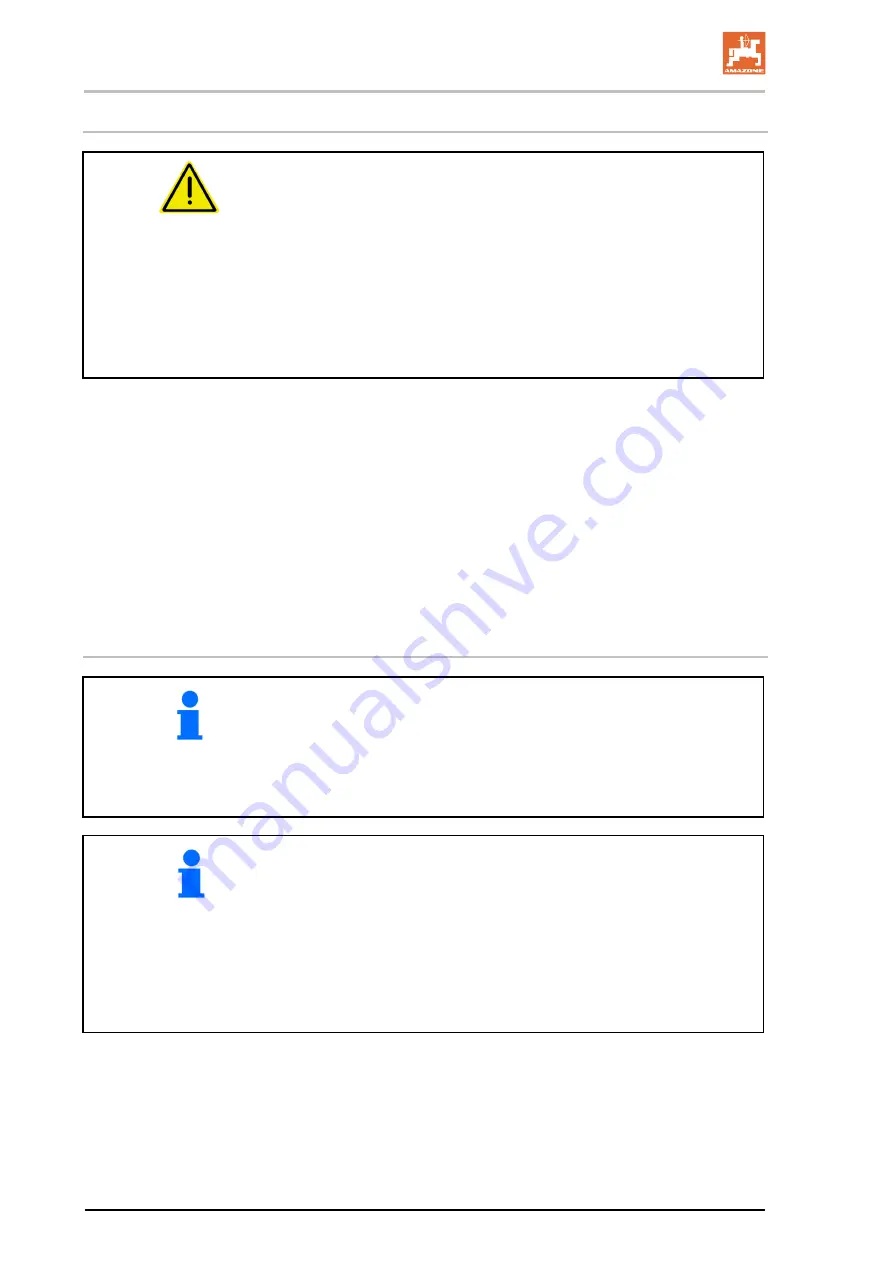
Commissioning
48
EK-S/EK-SH BAG0022.4 07.22
6.1
Checking the suitability of the tractor
WARNING
Danger of breaking during operation, insufficient stability and
insufficient tractor steering and braking power on improper use
of the tractor!
•
Check the suitability of your tractor, before connecting the ma-
chine to the tractor.
You may only connect the machine to tractors suitable for the
purpose.
•
Carry out a brake test to check whether the tractor achieves the
required braking delay with the machine connected.
Requirements for the suitability of a tractor are, in particular:
•
The approved total weight
•
The approved axle loads
•
The load capacity of the installed tyres
You can find this data on the rating plate or in the vehicle docu-
mentation and in the tractor operating manual.
The front axle of the tractor must always be subjected to at least 20%
of the dead-weight of the tractor.
The tractor must achieve the brake delay specified by the tractor
manufacturer, even with the machine connected.
6.1.1
Calculating the actual values for the total tractor weight, tractor axle loads
and load capacities, as well as the minimum ballast
The approved total tractor weight, specified in the vehicle documenta-
tion, must be greater than the sum of the
•
Empty tractor weight,
•
ballast weight and
•
total weight of the connected machine or drawbar load of the
connected machine
This information is only valid for the Federal Republic of Germa-
ny:
If, having tried all possible alternatives, it is not possible to comply
with the axle loads and / or the approved total weight, then a survey
by an officially-recognised motor traffic expert can, with the approval
of the tractor manufacturer, be used as a basis for the responsible
authority to issue an exceptional approval according to § 70 of the
German Regulations Authorising the Use of Vehicles for Road Traffic
and the required approval according to § 29, paragraph 3 of the Ger-
man Road Traffic Regulations.
Summary of Contents for EK-S 150
Page 76: ......