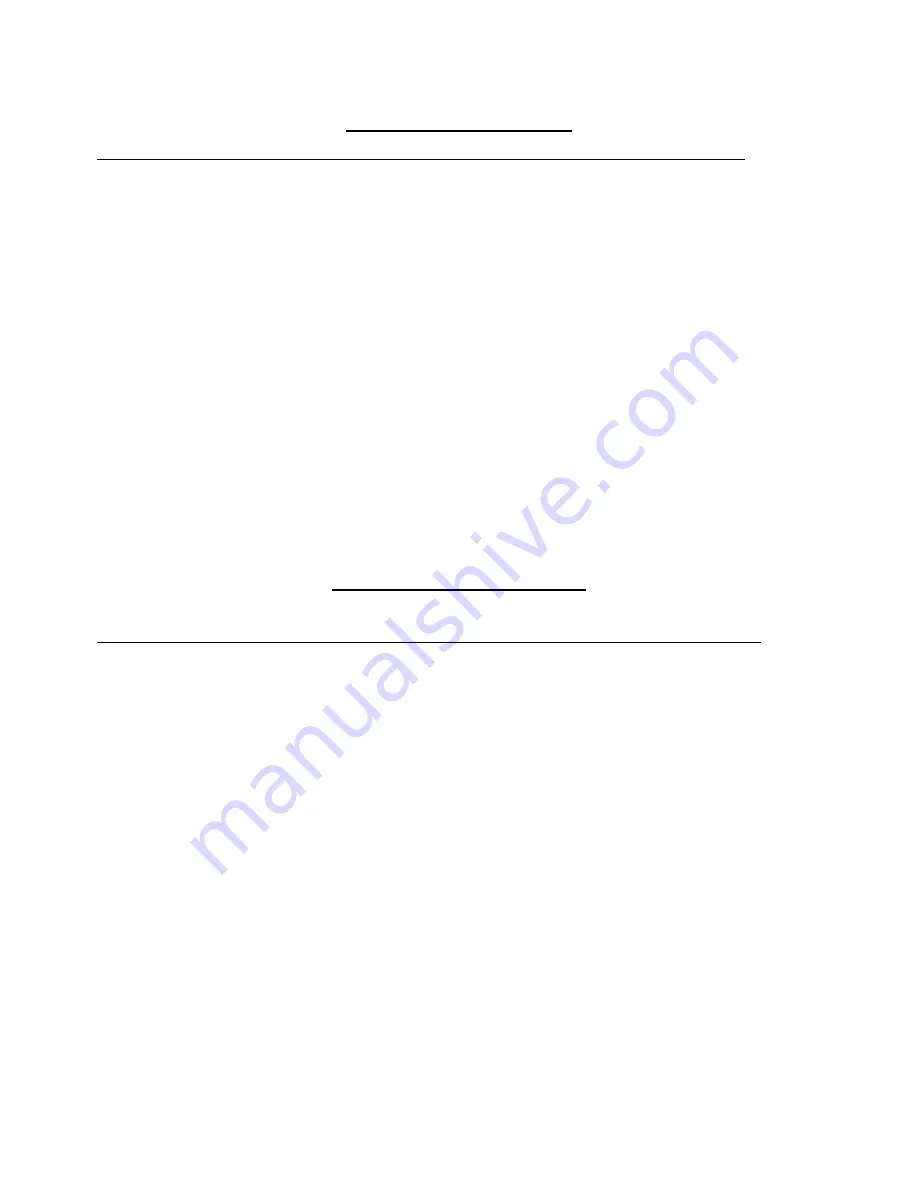
Model 415
Operation Manual
Document No. 740084
Revision N
iv
TABLE OF CONTENTS
SECTION DESCRIPTION PAGE
SECTION V
OPERATION
5.0
Introduction
30
5.1
Initial Power-On
30
5.2
Power Supply Calibration Introduction
30
5.3
Required Equipment For Calibration
31
5.4
Main Reference Voltage Calibration
31
5.5
Position Feedback Voltage Calibration
32
5.6
Current Calibration
32
5.7
Arc Voltage Calibration
35
5.8
Weld Head Travel Calibration Introduction
36
5.9
Weld Head Travel Calibration
37
5.10
Weld Head Wire Feed Calibration
38
5.11
System Security
39
5.12
Project Data Recording
40
5.13
General Maintenance
40
5.14
System Fault Corrections
41
5.15
Re-Shipping
42
5.16
Selecting and Creating Languages
43
5.17
Creating and Editing Weld Head Templates
45
5.18
CMOS Battery Replacement
47
LIST OF ILLUSTRATIONS
NUMBER
DESCRIPTION PAGE
Figure 1
System Configuration
14
Figure 2
AC Power Set Up (Transformer jumpers - International)
15
Figure 2A
AC Power Set Up (Transformer jumpers - Domestic)
18
Figure 3
Cable Connections
19
Figure 4
Status Screen/Initial Turn-On
20
Figure 5
Sequence Timing Chart
29
Figure 6
CMOS battery location on EP811 motherboard
47
Figure 7
CMOS battery location on SBC84710 motherboard
48
Summary of Contents for 415
Page 1: ...MODEL 415 OPERATION MANUAL Document No 740084 Revision N ...
Page 19: ...Model 415 Operation Manual Document No 740084 Revision N 14 ...
Page 24: ...Model 415 Operation Manual Document No 740084 Revision N 19 ...
Page 25: ...Model 415 Operation Manual Document No 740084 Revision N 20 ...
Page 34: ...Model 415 Operation Manual Document No 740084 Revision N 29 ...