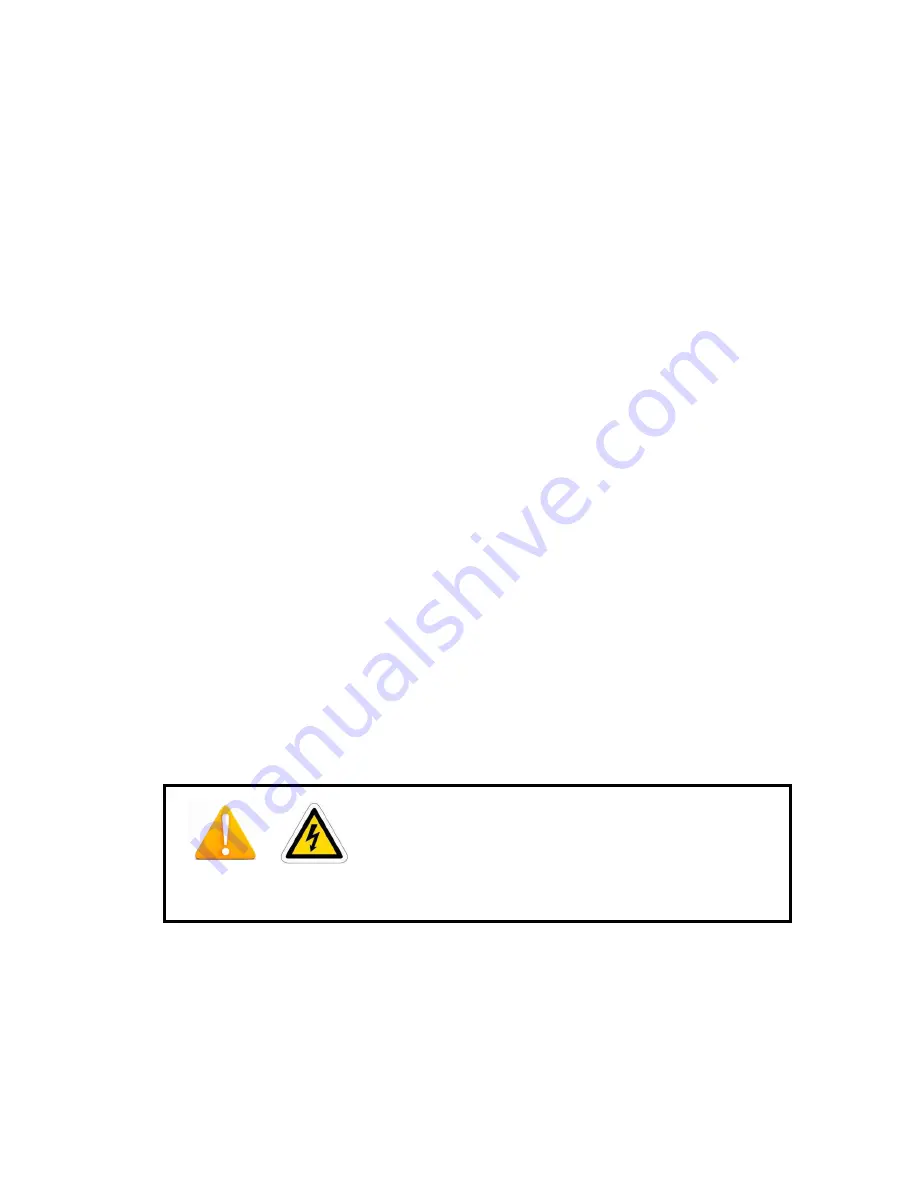
22
inflatable function (if have) parameters to be set according to the actual situation.
If the inflatable too much, vacuum lid opens automatically, the program will
automatically terminate.
If Inflatable excessive vacuum reaches higher than 0.06Mpa and begin to seal, the
sealing function may not be completed properly.
sealing function parameters can be set between 1-3 seconds.
If the bags are exceptionally thick or very thin, the temperature can be adjusted to
select high-grade or low-grade.
Note: If the sealing time parameter is too long, the temperature of the heating
plate will be a sharp rise, which will greatly shorten the heating plate and silicone
life.
sealing function parameters have a great impact on the sealing quality, need to
slowly adjust from low to high.
cooling function parameters according to the thickness of the case of the bag
disposed between 1-3 seconds.
5). For packaging liquid products
Machine can be used for packaging liquid products, such as soups, sauces, etc.,
when the packaging of such products, pay attention to spillage.
Liquid will arrive boiling point when the temperature is higher or it reaches a low
pressure, the high temperature of the liquid product will soon reach boiling point
when packed and thus the degree of vacuum may be lower.
We recommend to cool the liquid products before packing to ensure the best
vacuum effect of the product.
6.the best packaging
use the correct style and good quality vacuum bag.
pocket to leave enough space at least 30mm.
flat vacuum bag placed on a hot plate or silicone.
If the product is lower than the heating plate or silicone lot, put correct number of
pads (if have)to the vacuum chamber.
7.Machine maintenance
Warning! Risk of electric shock!
You must be completely disconnected from the mains before machine
maintenance.
To prolong the life of the machine, prevent failure and achieve the best packaging
effect, the machine's daily maintenance is necessary. If the machine is frequently used
(more than 4 hours per day), it is recommended every six months to give a professional
maintenance. If not, once a year full maintenance (depending on the location, the
environment and on the product).
Machine must be completely disconnected power before Maintenance, the power
plug is removed from the wall-mounted socket.