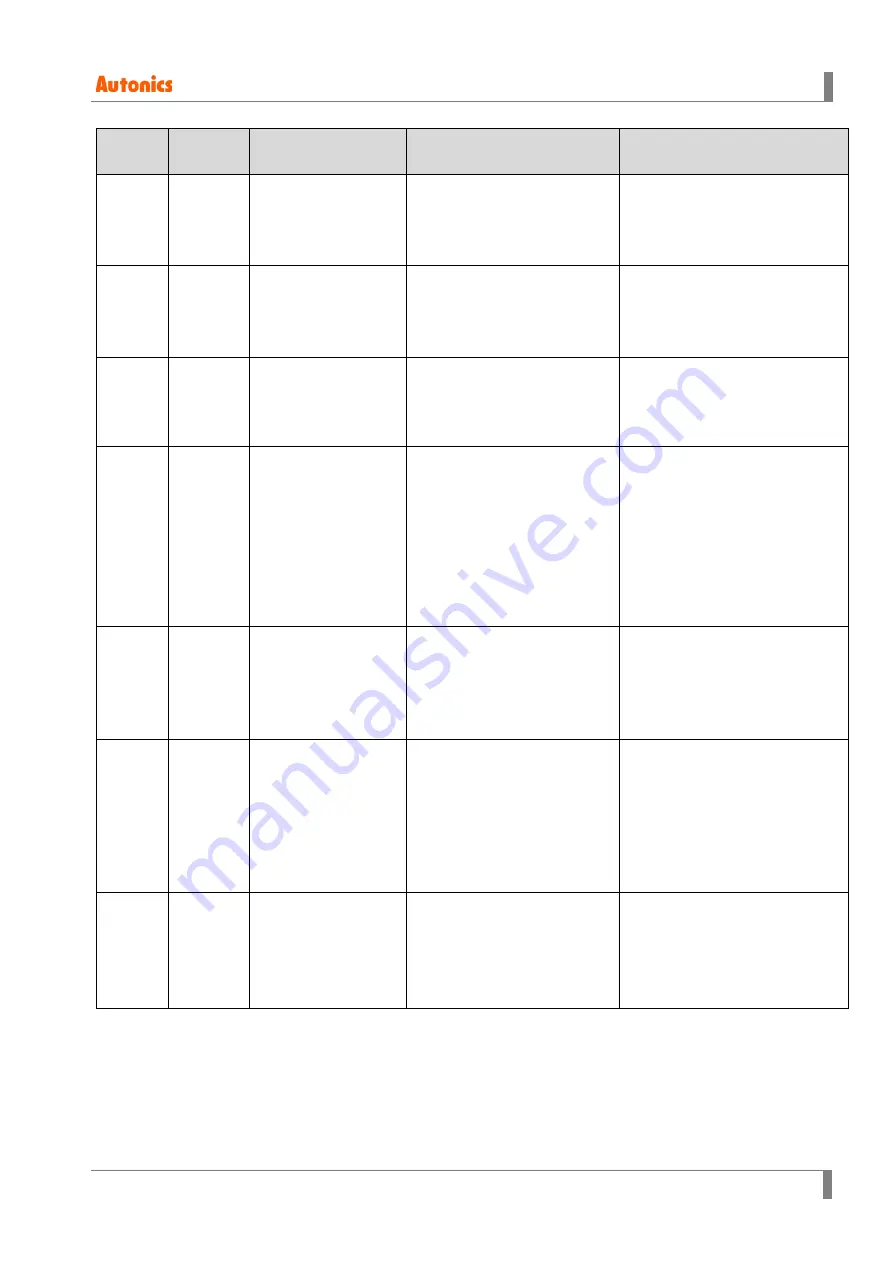
11 Protection Function
© Copyright Reserved Autonics Co., Ltd.
59
No. of
flashing
Alarm
type
Desctiptions
Causes
Troubleshooting
7 (
E7
)
Encoder
connection
error
When encoder cable
connection error
occurs at driver
1. Motor connector and cable
connection error
2. Burnout of line driver IC in
encoder
1. Check motor connector and
cable connection.
2. Replace the line driver IC in
encoder.
8 (
E8
)
Overvoltage
error
When input voltage is
over 24VAC +10%
1. Over load
2. Counter electromotive force
overflow due to rapid
deceleration
1. Change operation condition or
reduce load so that sudden
load fluctuation does not
occur.
9 (
E9
)
Under-
voltage error
When input voltage is
under 24VAC-10%
1. Low voltage
1. Change operation condition or
reduce load so that sudden
load fluctuation does not
occur.
10 (
EA
) Motor mis-
alignment
When motor is in
misalignment
1. Motor connector and cable
connector error
2. Burnout of line driver IC in
driver
3. Burnout of line driver IC in
encoder
4. Burnout of the inverter in the
driver
1. Check motor connector and
cable connection.
2. Replace the line driver IC in
driver.
3. Replace the line driver IC in
encoder.
4. Replace burned parts of the
inverter in the driver.
11 (
EB
) Command
pulse error
When input pulse is
over 3,500rpm
When input pulse is
input befor initial
motor alignment
1. Enter error of user command
speed input
1. Use recommended
specifications. (max. 3,000rpm
input)
2. Enter the speed value (PPS) by
checking the resolution.
12 (
EC
) In-Position
error
When position error
(over 1) is kept over 3
sec, after motor
stopped.
1. Over load
2. Lack of stop torque.
1. Change operation condition or
reduce load so that sudden
load fluctuation does not
occur.
2. Increase stop torque as 50% or
use the other motor with
higher torque.
13 (
ED
) Brake error
When brake failed to
operate
1. If there is no auxiliary
power applied.
2. Brake connector or cable
connection error
3. Brake is damaged
1. Check auxiliary power
2. Check brake connector and
cable
3. Replace brake motor