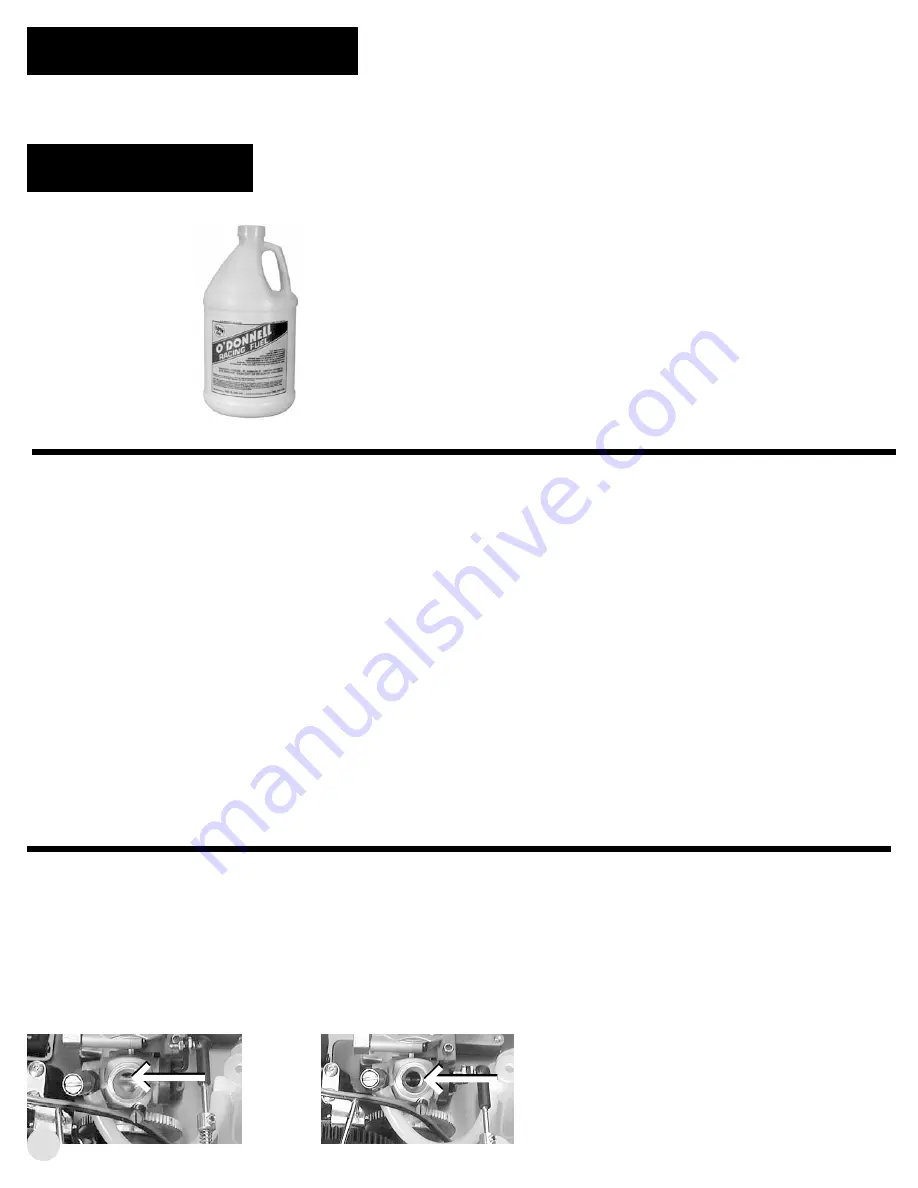
%()25(<28581<285758&.
PLEASE READ THIS SECTION OF THE MANUAL FIRST. AFTER YOU READ THIS SECTION, READ YOUR ENGINE
MANUAL BEFORE YOU START YOUR ENGINE
),1$/$'-8670(176
MAKE THESE ADJUSTMENTS BEFORE RACING
MODEL CAR FUEL
The proper fuel is very important for
long engine life. Improper fuel can cause
hard starting , poor performance, and ex-
cessive wear on the engine. The fuels we
recommend for R/C car use are: O’Donnell
Racing fuel, Duratrax Red Alert fuel, Blue
Thunder Race Formula, FSR fuel, Trinity,
Byron’s Originals, and Traxxas Top Fuel.
There are many other racing fuels, how-
ever, they must meet two requirements.
1) The fuel must contain at least 18%
of both castor and synthetic oils.
2) You should try to keep the nitro
(nitromethane) between 10% to 20%. The
best fuels also contain rust and corrosion
inhibitors, anti wear agents, anti foaming
agents and lubrication additives.
3) IMPORTANT: DO NOT use any
type of airplane fuels. Airplane fuels may
not have the necessary oil types and ra-
tios needed for R/C cars.
GETTING THE RADIO READY
Read your radio instructions that come
in the box with your radio. You should un-
derstand the operation of your transmitter.
Place eight of your AA cells in the trans-
mitter, and put four more in the receiver
pack, at the rear end of the truck.
It is impor tant that all of the AA radio
batteries are strong or fully charged. Al-
ways check the path and the condition of
the battery pack wires as well as the switch
wires. A melted wire can cause a short –
circuit and lead to a loss of control. Large
metal objects such as chain link fences,
light poles, cars, vans, trailers or even fluo-
rescent lights can occasionally cause lo-
cal interference by momentarily blocking
or reflecting a signal.
TESTING THE TRANSMITTER
Important: Always turn your transmit-
ter on first and off last. Remember this rule.
If you start your truck before turning on
your transmitter then you will lose con-
trol of the truck and damage your en-
gine quickly. Test the following radio func-
tions without the engine running.
These following steps will help you under-
stand the operation of your transmitter.
1.
Turn on the transmitter . You should see
an indicator light showing that the radio is
on.
2.
Turn the car receiver battery pack
switch on. Both the steering servo and the
throttle servo should move to their respec-
tive neutral settings.
3.
Turn the steering wheel on the trans-
mitter left and right. The front wheels should
turn left and right (when viewed from be-
hind), then go to a perfectly straight-ahead
position when the wheel is released. If
they’re a little off, you can set them with
the steering trim control on your transmit-
ter. If your servos are slow, you might want
check your batteries before you run.
4.
Pull on the throttle trigger, which should
open the throttle on the engine.
5.
Push the throttle trigger forward, which
will activate the brakes.
6.
Hold the throttle open and roll the truck
on the ground. The truck should roll freely.
While it is still rolling , push on the brakes.
The truck should come to an immediate
stop. If these steps do not produce these
results refer to the linkage assembly setup
in this manual.
CHECKING THE CARBURETOR
Let’s check the carburetor linkage be-
fore you fire up the engine for the first time.
Pull off the air filter. Turn the transmit-
ter on first, followed by the truck.
With your finger off the throttle, which
is the neutral position, the throttle should
be almost closed, with an opening about
1/32” (.71mm), as shown below.
Pull the throttle wide open and look into
the carburetor and see if it’s opening all the
way up. If you don’t see the gap shown
below, then adjust the “throttle trim adjust-
ment” on your transmitter according to the
radio manual, or adjust the linkage shown
to you earlier in this manual to achieve full
throttle.
When everything is adjusted OK, turn
the switch off in your truck first, followed by
your transmitter. You must remember to turn
off your truck’s electronics every time in this
order.
Now, place the air filter back on your
carburetor and fasten it back down with a
new tie wrap.
One of several recom-
mended racing fuels:
O’Donnell Racing fuel
28