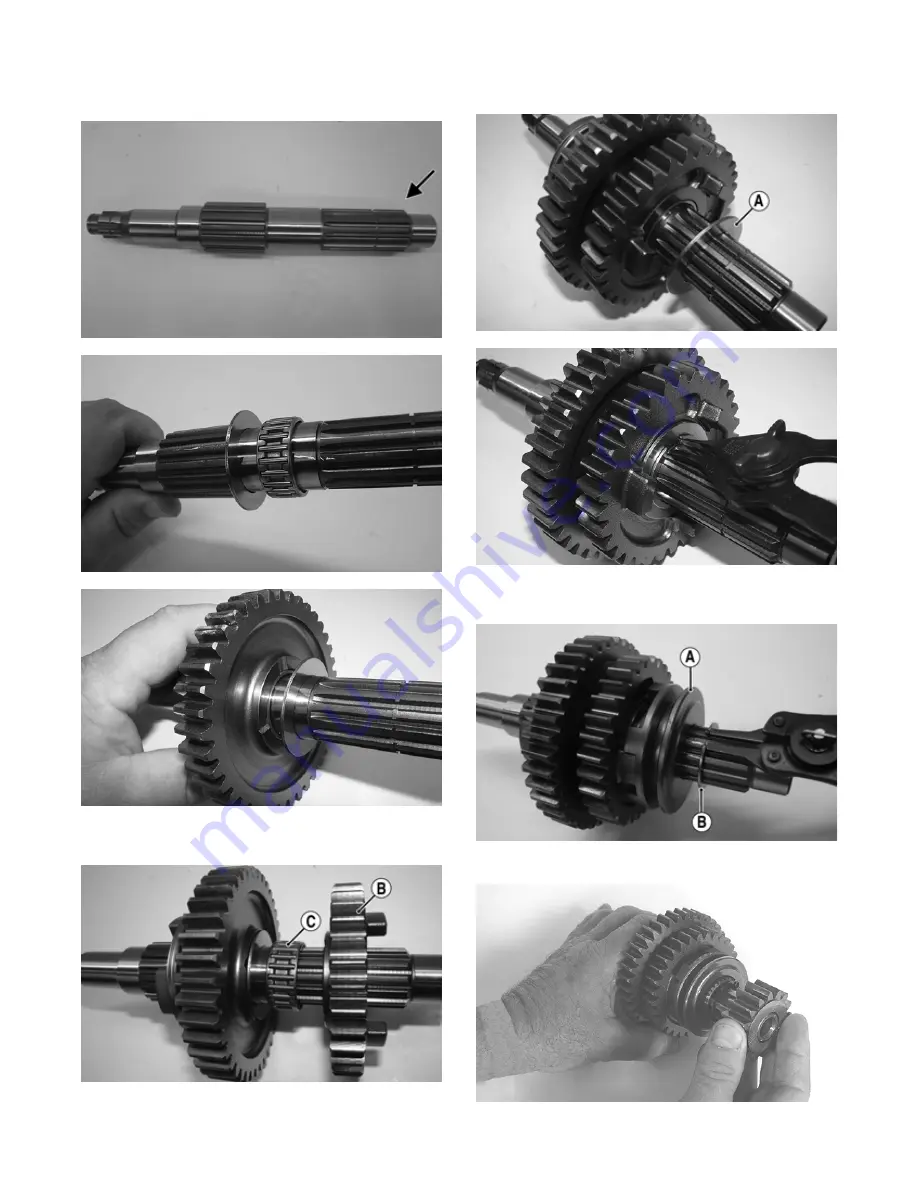
76
Assembling
1. From the drive gear end, install a thrust washer, and
bearing; then install the low driven gear and washer.
H1-049A
H1-048
H1-047
2. Install the reverse driven gear needle bearing (C)
then the reverse driven gear (B).
H1-046A
3. Install the outer reverse driven gear washer (A); then
secure the reverse driven gear assembly with a new
snap ring.
H1-045A
H1-044
4. Install the reverse driven dog (A) onto the counter-
shaft and secure with a new snap ring (B).
H1-043A
5. Install the drive gear.
GZ296
Summary of Contents for VLX 70002017
Page 1: ...2017 S SERVICE ERVICE MANUAL ANUAL www arcticcat com...
Page 137: ...136 NOTES...