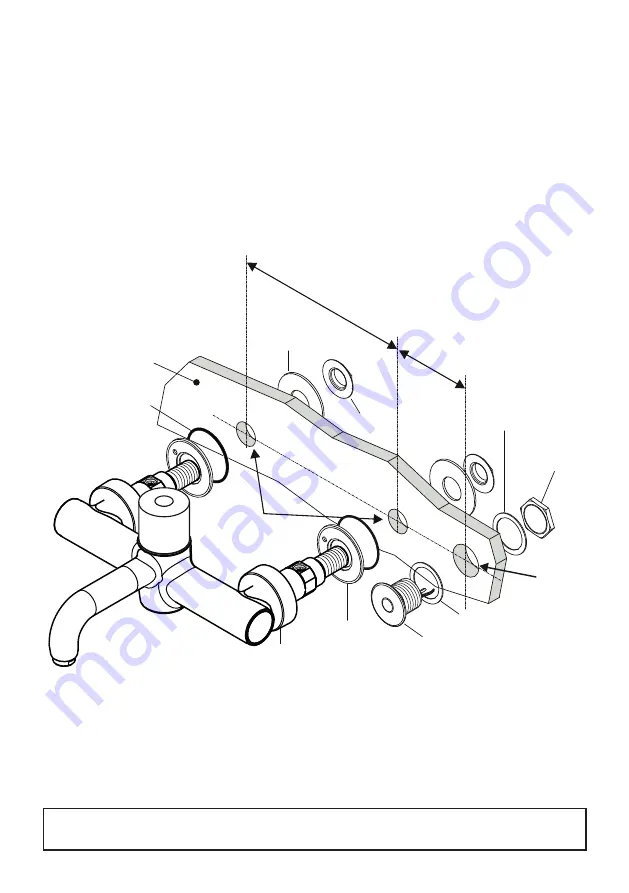
8
5
INSTALLATION: FIXATION
slip
washer
backnut
backnut
slip
washer
Figure 4
Timed Flow mixer installation - panel mounting
200 mm
85 mm
min
left or
right
Ø
30
nominal
Ø
35
nominal
wall
plate
shroud
seal
seal
timed flow
sensor
wall
panel
6
INSTALLATION: PLUMBING
These mixers are designed to be panel mounted on a duct wall of maximum panel thickness
27mm. For thicker panels the rear of the panel will require counter bores of 62mm or greater
around the fixation holes.
Cut two holes of 30mm diameter, horizontally aligned to 200mm centres in the wall.
(See figure 1 for height positioning of the fitting body over a “waste appliance”)
The sensor will require a hole of 35mm positioned as indicated in either fig4.
Loosen the chrome shrouds and insert the fitting as shown above with the wall plates and seals to the
front of the wall. Put on the slip washers and do up the backnuts to a torque of 25 Nm Screw the shrouds
onto the wall plates
Products covered in this manual are certified with the service valves provided.
Only if necessary (not recommended), use an equivalent service valve with integral strainer &
isolating function.
NOTE FOR IRELAND: 15mm olives are supplied with this product. Use ½” olives if ½” supply
pipes are fitted.