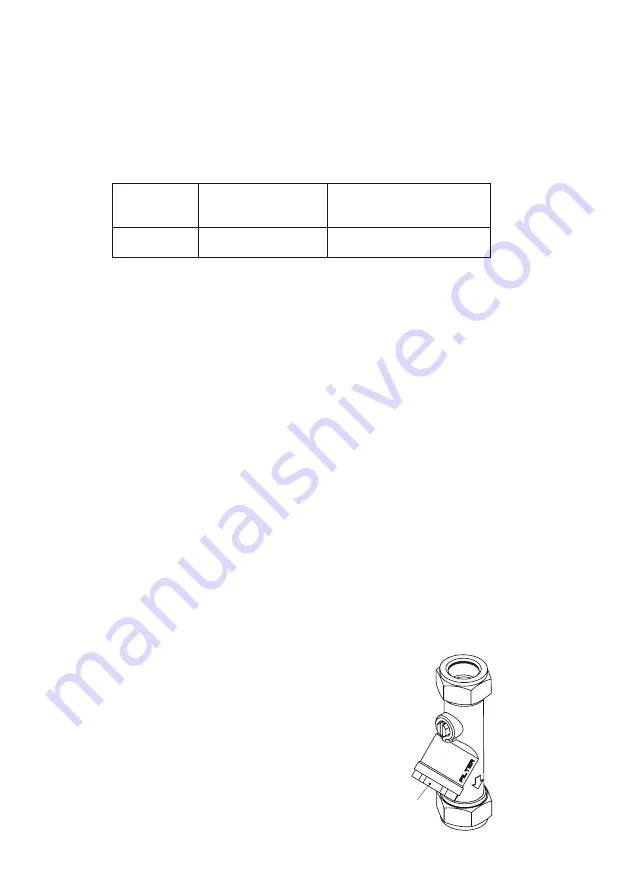
20
10 SERVICING - TVM3 SCHEME
10.1 Frequency of regular servicing
9.6
Setting temperature for sensor operated mixers
The need for servicing is normally identified as a result of the regular performance auditing.
Table 2 A guide to maximum temperature sets
Permitted maximum stabilised
temperature recorded during site
testing – excluding transient spikes
Maximum mixed water
temperature during
normal operation
Application
41ºC *
43ºC
Washbasin
The purpose of servicing regularly is to monitor any changes in performance due to changes in either
the system or the product. This may highlight the need to adjust either the supply system or the product.
These products should be audited 6 to 8 weeks and again 12 to 15 weeks after commissioning. The
results are to be compared against original commissioning settings.
If the product passes the audit test three consecutive times (demonstrating good stability of system &
product) then a 12 monthly servicing cycle may be adopted.
Otherwise, servicing checks should be carried out more frequently (E.g. every 4 months).
Follow the recommended auditing and maintenance procedures detailed in sections 9 & 12. During
servicing, note the following:
1. Repeat the procedure of recording and checking supply temperatures. (The same type of measuring
equipment should be used)
2. If the temperature has changed significantly from the previously recorded valves, the following should
be checked:
a. All in-line or integral valve strainers are clear of obstruction.
b. All in-line or integral check valves are clean and working properly to prevent backflow.
c. Any isolating valves are fully open.
d. The thermostat is free of debris
3. When satisfied with the mixed outlet temperatures re-record the temperatures.
11 MAINTENANCE OF IN-LINE COMPONENTS
In this example, (see figure 25) the isolator screw slot is
shown in the vertical position. This indicates the valve is open.
To close this valve, rotate the isolator screw by 90° into the hor-
izontal position. By operating the product, this will drain down
the water from the pipes below the service valve. Once the
product has been isolated, this will permit maintenance staff to:
1. Check & clean the strainers by unscrewing the strainer cap.
2. Replace the in-line solenoid valves if necessary.
3. Completely remove the product from the panel if necessary.
These products do not allow the user to select the desired blend temperature. We therefore recommend
setting a blend temperature of 39 to 40°C rather than the normally applicable 41°C maximum associated
with “user adjustable” products. This ensures comfort to more sensitive users.
* See section 9.6: setting temperature
strainer
cap
Figure 25 In-line isolating valve with strainer