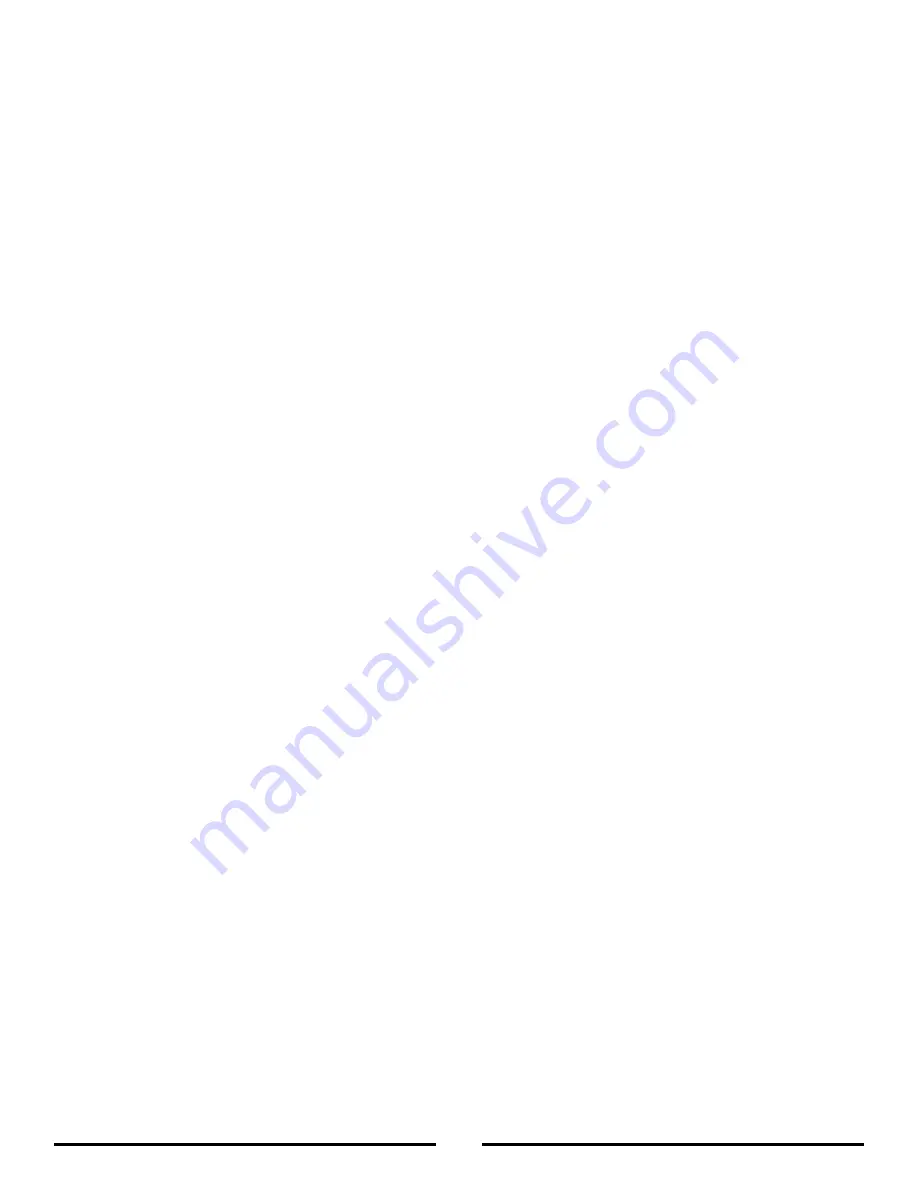
59
Emission Control Warranty Statement
Your Warranty Rights and Obligations
The California Air Resources Board and Amano Pioneer Eclipse
Corporation is pleased to explain the emissions control system’s
warranty on your 2016 small off-road engine. In California, new
equipment that use small off-road engines must be designed, built, and
equipped to meet the State’s stringent anti-smog standards. Amano
Pioneer Eclipse Corporation must warrant the emissions control system
on your small off-road engine for the period listed below provided there
has been no abuse, neglect or improper maintenance of your equipment.
Your emissions control system may include parts such as: carburetor’s
or fuel injection system, ignition system, catalytic converters, fuel tanks,
valves, filters, clamps, connectors, and other associated components.
