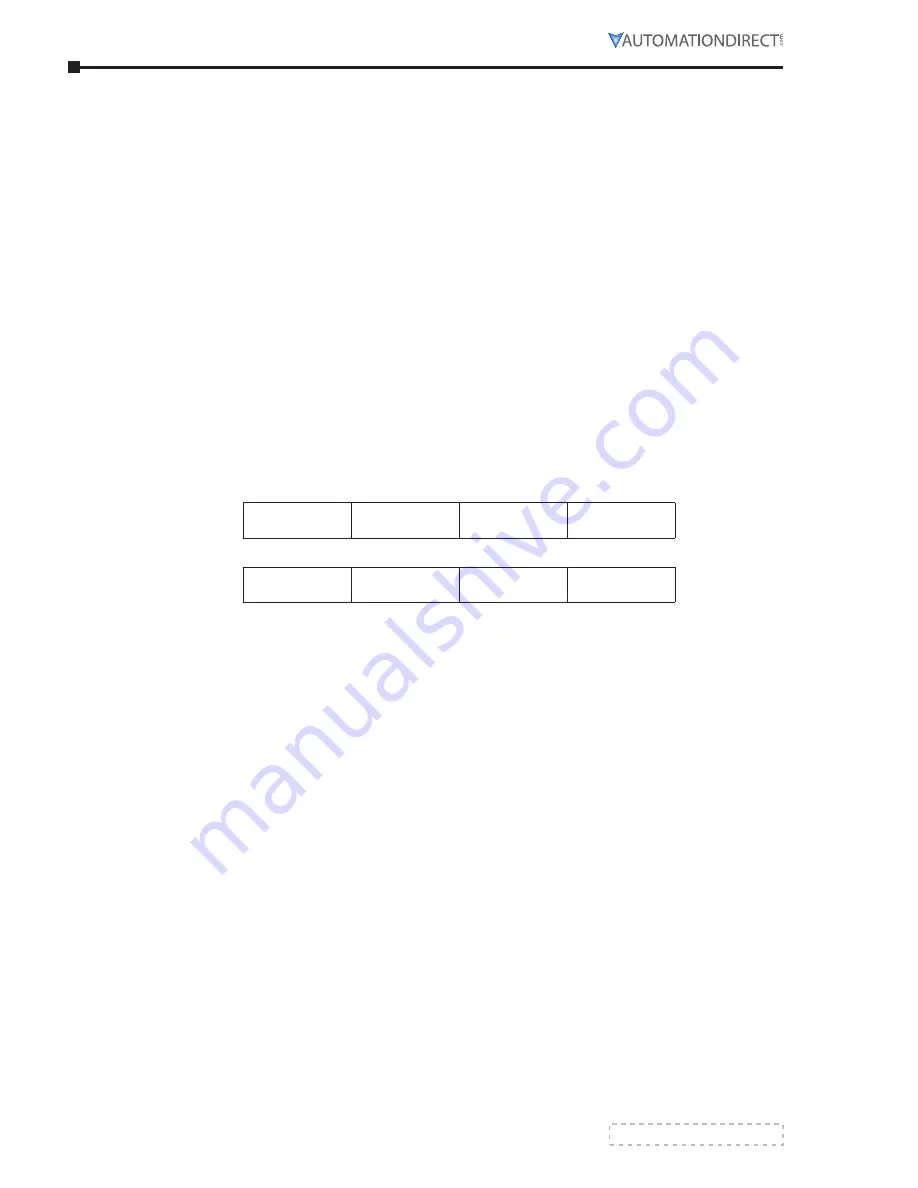
Page 5–4
Stellar
®
SR55 Series Soft Starter User Manual – 1st Ed, Rev F – 09/18/2019
Chapter 5: Communications
m
odbus
s
erial
C
ommuniCaTions
(
ConTinued
)
m
odbus
C
ommuniCaTions
C
onfiguraTion
The Modbus communication settings are accessible from the Device menu:
•
Device >> Networks >> Modbus Network Settings >> Address (1 – 32)
•
Device >> Networks >> Modbus Network Settings >> Baud (9600 – 115200)
•
Device >> Networks >> Modbus Network Settings >> Parity (Odd / Even)
•
(Data bits = 8, Stop bits = 1)
The communication parameters should be set before connecting the Modbus master.
T
ransmission
m
odes
ASCII and RTU transmission modes are defined in the Modbus protocol specification. SR55
uses
only the RTU mode
for the message transmission.
m
essage
s
TruCTure
f
or
rTu m
ode
The Modbus RTU structure uses a master-slave system for message exchange. In the case of
the SR55 system, it allows up to 32 slaves, and one master. Every message begins with the
master making a request to a slave, which responds to the master in a defined structure. In
both messages (request and answer), the used structure is the same:
•
Address, Function Code, Data and CRC
m
asTer
(
requesT
message
):
Address
(1 byte)
Function
(1 byte)
Request Data
(n bytes)
CRC
(2 bytes)
s
lave
(
response
message
):
Address
(1 byte)
Function
(1 byte)
Response Data
(n bytes)
CRC
(2 bytes)
a
ddress
The master initiates the communication by sending a byte with the address of the destination
slave. When responding, the slave also initiates the message with its own address. Broadcast
to address 0 (zero) is not supported.
f
unCTion
C
ode
This field contains a single byte, where the master specifies the type of service or function
requested to the slave (reading, writing, etc.). According to the protocol, each function is used
to access a specific type of data.
d
aTa
f
ield
The format and contents of this field depend on the function used and the transmitted value.
CrC
The used method is the CRC-16 (Cyclic Redundancy Check). This field is formed by two bytes;
where first the least significant byte is transmitted (CRC-), and then the most significant
(CRC+). The CRC calculation form is described in the Modbus RTU protocol specification.
Summary of Contents for Stellar SR55 Series
Page 1: ...Stellar SR55 Soft Starter User Manual SR55_UMW First Edition Revision F...
Page 2: ...Stellar SR55 Series Soft Starter User Manual 1st Ed Rev F 09 18 2019 BLANK PAGE...
Page 6: ...Page W 4 Stellar SR55 Series Soft Starter User Manual 1st Ed Rev F 09 18 2019 BLANK PAGE...
Page 8: ...Page H 2 Stellar SR55 Series Soft Starter User Manual 1st Ed Rev F 09 18 2019 BLANK PAGE...
Page 201: ...Stellar SR55 Series Soft Starter User Manual 1st Ed Rev F 09 18 2019 BLANK PAGE...
Page 202: ...Stellar SR55 Series Soft Starter User Manual 1st Ed Rev F 09 18 2019...