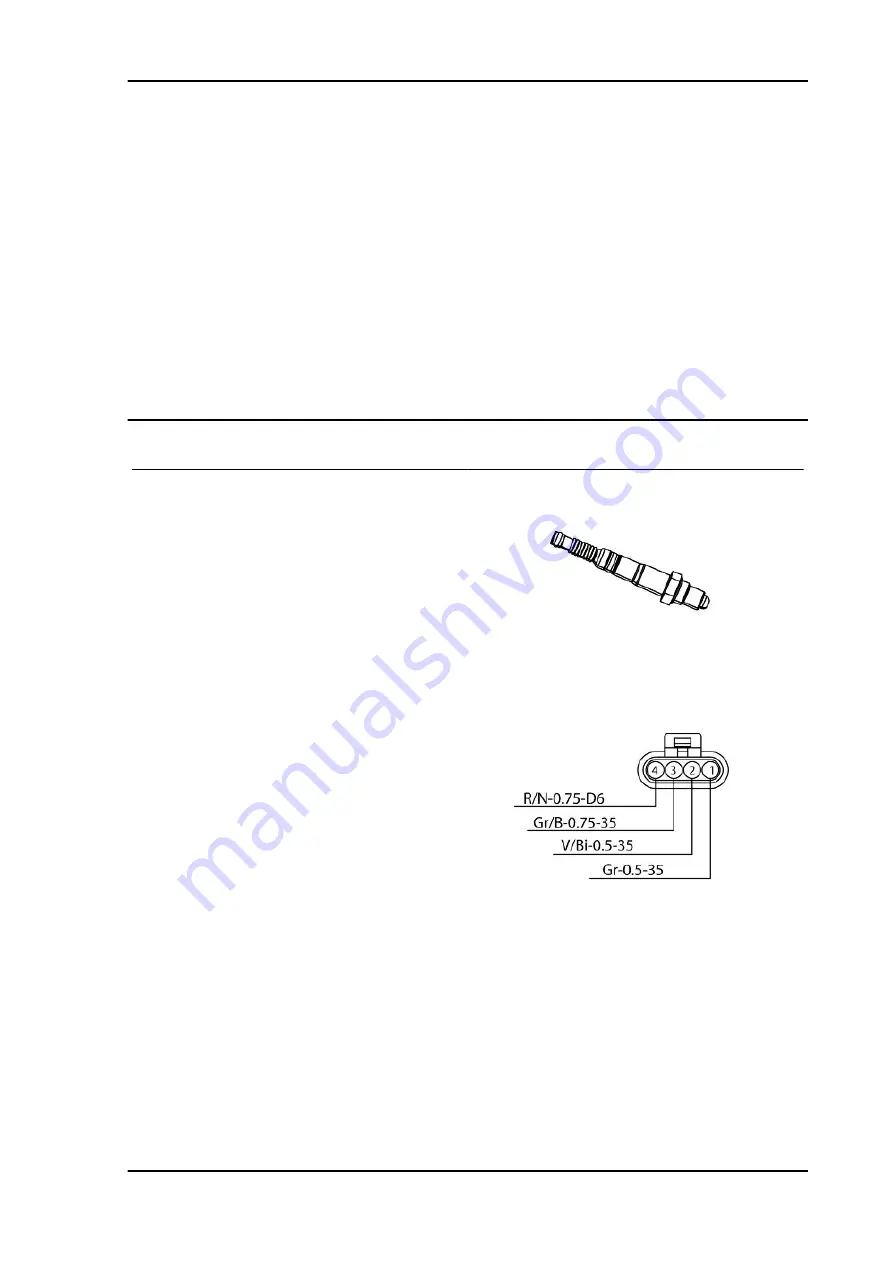
If there is, it means that the control unit does not supply the ground connection and therefore
should be replaced.
•
If shorted to negative, check sensor correct resistance: if resistance = 0, replace the sensor;
if resistance is correct, it means that the cable has ground connection: restore the cable
harness.
NOTES
No error is detected if the sensor does not work correctly or the control unit connector
or sensor terminals are rusty: then check through Axone if the temperature indicated is plausible
in relation to the ambient temperature. Check also that the sensor electrical characteristics are
observed: replace the sensor if not OK; if it is OK, check the sensor connector and the Marelli
control unit connector.
Lambda sensor
LAMBDA PROBE
Function
It tells the control unit whether combustion is lean
or rich.
Operation / Operating principle
The Marelli injection control unit reads and inter-
prets a voltage generated by the difference in oxy-
gen content between the exhaust fumes and the
ambient. It does not require an external supply
source but, in order to work properly, it should
reach a high operating temperature: that is why
there is a heating circuit inside.
Level in wiring diagram:
Lambda Probe
Location:
•
on the vehicle: exhaust pipe
•
connector: near the probes
Electrical characteristics:
•
Oxygen probe with preheating circuit
(power 7W)
•
It generates voltage within: 0 - 1000
mV
•
Heater circuit: continuity (7 - 9 Ohm at
ambient temperature)
Pin-out:
DORSODURO
Electrical system
ELE SYS - 101
Summary of Contents for DORSODURO 2007
Page 1: ...SERVICE STATION MANUAL 854202 DORSODURO ...
Page 5: ......
Page 6: ...INDEX OF TOPICS CHARACTERISTICS CHAR ...
Page 25: ...DORSODURO Characteristics CHAR 25 ...
Page 26: ...INDEX OF TOPICS SPECIAL TOOLS S TOOLS ...
Page 34: ...INDEX OF TOPICS MAINTENANCE MAIN ...
Page 46: ...INDEX OF TOPICS TROUBLESHOOTING TROUBL ...
Page 54: ...INDEX OF TOPICS ELECTRICAL SYSTEM ELE SYS ...
Page 134: ...INDEX OF TOPICS ENGINE FROM VEHICLE ENG VE ...
Page 142: ...See also Vehicle preparation Adjusting Engine from vehicle DORSODURO ENG VE 142 ...
Page 143: ...INDEX OF TOPICS ENGINE ENG ...
Page 216: ...INDEX OF TOPICS POWER SUPPLY P SUPP ...
Page 223: ...INDEX OF TOPICS SUSPENSIONS SUSP ...
Page 250: ...INDEX OF TOPICS CHASSIS CHAS ...
Page 260: ... Unscrew and remove the lambda probe Chassis DORSODURO CHAS 260 ...
Page 261: ...INDEX OF TOPICS BRAKING SYSTEM BRAK SYS ...
Page 268: ...INDEX OF TOPICS CLUTCH SYSTEM CLU SYS ...
Page 270: ...INDEX OF TOPICS COOLING SYSTEM COOL SYS ...
Page 278: ...INDEX OF TOPICS BODYWORK BODYW ...
Page 292: ...INDEX OF TOPICS ...
Page 293: ...PRE DELIVERY PRE DE ...
Page 302: ...T Tank 276 287 Transmission 12 Tyres 14 W Warning lights ...