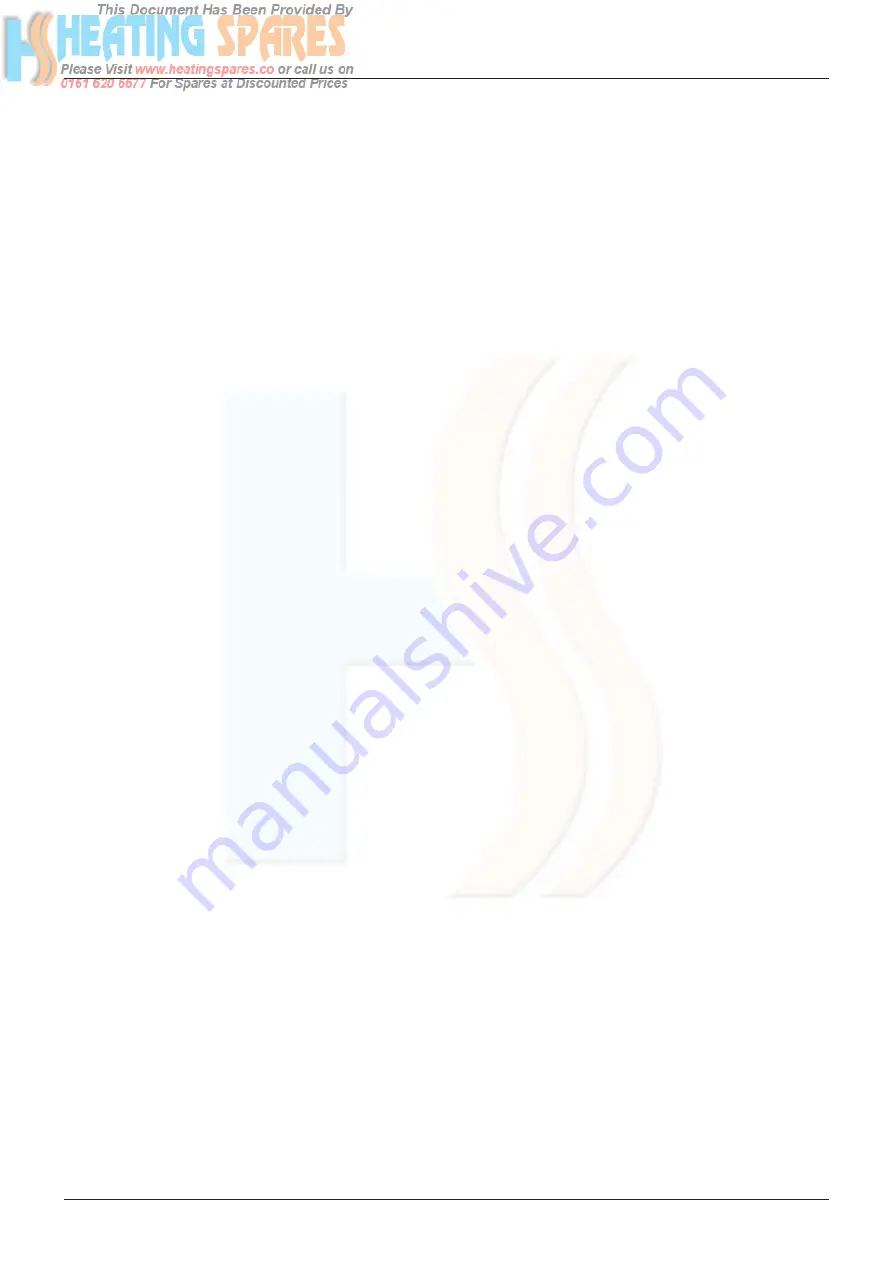
Supplied By www.heating spares.co Tel. 0161 620 6677
10
installation
Water Supply
The boiler is suitable for sealed systems only. The maximum
working pressure for the appliance is 6 bar. All fittings and
pipework for the appliance should be of the same standard. If
there is a possibility of the incoming mains pressure exceeding 6
bar, particularly at night, then a suitable pressure limiting valve
must be fitted.
The boiler is designed to provide hot water on demand to
multiple outlets within the property. If there is a requirement for
greater demands, for example if the boiler has several bathrooms
and cloakrooms, a vented or unvented hot water storage system
may be used.
