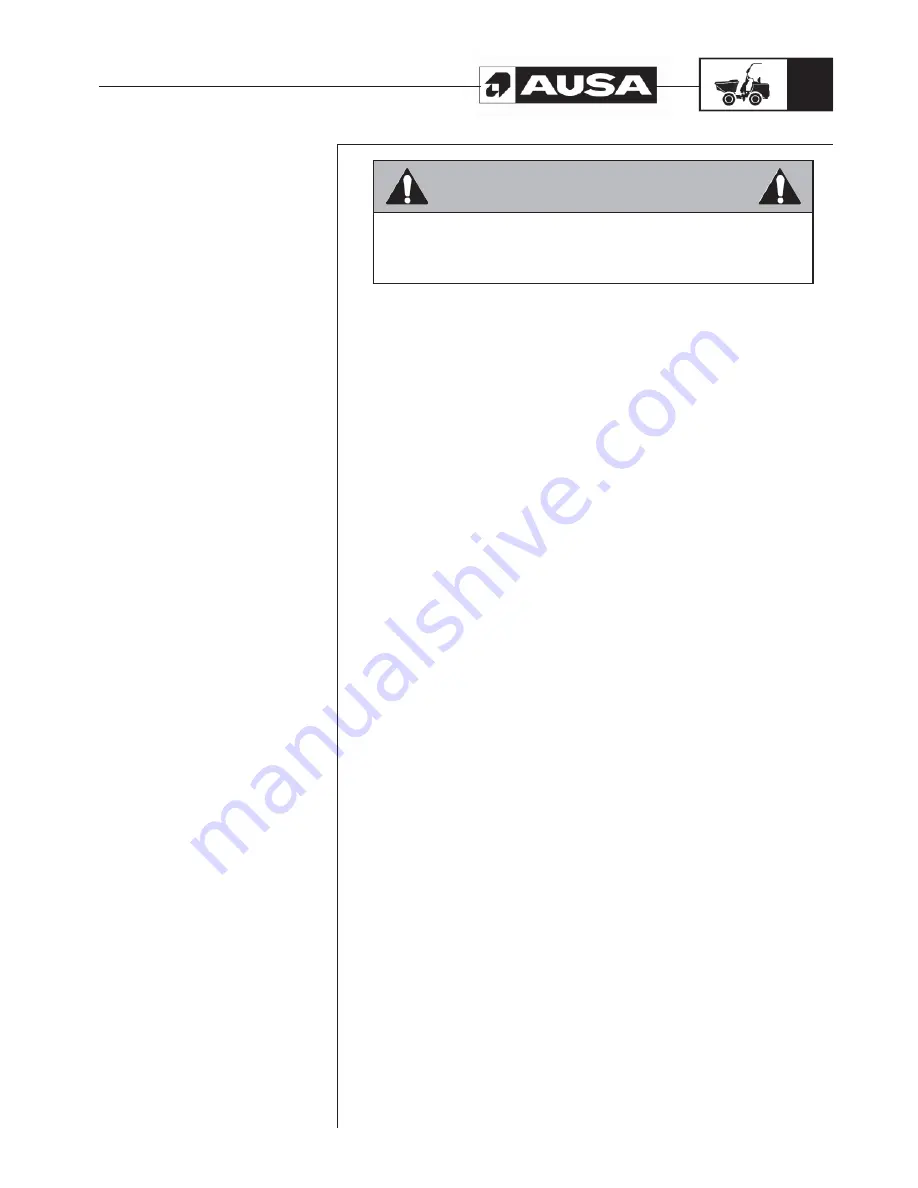
D 900 AP / D 1000 AP / D 1000 APG
27
Before starting
the dumper
WARNING
The pre-operation check is very important prior to operating the vehicle.
Always check the proper operation of critical controls, safety systems and
mechanical components before starting. If the pre-check operations are not
done as specified here, severe injury or even death might occur.
- Check tyre pressure and condition.
- Familiarise yourself with the controls and ensure that they function correctly.
- Verify that the steering operates freely.
- Activate the throttle pedal various times to ensure it operates freely. It must return
to the original position when released.
- Activate the brake pedal to ensure that the brakes function correctly. The pedal
must return to the original position when released.
- Ensure that the gear stick functions correctly.
- Check fuel, engine oil, hydraulic oil, coolant and brake fluid levels.
- Check for oil leaks on the engine, in the transmission components or in the
hydraulic circuit.
- Clean the lights and the lamps (if there are any).
- Ensure that the engine protector is correctly covered.
- Ensure that the seatbelts are correctly secured.
Before starting the day, carefully inspect this devices with special attention to:
- Cuts or threading on the belt
- Wear or damage to anchor points
- Poor functioning of the seat belt buckle or the retracting roller
- Loose threads or poor stitching
- If transporting cargo, respect the load capacity. Ensure that the cargo is properly
distributed.
- Review the engine parts while it is off. Check fixings.
- Check that the ignition switch, the headlights, the direction indicators, taillights
and acoustic warning and lights for reverse are functioning correctly.
- Start the engine and drive forward slowly a short distance and press the brake
pedal to check the brakes.
Correct any problem you may have found before operating the vehicle.
Consult an authorised AUSA dealer if necessary.
Summary of Contents for D 1000 AP
Page 1: ...D 900 AP D 1000 AP D 1000 APG OPERATOR S MANUAL ENGLISH ORIGINAL MANUAL ...
Page 2: ......
Page 3: ...D 900 AP D 1000 AP D 1000 APG Above chassis number 63163011 ORIGINAL MANUAL ...
Page 4: ......
Page 13: ...D 900 AP D 1000 AP D 1000 APG 11 Identification plates and labels ...
Page 63: ...D 900 AP D 1000 AP D 1000 APG 61 Electric diagram H1 ...
Page 64: ...D 900 AP D 1000 AP D 1000 APG 62 Electric diagram H2 ...
Page 65: ...D 900 AP D 1000 AP D 1000 APG 63 Electric diagram H3 ...
Page 66: ...D 900 AP D 1000 AP D 1000 APG 64 Electric diagram H4 ...
Page 68: ...D 900 AP D 1000 AP D 1000 APG 66 Hydraulic diagram D 900 AP D 1000 AP ...
Page 69: ...D 900 AP D 1000 AP D 1000 APG 67 Hydraulic diagram D 1000 APG ...
Page 71: ......
Page 72: ......