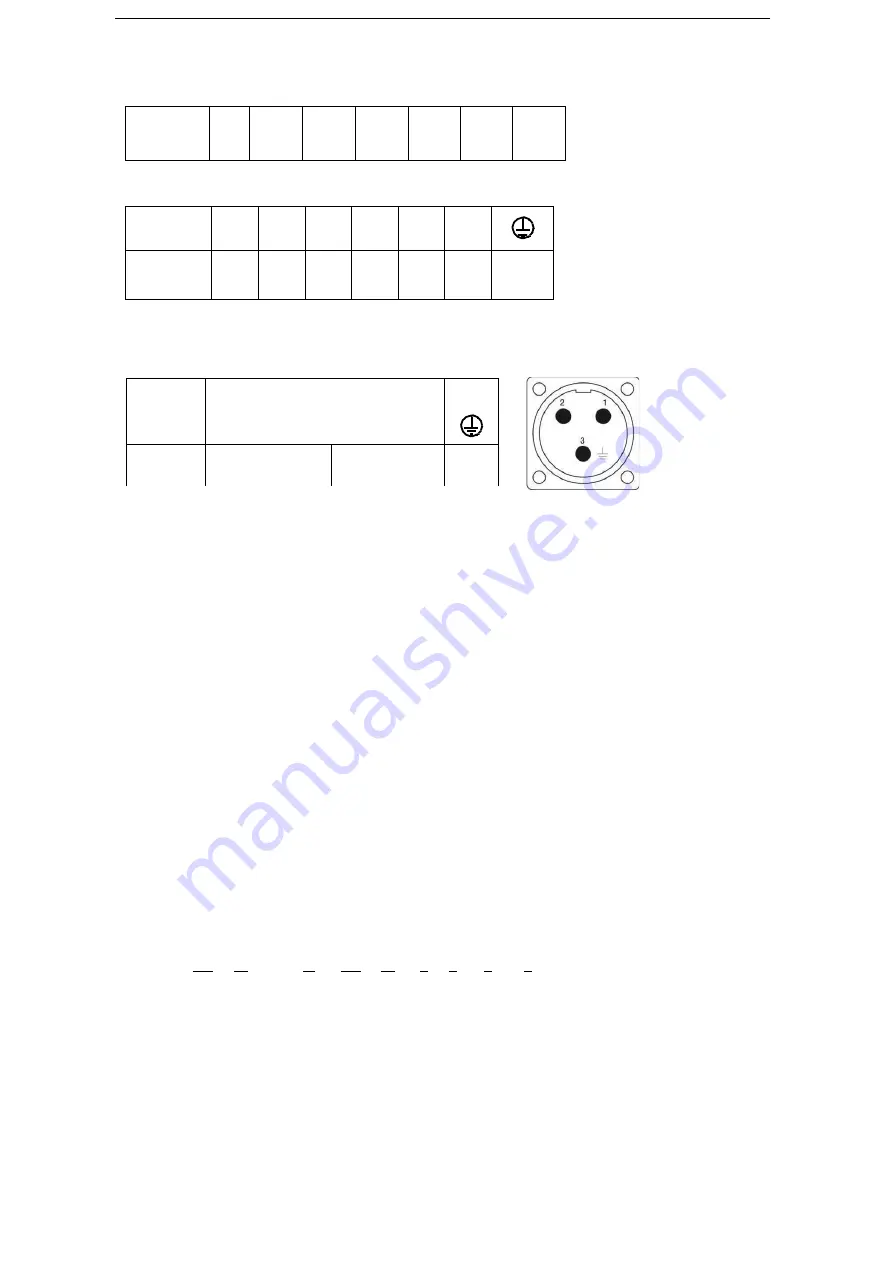
Socket No.
7
5
6
4
3
2
1
SD+ and SD- are data output signals; E+ and E- are battery leads.
●
Socket (with 7 prongs) for rotatable transformer (R)
Signal
R1
R2
S1
S3
S2
S4
Socket No.
2
3
4
5
6
7
1
R1-R2 are primary signals, S1-S3 and S2-S4 are secondary signals.
III. Socket for Safe Brake (Band-type Brake):
Safe brake parameters allocated for Seat 110
Working pressure: 24VDC (-15%-+10%), working current:
≤
0.6A, braking torque:
≥
8Nm Safe brake parameters allocated for Seat 130
Working pressure: 24VDC (-15%-+10%), working current:
≤
0.6A, braking torque:
≥
12Nm Safe brake parameters allocated for Seat 150
Working pressure: 100VDC (-15%-+10%), working current:
≤
0.4A, braking torque:
≥
30Nm
Description of Model Selection of Servo Motors
● Parameter characteristics
Seat (mm): 80, 110, 130, 150
Rated torque (Nm): 1.3-27
Rated speed (rpm): 1500,2000,2500,3000
Rated power (kW): 0.4-5.5
Standard
matching
feedback
elements:
incremental encoder (2500C/T)
Safe brake: matching
Insulation level: B
Protection level: closed self-cooling IP65
Number of pole-pairs: 4
Installment mode: flange plate
Ambient temperature: 0-55
0
C
Ambient humidity: < 90% (without condensation)
Excitation mode: permanent magnet
Working voltage of adaptive driver (VAC): 220
●
Description of type codes of LB series servo motors:
110
ST
–
M
020
30
L
F
B
Z
(1)
(2)
(3)
(4)
(5)
(6)
(7)
(8)
(9)
(1) Seat No.
(2)
AC Permanent magnet synchronous servo motor
(3) Type of feedback element: photoelectric encoder
(4) Rated torque: three figures ×0.1Nm
(5) ated speed: two figures ×100rpm
(6) Working voltage of the driver (VAC): 220
Power supply
VDC(direct current power supply)
without requirements on polarity access.
Socket No.
1
2
3
70