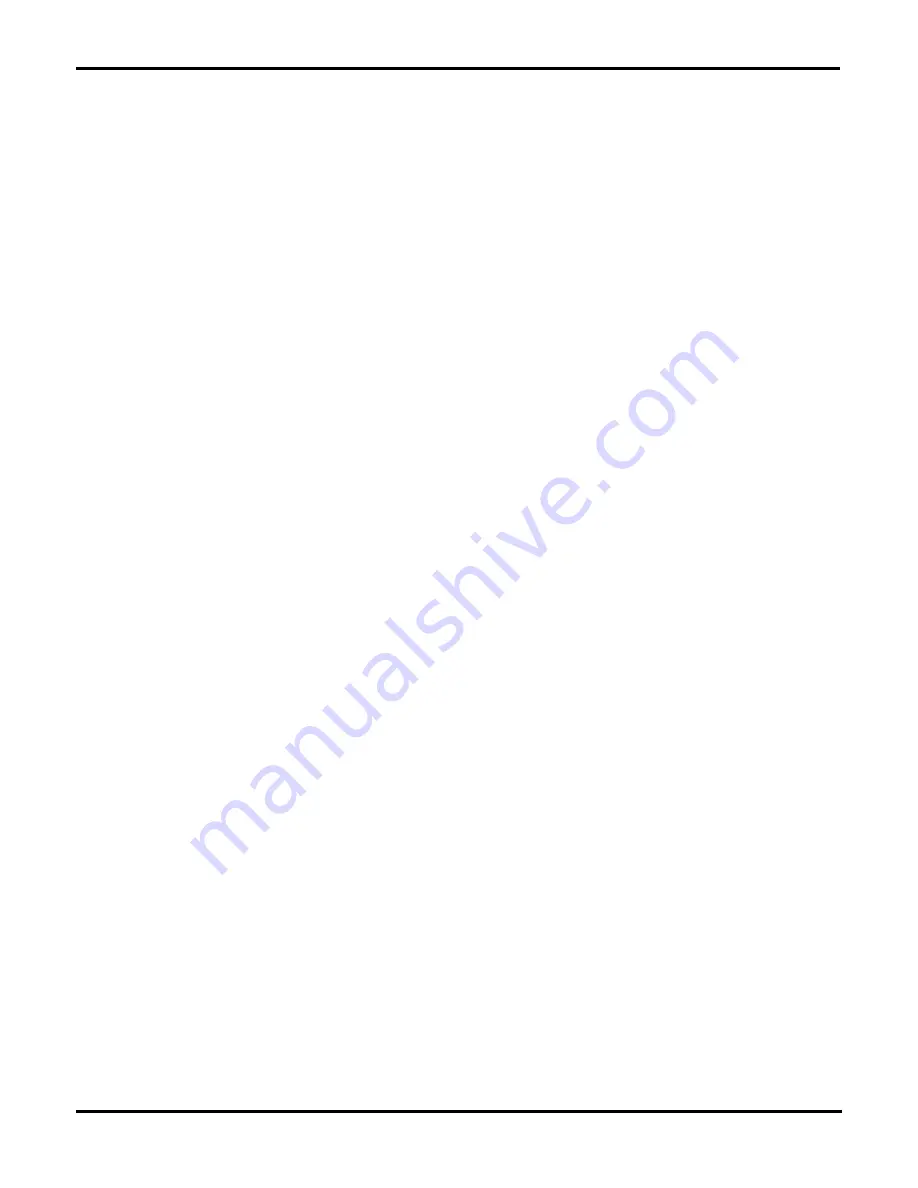
Chapter
A
: General Diagnosis
2
• Fuel lines, hoses, and fittings that are free of leak-
age and damage
• Battery, cables, and connections that are tight and
free of corrosion. Also, check the battery electrolyte
level and state-of-charge
• Secondary ignition cables, as well as the distributor
cap and coils, that are free of cracks, insulation
damage, corrosion, and loose connections
• Air filter element and ductwork that are clear and
able to supply a good flow of unrestricted air
• Emission control system components that are prop-
erly installed and connected. Repair any brittle,
burned, or damaged hoses and loose fittings
Also look the engine over for any signs of leakage. Ver-
ify coolant leaks by pressure testing the cooling system.
Check the level of the engine oil and coolant, and look
for indications of dilution and contamination. Oil dilution
is generally caused by raw fuel entering the crankcase.
Look for a high fluid level and thin consistency accom-
panied by the odor of gasoline. Coolant leaking into the
crankcase mixes with the oil to create a milky, brown-
colored emulsion. Either condition, dilution or coolant
contamination, indicates internal engine problems.
Start the engine and allow it to idle while listening for any
unusual noises. A stethoscope is a handy tool for iso-
lating top-end and bottom-end engine noises. To isolate
difficult noises, connect a timing light and listen. Bot-
tom-end noise will cycle in time with the flashing of the
light. Top-end sounds will be audible with every other
flash of the light.
While the engine is running, check the exhaust for indi-
cations of internal engine problems. Check for:
• Black smoke. This is caused by a rich air-fuel ratio,
and is often accompanied by the "rotten egg" smell
of an overworked catalytic converter
• Blue smoke. This indicates excessive oil burning
and often gives off a pungent odor
• Cloudy white exhaust. This is often the result of en-
gine coolant leaking into the combustion chamber.
Burning coolant also produces a distinctive chemi-
cal odor. Check the temperature gauge for over-
heating
• Listen closely to the sound of the exhaust system.
Be especially conscious of irregular pulses or
whistling sounds that may indicate valve problems
or a restricted exhaust
If everything looks good and there are no obvious prob-
lems, the vehicle is ready for a road test.
ROAD TEST
Whenever possible, let the customer accompany you on
the road test. The customer knows the vehicle and can
point out abnormal sounds, vibrations, and other an-
noyances that might be overlooked or considered nor-
mal.
Conduct a thorough road test; one quick lap around the
block is not enough. The engine must be brought to nor-
mal operating temperature, and the test drive should in-
clude a stop-and-go city driving cycle and a period of
cruising at highway speed. Proper road testing is ex-
tremely important for vehicles equipped with onboard
diagnostics. An incomplete test may not record all of the
intermittent, or soft, fault codes. A complete road test
should take about 15 minutes. If possible, use the same
route for all tests so that performance can be compared
before and after service, as well as to the performance
of similar vehicles. If a dynamometer is available, use it
to simulate the road test.
When a problem occurs while driving, note the operat-
ing conditions. Modulate engine and road speed to help
isolate the symptoms. Use the nature of the problem to
determine which diagnostic tests to perform. The tests,
and the order in which they are performed, depend on if
the suspected problem is in the:
• Electrical or electronic system
• Internal engine
• Ignition system
• Fuel system
• Emission control system
VEHICLE SERVICE INFORMATION
Resource materials should be readily available when
performing diagnostic procedures. Resource materials
and information should include:
• Service History
• Service Manuals
• Diagnostic Manuals
• Wiring Diagrams
• Technical Service Bulletins
• Online Technical Support
The vehicle service history may be found in various
ways. Ask the customer if they have copies of repair or-
ders for previous service work. OEM warranty systems
track all repairs completed under warranty and provide
good details of the problems serviced in the past.
Summary of Contents for ASE-A8
Page 2: ......