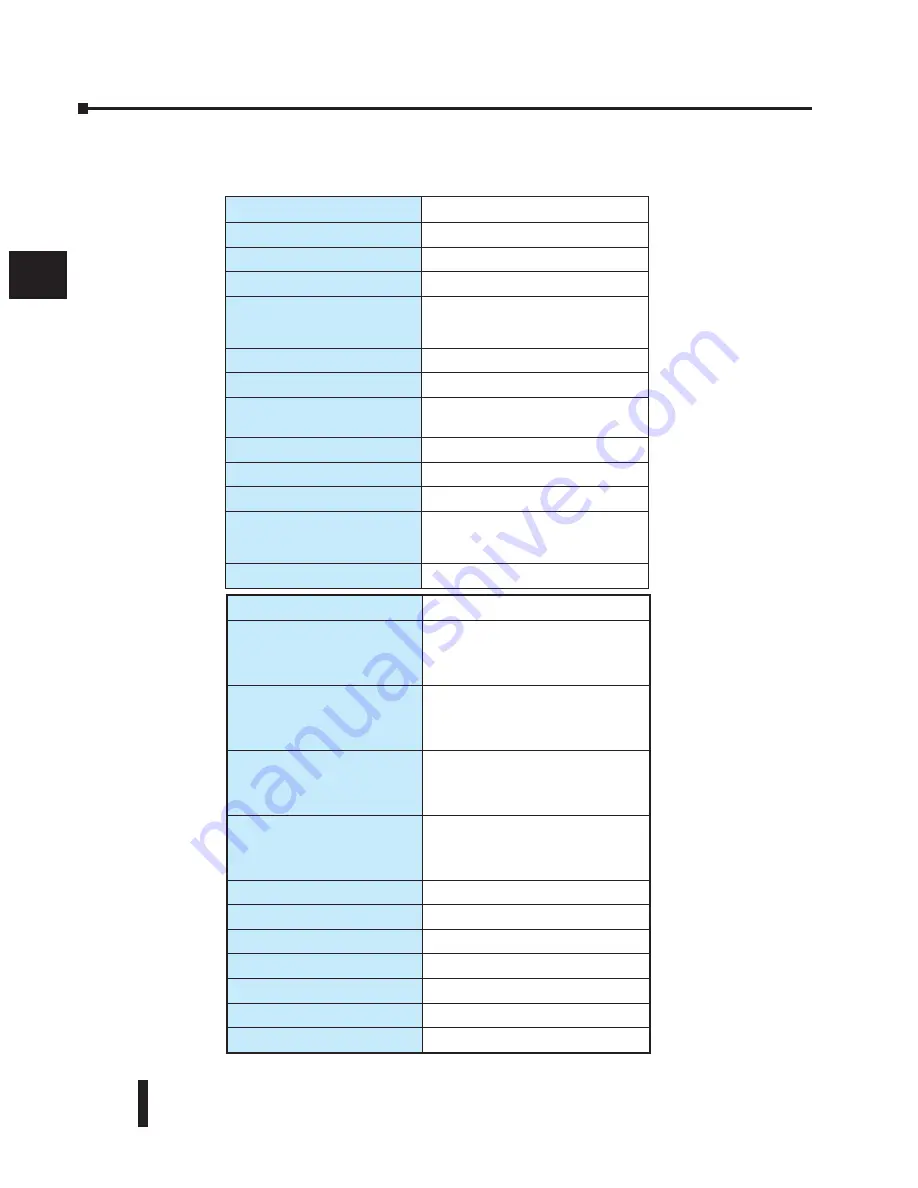
DL205 Installation and I/O Manual, 2nd Edition
3–62
Chapter 3: I/O Wiring and Specifications
1
2
3
4
5
6
7
8
9
10
11
12
13
14
A
B
C
D
F2-08DA-1 8-Channel 4-20mA Analog Output Module
Linearity Error (end to end)
±2 count (±0.050% of full scale) maximum
Full Scale Calibration Error
± 12 counts max. sinking @ any load
± 12 counts max. sourcing @ 125
load
± 18 counts max. sourcing @ 250
load
± 26 counts max. sourcing @ 400
load
Offset Calibration Error
± 9 counts max. sinking @ any load
± 9 counts max. sourcing @ 125
load
± 11 counts max. sourcing @ 250
load
± 13 counts max. sourcing @ 400
load
Maximum Full Scale
Inaccuracy @ 60
ºC
0.5% sinking (any load) sinking & sourcing @
125
load
0.64% sourcing @ 250
load
0.83% sourcing @ 400
load
Maximum Full Scale
Inaccuracy @ 25
ºC
(Incudes all errors and temp drift)
0.3% sinking (any load) sinking & sourcing @
125
load
0.44% sourcing @ 250
load
0.63% sourcing @ 400
load
Operating Temperature
32º to 140ºF (0º to 60ºC)
Storage Temperature
-4 to 158ºF(-20 to 70ºC)
Relative Humidity
5% to 95% (non-condensing)
Environmental air
No corrosive gases permitted
Shock & Vibration
MIL STD 810C 514.2
Noise Immunity
NEMA ICS3-304
Terminal Type (included)
Removable; D2-16IOCON
Number of Channels
8, single-ended
Output Ranges
4 to 20 mA
Resolution
12 bit (1 in 4096)
Output Type
Current sinking or current sourcing
Digital Output Points
Required
16 (Y) output points
(12 binary data bits, 3 channel ID bits, 1 output
enable bit)
Base Power Required 5VDC
30 mA
Maximum Loop Voltage
30 VDC
External Power Supply
18 to 30 VDC, 50 mA., class 2
(add 20 mA for each current loop used)
Source Load
0-400
@ 18-30 VDC
Sink Load
0-600
/18V, 0-900
/24 V, 0-1200
/30 V
Total Load
(sink + source)
600
/18 V, 900
/24 V, 1200
/30 V
PLC Update Rate
1 channel per scan maximum (D2-230 CPU)
8 channels per scan maximum (D2-240,
D2-250(-1) and D2-260 CPUs)
Conversion Settling Time
400 µs maximum (full scale change)