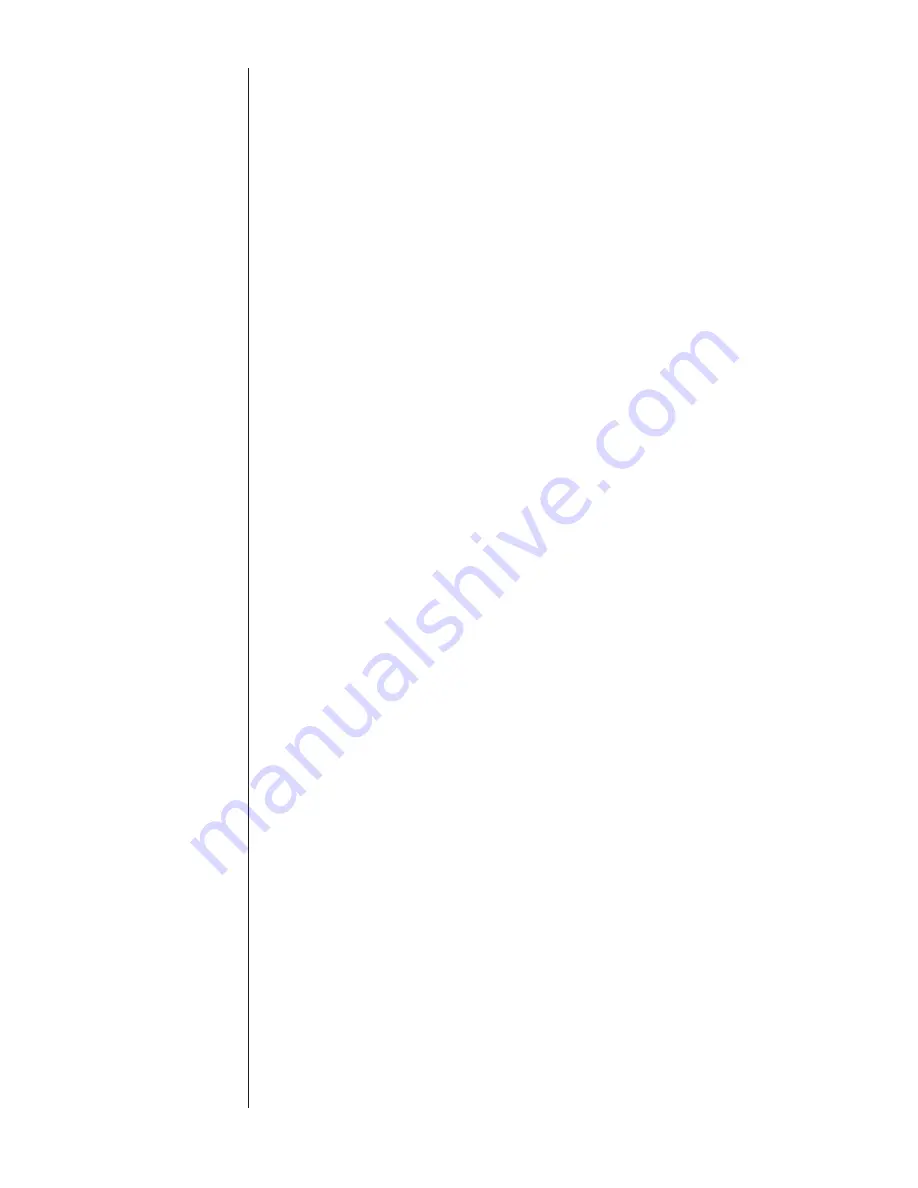
66
20.
Power on the voltage standard and allow it to warm up to its
specified accuracy as defined by the manufacturer.
21.
The HHC Base Unit will prompt the operator to apply pre-
cision voltage and current values to specific terminals,
data collection will take a few seconds then the HHC will
prompt the operator to move to the next step in the following
sequence :
a.
Apply 0.000 volts to the voltage input jacks press ENTER
b.
Apply 30.000 volts to the voltage input jacks press
ENTER
22.
POWER DOWN THE VOLTAGE STANDARD AND DISCON-
NECT THE VOLTAGE STANDARD FROM THE VOLTAGE
INPUT TERMINALS
23.
Connect the negative lead of the current source to the black
ringed “COM” input jack
24.
Connect the positive lead of the current source to the red
ringed “0-22mA In” jack
25.
Power on the DC current source capable of delivering up to
20.000mA and allow it to warm up to its specified accuracy
as defined by the manufacturer
26.
The HHC Base Unit will prompt the operator to apply preci-
sion current values to specific terminals, data collection will
take a few seconds then the HHC will prompt the operator to
move to the next step in the following sequence :
a.
Apply 0.000 mA to the current input jacks press ENTER
b.
Apply 20.000 mA to the current input jacks press ENTER
27.
This is the final data taking process of system field calibration.
It is now necessary to save the newly calculated coefficients.
28.
POWER DOWN THE CURRENT STANDARD AND DIS-
CONNECT FROM THE INPUT TERMINALS
NOTE: If you wish to abort this process and not change
the present calibration coefficients, press “ESC” and then
“MENU” to return to the main menu
29.
The HHC Base will prompt the operator to apply the
calibration data .
30.
Press “ENTER” and the calibration data will be saved to
system EEPROM. A message will appear on the screen as
the data is written to memory
31. Field Calibration is now compete.
32.
If desired repeat the “As Found” procedure to document “As
Left” data.
Pressure modules can be recalibrated and certified in the field.
The procedure allows for the acquisition of “as found” and “as left”
data, and recalibration of the pressure module.
Field calibration typically consists of three steps. Step one is
to document the “as found” or pre calibration condition of the
module. Step two is to perform the recalibration procedure to
adjust coefficients used by the module. Step 3 is to repeat step
one to document the “as left” or post recalibration condition of the
module.
The procedure details two processes, first obtaining “as found”
and ”as left” data; second performing the actual calibration of the
HHC.
Obtaining “As found” and “As Left” data consists of applying
precisely controlled pressure to the module and comparing the
value shown on the display to that being applied by the pressure
standard. The number of points measured typically increases with
the accuracy of the module. Factory calibration consists of the
following number of points based on module accuracy:
0.025% & 0.05% enhanced accuracy
20 points (approximately 10% increment)
SECTION 15 n.
CALIBRATE BASE UNIT CONT.
SECTION 15 o.
PRESSURE MODULE CALIBRATION
Summary of Contents for ATE-2
Page 1: ...i I M002 10233 ASHCROFT ATE 2 Operation and Maintenance Manual 0 0 5 4 P S I 0 8 6 i n H 2 0...
Page 2: ...ii...
Page 50: ...48 SECTION 15 l FIRMWARE UPDATE CONT...
Page 51: ...49 SECTION 15 l FIRMWARE UPDATE CONT...
Page 55: ...53 SECTION 15 l FIRMWARE UPDATE CONT Note The File Transfer can take up to 15 Minutes...