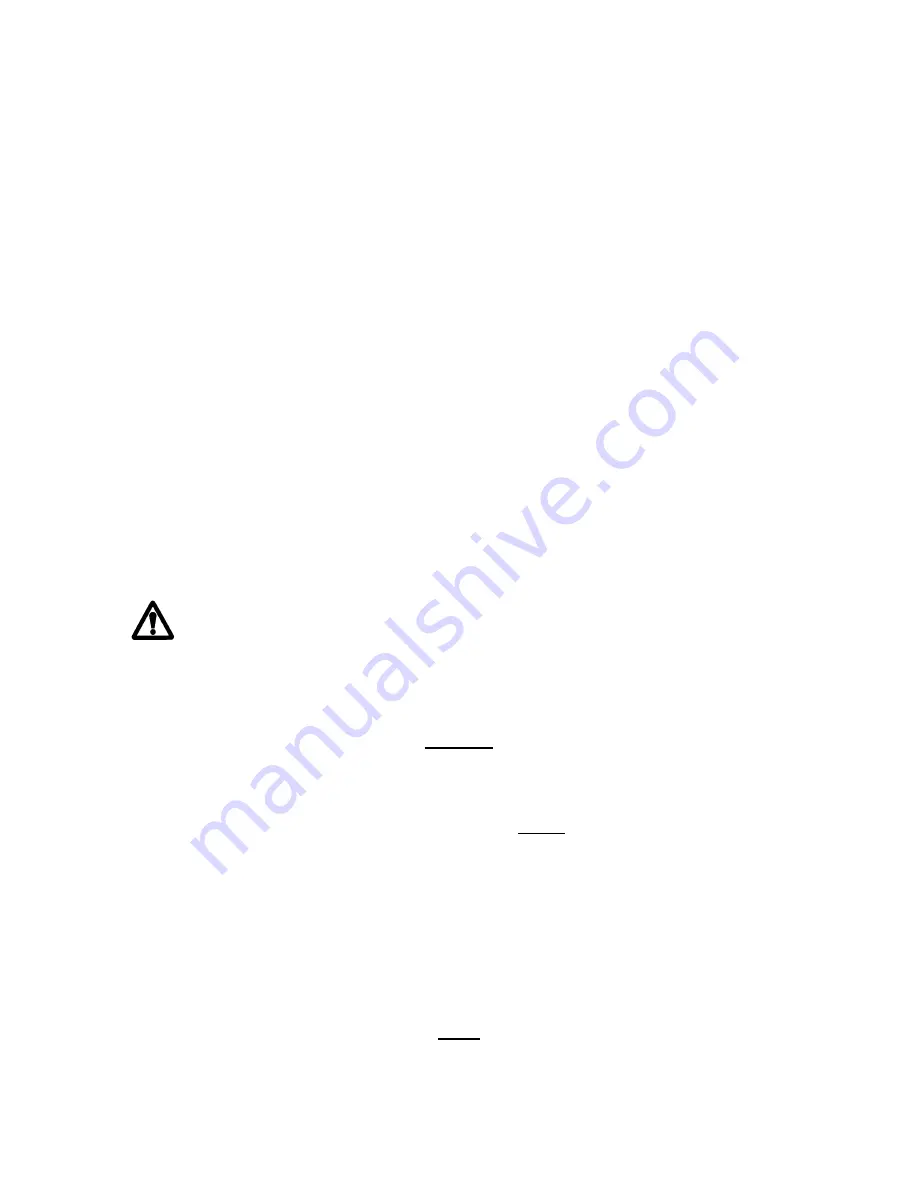
Model 415
Operation Manual
4.
Operator Pendant (see Figure 1, Item 5)
1.
For the remainder of this manual this will be called the RP Pendant or just Pendant.
2.
Perform a visual inspection to insure no obvious shipping damage has occurred.
Check Pendant cable for Protective Connector Covers, tight strain relief and no
frays or tears in the Cable Jacket.
5.
Cables
There are five Standard Cables included with the Model 415. Check each of the following
Cables for Protective Covers, proper strain relief and obvious frays or tears.
1.
RP Pendant Extension Cable, 50 foot (15.2 meters) (see Figure 1 Item 6).
2.
Weld Head Adapter Control Cable, 40 foot (12.2 meters) (see Figure 1 Item 7).
3.
Weld Head Adapter Service Cable, 40 foot (12.2 meters) (see Figure 1 Item 8).
4.
Ground cable with “C” Clamp, 50 foot (15.2 meters) (see Figure 1, Item 9).
5.
Input Power Cable, 25 foot (7.6 meters) (see Figure 1, Item 10).
6.
Weld Head (see figure 1, Item 11)
1.
Inspect the Weld Head or Heads for obvious physical damage. The Model 415 can
operate all AMI Weld Heads. The user will find detailed Weld Head Installation and
Inspection information in the Operation Manual for each specific Weld Head.
3.3
TORCH COOLANT SYSTEM PREPARATION
The Model 415 power source is air cooled. However, almost all AMI Torches require liquid
cooling. The Coolant System provides coolant for Weld Heads equipped with liquid cooled
Torches. The liquid coolant should be a combination of pure de-mineralized, de-ionized or distilled
water and pure Ethylene glycol.
If antifreeze is required Arc Machines, Inc. recommends the use of a corrosion inhibitor and
algaeside along with water or water mixture. The present recommended water treatment is
Optishield Plus manufactured by Opti-Temp Corp. and can be purchased from local welding
supply. Glycol mixtures can be purchased from Miller Electric for RF TIG applications,
available from local welding supply
.
CAUTION
It is extremely important to insure proper operation of the Coolant System. The coolant system
will operate, for a few weeks or months, with plain tap water as the coolant. After some length of
operating in this condition the Coolant System will begin to have problems with bacteria growth,
contaminates, poor connections, hoses and pump flow. For the Coolant System to continue to
meet the demands of the System Specification it must “BEGIN” operations per this procedure.
The following is for initial preparation of the Coolant System after shipment from the FACTORY.
1.
The Coolant System reservoir has a capacity of 2.5 gallons (9.46 liters). This reservoir is
located on the lower left side of the Power Supply. The left side panel should already be
removed (step 3.2.2.2), if not remove the left side panel to access the coolant system.
2.
Remove the coolant fill spout cap (Figure 1, Item 12) and add 2.5 gallons of coolant solution
or distilled water.
NEVER USE TAP WATER IN THE COOLANT SYSTEM.
Before Operating be sure to re-install the left side panel (Figure 1, Item 13).
.
NOTE
For operation and storage in areas subject to freezing temperatures, use 1.75 gallons of
distilled water mixed with 0.75 gallons of pure Ethylene Glycol for a total of 2.5 gallons of
coolant.
Document No. 740084
Revision N
12
Summary of Contents for 415
Page 1: ...MODEL 415 OPERATION MANUAL Document No 740084 Revision N ...
Page 19: ...Model 415 Operation Manual Document No 740084 Revision N 14 ...
Page 24: ...Model 415 Operation Manual Document No 740084 Revision N 19 ...
Page 25: ...Model 415 Operation Manual Document No 740084 Revision N 20 ...
Page 34: ...Model 415 Operation Manual Document No 740084 Revision N 29 ...