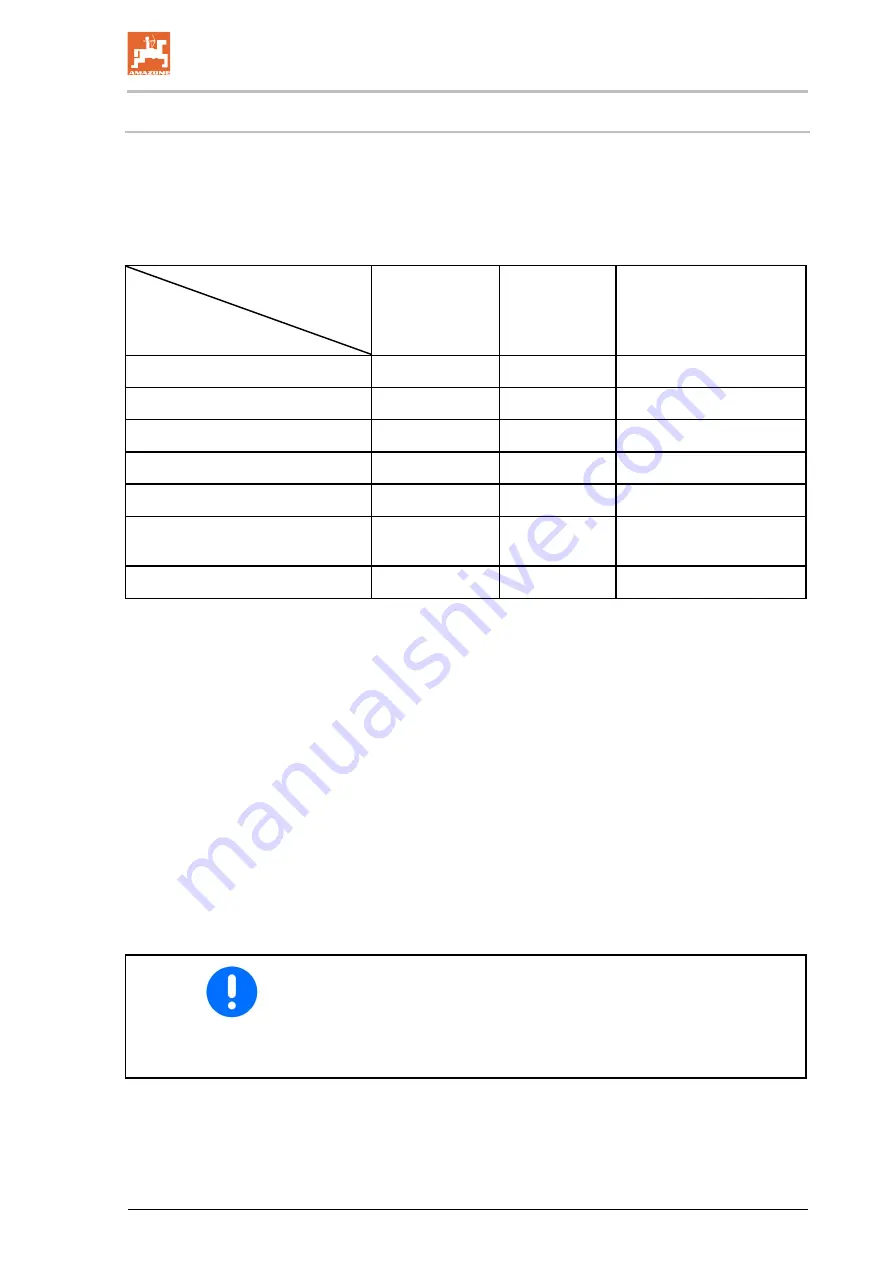
General Safety Instructions
KE/KX/KG (RIGID) BAH0089-7 02.2020
15
2.6
User training
Only those people who have been trained and instructed may work
with/on the implement. The operator must clearly specify the respon-
sibilities of the people charged with operation and maintenance work.
People being trained may only work with/on the implement under the
supervision of an experienced person.
Person
Activity
Person specially
trained for the
activity
1)
Trained
operator
2)
Persons with specialist
training
(specialist workshop)
3)
Loading/Transport
X
X
X
Initial operation
--
X
--
Set-up, tool installation
--
--
X
operation
--
X
--
Maintenance
--
--
X
Troubleshooting and fault elimina-
tion
--
X
X
Disposal
X
--
--
Legend:
X..permitted
--
..not permitted
1)
A person who can assume a specific task and who can carry out
this task for an appropriately qualified company.
2)
Instructed persons are those who have been instructed in their
assigned tasks and in the possible risks in the case of improper
behaviour, have been trained if necessary, and have been in-
formed about the necessary protective equipment and
measures.
3)
Persons with specialised technical training shall be considered
as a specialist. Due to their specialist training and their
knowledge of the appropriate regulations, they can evaluate the
work with which they have been charged and detect possible
dangers.
Comment:
A qualification equivalent to specialist training can be obtained
from several years' experience in the relevant field.
If maintenance and repair work on the implement is additionally
marked "Workshop work", only a specialist workshop may carry out
such work. The personnel of a specialist workshop shall possess the
appropriate knowledge and suitable aids (tools, lifting and support
equipment) for carrying out the maintenance and repair work on the
implement in a way which is both appropriate and safe.
Summary of Contents for KE 2501 Special
Page 71: ...Structure and function KE KX KG RIGID BAH0089 7 02 2020 71 Fig 43...
Page 171: ...Cleaning maintenance and repair KE KX KG RIGID BAH0089 7 02 2020 171...
Page 172: ...Notes 172 KE KX KG RIGID BAH0089 7 02 2020 13 Notes Space for your notes...