Showers
Any shower valves used with the appliance should be of a
thermostatic or pressure balanced type. Refer to the shower
manufacturer for performance guidance and suitability.
Flushing and Water Treatment
The boiler is equipped with a stainless steel heat exchanger.
The detailed recommendations for water treatment are given in
BS 7593:199 (Treatment of water in domestic hot water central
heating systems); the following notes are givent for general
guidance;
If the boiler is installed on an existing system, any unsuitable
additives must be removed.
Under no circumstances should the boiler be fired before the
system has been thoroughly flushed; the flushing procedure
must be in line with BS 7593:199.
We highly recommend the use of a flushing detergent
appropriate for the metals used in the circuit. These include
cleansers produced by Fernox BetzDearbon, whose function is to
disolve any foreign matter that may be in the system;
In hard water areas or where large quantities of water are in the
system the treatment of water to prevent premature scaling of
the main exchanger is necessary.
The formation of scale strongly compromises the efficiency of
the thermic exchanger because small areas of scale cause a high
increase of the temperature of the metallic walls and therefore
add to the thermal stress of the heat exchanger.
Demineralised water is more aggressive so in this situation it
is necessary to treat the water with an appropriate corrosion
inhibitor.
Any treatment of water by additives in the system for frost
protection or for corrosion inhibition has to be absolutely
suitable for all metals used in the circuit.
The use of a corrosion inhibitor in the sysem such as Fernox
MB-1, BetzDearborn Sentinel X100 or Fernox System Inhibitor
is recommended to prevent corrosion (sludge) damaging the
boiler and system;
If anti-freeze substances are to be used in the system, check
carefully that they are compatible with the metals used in the
circuit.
MTS suggests the use of suitable anti-freeze products such as
Fernox ALPHI 11, which will prevent rust and incrustation taking
place.
Preiodically check the pH balance of the water/anti-freeze
mixture of the boiler circuit and replace it when the amount
measured is out of the range stipulated by the manufacturer (7
< pH < 8).
DO NOT MIX DIFFERENT TYPES OF ANTI-FREEZE
In under-floor systems, the use of plastic pipes without
protection against penetration of oxygen through the walls can
cause corrosion of the systems metal parts (metal piping, boiler
etc), through the formation of oxides and bacterial agents.
To prevent this problem it is necessary to use pipes with an
“oxygen proof barrier”, in accordance with standards DIN
476/479.
If pipes of this kind are not used, keep the system
separate by installing heat exchangers of those with a
specific system water treatment.
IMPORTANT
Failire to carry out the water treatment procedure will
invalidate the appliance guarantee.
System Controls
The boiler is electrically controlled and is suitable for most
modern electronic time and temperature controls. The addition
of such external controls can be beneficial to the efficient
operation of the system. The boiler connections for external
contols are 1V DC and so only controls of 1V DC that have
voltage free contacts should be used. (page 4).
MTS supply a range of wired and wireless system controls.
Contact your supplier for more details.
Location
The boiler can be installed on any suitable internal wall
(suitable sound proofing may be required when installing
onto a stud partition wall). Provision must be made to allow
for the correct routing of the flue and siting of the terminal
to allow the safe and efficient removal of the flue products. A
compartment or cupbaord may be used provided that it has
been built or modified for this purpose. It is not necessary to
provide permanent ventillation for cooling purposes. Detailed
recommendations are given in BS 5440 Part . If it is proposed
that it is to be installed in a timber framed building then
reference should be made to British Gas Document DM, IGE/
UP/7 or advice sought from CORGI.
Where a room sealed appliance is installed in a room
containing a bath or shower, the appliance and any electrical
switch or appliance control, utilising mains electricity should
be situated specifically in accordance with current IEE Wiring
Regulations.
For unusual locations, special procedures may be necessary.
BS
6798:2000
gives detailed guidance on this aspect.
Codensate Discharge
The condensate discharge hose from the boiler must have a
continuous fall of .5
o
and must be inserted by at least 50mm
into a suitable acid resistant pipe - e.g. plastic waste or overflow
pipe. The condensate discharge pipe must have a minimum
diameter of mm, must have a continuous fall and preferably
be installed and terminated to prevent freezing.
The discharge pipe must be terminated in a suitable position:
i) Connecting into an internal soil stack (at least 450mm above
the invert of the stack). A trap giving a water seal of at least
75mm must be incorporated into the pipe run, there also
must be an air beak upstream of the trap.