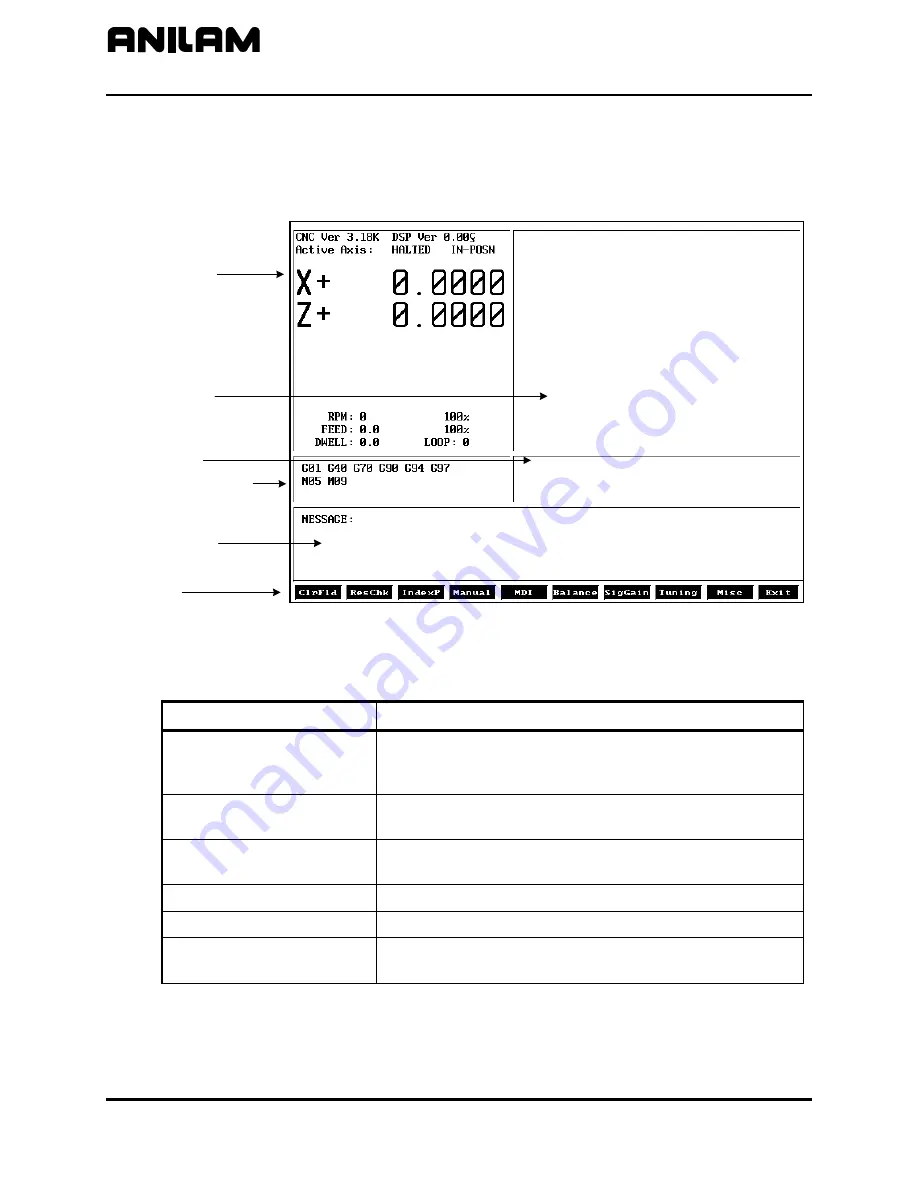
CNC Motion Setup/Testing Utility
P/N 70000634C
Activating the MST Screen
The axis positions displayed in
Figure 1
correspond to the current
position. The Graphic Area displays step responses for the Signal Gain
and Tuning functions. Refer to
Figure 1
and
Table 1
.
General Status
Graphics Area
Active Status Codes
Prompt Area
Message Area
Soft Keys
4MSTSCRN
Figure 1, CNC Motion Setup/Testing Screen
Table 1, MST Screen Areas
MST Screen Area
Description
General Status
Shows Active Modes, Machine Position for each axis,
RPM, Dwell, Spindle Speed and Feedrate, Active Axis,
and other information regarding the status of the CNC.
Graphic Area
Displays step responses for the Signal Gain and Tuning
functions.
Prompt Area
Displays messages regarding information that must be
entered.
Active Status Codes
Active G-codes.
Message Area
Displays error messages.
Soft Keys
Function keys (
F1
–
F10
) located below the LCD on the
console used to activate the functions, as labeled.
All rights reserved. Subject to change without notice.
November 2009
2
Summary of Contents for 4200T
Page 1: ...www anilam com 4200T CNC Motion Setup Testing Utility...
Page 2: ......
Page 4: ......
Page 46: ......
Page 47: ......