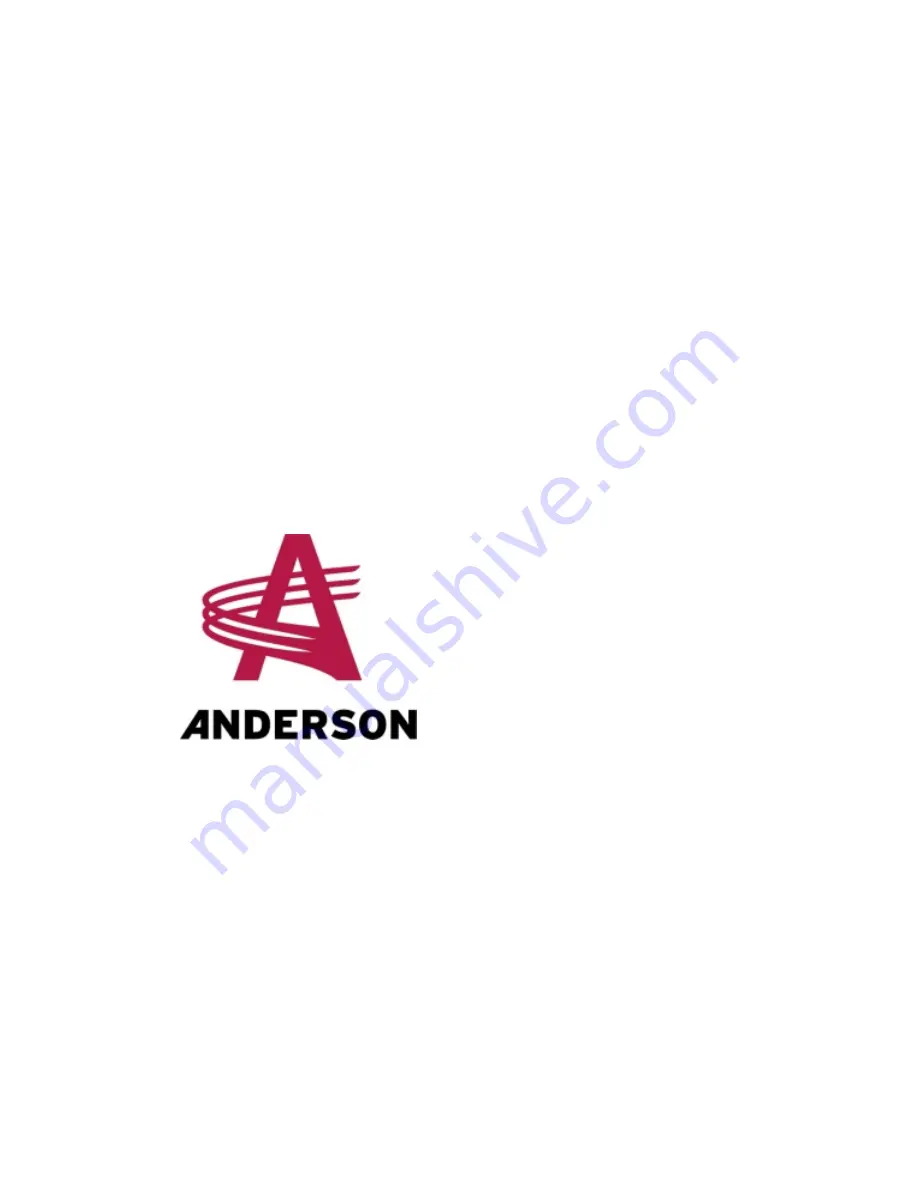
ANDERSON GROUP
5125 De la Plaisance
Chesterville, QC
CANADA G0P 1J0
Email: [email protected]
Phone: 1-819-382-2952
Fax: 1-819-382-2218
www.grpanderson.com
Summary of Contents for SMARTMIX A1230FD
Page 1: ...Mixer SMARTMIX 404623 Operator s Manual ORIGINAL NOTICE 2019 ...
Page 2: ......
Page 8: ......
Page 10: ......
Page 14: ......
Page 17: ...Anderson Group Mixer Operator s Manual 15 Figure 3 SMARTMIX Auger ...
Page 22: ...20 Operator s Manual Mixer Anderson Group 1 2 2 SMARTMIX FD Figure 5 Dimensions SMARTMIX FD ...
Page 48: ......
Page 86: ......
Page 128: ......