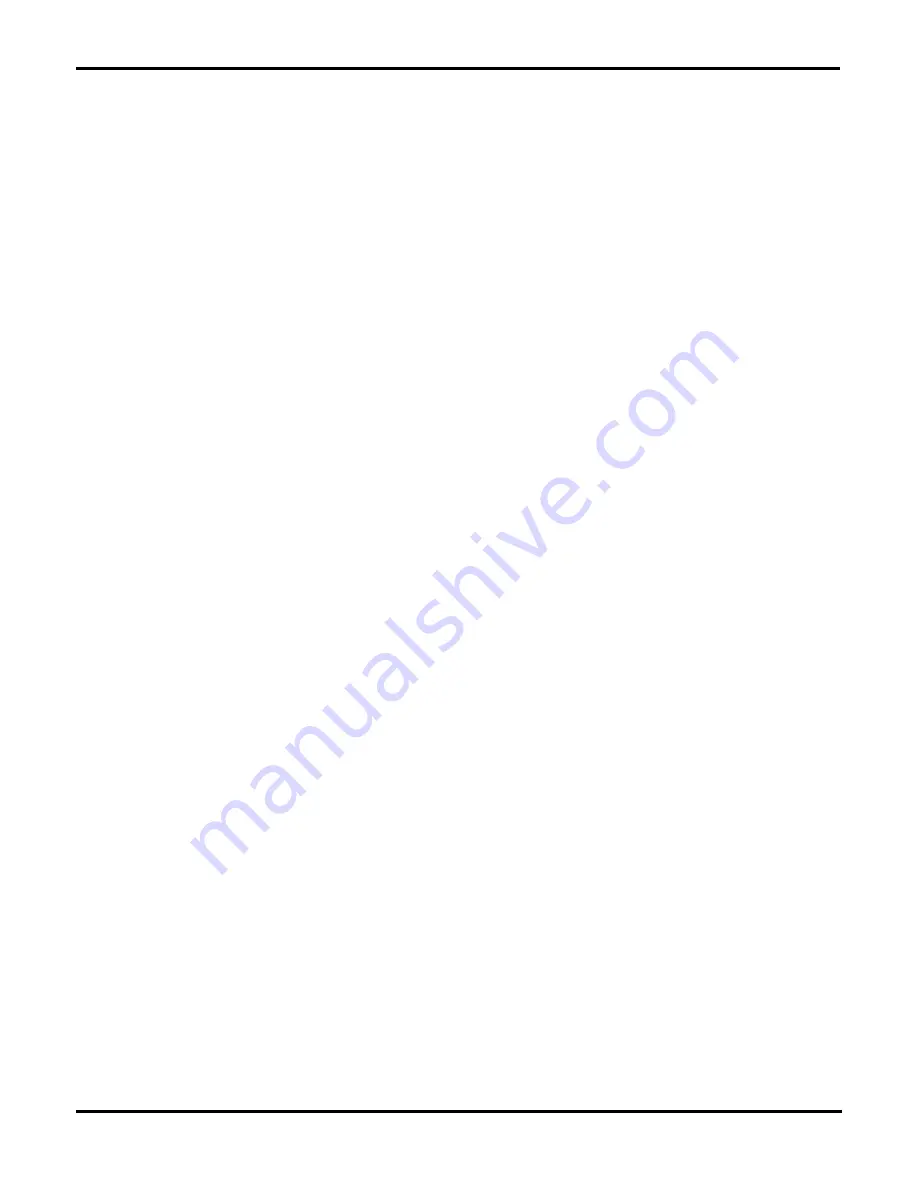
Chapter A: General Diagnosis
17
Adjustment Methods
Typical valve clearance specifications range from 0.004
to 0.025 inch (0.10 to 0.64 mm) for intake valves and
0.004 to 0.030 inch (0.10 to 0.76 mm) for exhaust
valves. Service Manuals may list valve clearances either
as hot or cold specifications, or both. If the valves are to
be set cold, check the coolant temperature. It should be
about the same as the air temperature, and the valve
cover should feel cool to the touch. To use a hot speci-
fication, the engine should be warmed to its normal op-
erating temperature. Common adjustment mechanisms
include:
• An adjustment locknut holding the rocker arm to the
rocker stud
• Replaceable adjustment shims located between the
camshaft lobes and cam followers
• Selective length pushrods
Adjusting Clearance on Overhead Valve
Engines
All late-model domestic overhead valve (OHV) engines
use hydraulic lifters. Adjustments are required only after
high-mileage operation has worn valve train parts be-
yond the adjustment range of the lifters, or when the
rocker arms, pushrods, or lifters were removed for ser-
vice. Mechanical valve lifters are still used on some im-
port and high-performance engines.
To access the lash adjusters, remove the valve covers.
When hot clearance specifications are provided, valves
can often be adjusted while the engine is running. Cold
clearances are set with the engine off and cooled down.
Both procedures are presented here.
Adjusting Clearances with the Engine Running
With many OHV engines, valve lash can easily and ac-
curately be adjusted with the engine running at its nor-
mal operating temperature. Remove the valve covers
and install a set of oil deflectors on the rocker arms to
prevent oil from splashing.
Obtain the proper hot valve clearance specifications
and have the necessary feeler gauges and wrenches
readily available. Work from one end of the engine to the
other and set all of the intake valve clearances first.
Then, repeat the sequence to adjust all of the exhaust
valves.
Hydraulic Lifters
Stud-mounted adjustable rocker arms used with hy-
draulic lifters can also be adjusted with the engine run-
ning.
Follow this procedure:
1. Starting with any valve, back off the rocker arm
locknut until the valve starts to clatter. At this point,
the valve has too much clearance.
2. Slowly tighten the nut until the clatter just stops.
This removes all lash, but does not compress the
plunger into the lifter body so there is no reserve
travel left to compensate for wear.
3. Slowly tighten the locknut in 90 degree increments
waiting about 10 seconds between steps to give
the lifter time to bleed down. The total amount the
locknut is tightened varies between engines.
Check the Service Manual for specifications.
Adjusting Clearances with the Engine Off
With the engine not running, the cylinder to be adjusted
must be brought up to top-dead-center (TDC) so that
both valves are closed. For engines with mechanical
lifters, turn the adjustment screw until there is a slight
drag on the feeler gauge blade. Some engines use in-
terference-fit adjustment screws or nuts that retain their
position once they are tightened. Others use a locknut
to hold an adjustment screw in place once the correct
clearance is established. On these engines, always
recheck clearance after tightening the locknut.
Two adjustment methods-selective length pushrods and
adjustable rocker arms-are used on engines with hy-
draulic lifters.
Mechanical Lifters
The following general procedure can be used to adjust
valve clearance with mechanical lifters on a running en-
gine:
1. Make sure the engine is running at its slowest idle
speed and is at normal operating temperature.
2. Insert a feeler gauge of the correct thickness be-
tween the rocker arm and valve stem. The feeler
gauge should pass through the gap with a slow,
steady drag:
• If force is required to insert the feeler gauge, or
if the engine starts missing when the gauge is
inserted, the clearance is too tight
• If the gauge slips through too easily, or if there
is a choppy, jerking feel as the gauge passes
through, the clearance is too loose
3. Turn the adjusting screw in or out as required.
4. Recheck the clearance after adjustment. If a sepa-
rate locknut is used, check the clearance once
again after tightening the locknut.
Summary of Contents for ASE-A8
Page 2: ......