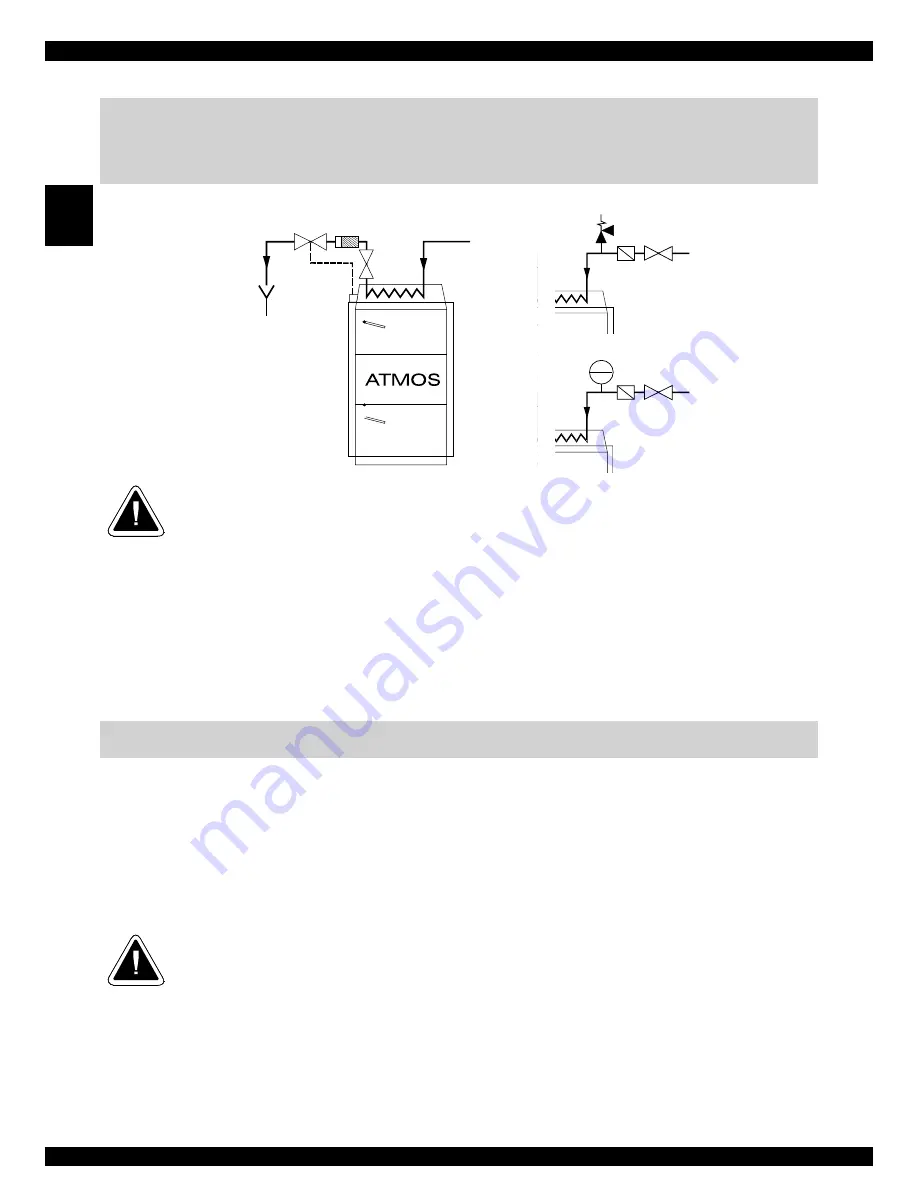
www.atmos.cz
26-GB
Instruction manual - GB
GB
27. Connection of overheat protecting cooling loop with a safe-
ty valve Honeywell TS 131 - 3/4 ZA or WATTS STS20
(valve opening temperature 95 - 97 °C)
CAUTION
– in compliance with the EN ČSN 303-5, the cooling loop must not be used for
any other purpose than overheat protection (never for heating hot potable water).
The TS 131 - 3/4 ZA valve or WATTS STS 20 valve, the sensor of which is placed in the rear
of the boiler, prevents overheating in the following way: if the boiler water temperature rises above
95 °C, the valve opens and allows water from public water supply system to enter the cooling loop.
This water then absorbs the excessive energy and exits to the sewer. In case that a non-return flap
valve has been installed to the cooling loop water inlet for the purpose of preventing reversed water
flow (which might be caused by pressure drop in the public water supply system), the cooling loop
must be fitted with a 6 - 10 bar safety valve or with an expansion vessel of minimum 4 l volume. The
boiler must be protected against overheating at all times. If not, its damage or burst may occur.
28. Operating instructions
Preparing boilers for operation when burning pellets
Before putting the boiler in operation you must make sure that the system is filled with water
and bled. Boiler must always operate in accordance with the instructions contained in this manual to
achieve high quality and safety of the functionality of the system.
The system may only be operated
by adult persons.
The commissioning of the boiler must be done in accordance with this manual and
the operation manual attached to the pellet burner by a qualifiedperson.
CAUTION - The boiler may only be put in operation by a qualifiedpersoninaccord
-
ancewith valid regulations and standards, trained by the manufacturer.
Before we proceed heating-up with the pellets do some operations.
Ensure that all lids and doors are fully closed. Check that the burner is well drawn towards the
boiler through its gasket and the limit switch position-stop is in its place. Also check the tube between
the burner and conveyor so that it is stretched and at a sufficient angle to ensure that the pellets can
drop without difficulty into the burner.
They must not cumulate inside the tube!
The screw convey-
or should be at a maximum of 45° angle otherwise the boilers might not reach their nominal output.
Honeywell TS 130– 3/4 A (95°C) valve
WATTS STS 20 (97°C)
sewer
filter
valve
water supply from
public water system
pressure: 2 - 6 bar
temperature: 10 – 15°C
safety valve 6 – 10 bar
non-return
flap valve
non-return
flap valve
expansion tank of min. 4 l volume