Also, included may be hoses, belts, connectors, sensors, and other
emission-related assemblies. Where a warrantable condition exists,
Amano Pioneer Eclipse Corporation will repair your small off-road engine
at no cost to you including diagnosis, parts and labor.
Manufacturer’s Warranty Coverage
This emissions control system is warranted for two years. If any
emissions-related part on your equipment is defective, the part will be
repaired or replaced by Amano Pioneer Eclipse Corporation.
Owner’s Warranty Responsibilities
(a) As the small off-road engine owner, you are responsible for
performance of the required maintenance listed in your owner’s
manual. Amano Pioneer Eclipse Corporation recommends that you
retain all receipts covering maintenance on your small off-road engine,
but Amano Pioneer Eclipse Corporation cannot deny warranty solely
for the lack of receipts or your failure to ensure the performance of all
scheduled maintenance.
(b) As the small off-road engine owner, you should however be aware that
Amano Pioneer Eclipse Corporation may deny you warranty coverage
if your small off-road engine or a part has failed due to abuse, neglect,
or improper maintenance or unapproved modifications.
(c) You are responsible for presenting your small off-road engine to an
Amano Pioneer Eclipse Corporation distribution center or service
center as soon as the problem exists. The warranty repairs should be
completed in a reasonable amount of time, not to exceed 30 days. If
you have a question regarding your warranty coverage, you should
contact Amano Pioneer Eclipse Corporation at 1-800-367-3550.
Defects Warranty Requirements
(A) The warranty period begins on the date the engine or equipment is
delivered to an ultimate purchaser.
(B)
General Emissions Warranty Coverage.
Amano Pioneer Eclipse
Corporation as the manufacturer of each small off-road engine
or equipment must warrant to the ultimate purchaser and each
subsequent owner that the engine or equipment is:
(1) Designed, built, and equipped so as to conform with all
applicable regulations adopted by the Air Resources Board; and
(2) Free from defects in materials and workmanship that causes the
failure of a warranted part for a period of two years.
(C) The warranty on emissions-related parts will be interpreted as follows:
(1) Any warranted part that is not scheduled for replacement as
required maintenance in the written instructions required by
subsection (D) must be warranted for the warranty period defined
in Subsection (B2). If any such part fails during the period
of warranty coverage, it must be repaired or replaced by the
manufacturer according to Subsection (C4) below. Any such part
repaired or replaced under the warranty must be warranted for
the remaining warranty period.
(2) Any warranted part that is scheduled only for regular inspection
in the written instructions required by subsection (D) must be
warranted for the warranty period defined in Subsection (B2).
A statement in such written instructions to the effect of “repair
or replace as necessary” will not reduce the period of warranty
coverage. Any such part repaired or replaced under warranty
must be warranted for the remaining warranty period.
(3) Any warranted part that is scheduled for replacement as
replacement as required maintenance in the written instructions
required by subsection (D) must be warranted for the period
of time prior to the first scheduled replacement point for that
part. If the part fails prior to the first scheduled replacement, the
part must be repaired or replaced by the engine manufacturer
according to Subsection (C4) below. Any such part repaired or
replaced under warranty must be warranted for the remainder of
the period prior to the first scheduled replacement point for the
part.
(4) Repair or replacement of any warranted part under the warranty
must be performed at no charge to the owner at a warranty
station.
(5) Notwithstanding the provisions of Subsection (C4) above,
warranty services or Repairs must be provided at all
manufacturer distribution centers that are franchised to service
the subject engines.
(6) The owner must not be charged for diagnostic labor that leads
to the Determination that a warranted part is in fact defective,
provided that such diagnostic work is performed at a warranty
station.
(7) The manufacturer is liable for damages to other engine
components Proximately caused by a failure under warranty of
any warranted part.
(8) Throughout the emissions warranty period defined in Subsection
(B2), the manufacturer must maintain a supply of warranted parts
sufficient to meet the expected demand for such parts.
(9) Any replacement part may be used in the performance of any
warranty Maintenance or repairs and must be provided without
charge to the owner. Such use will not reduce the warranty
obligations of the manufacturer.
(10) Add-on or modified parts that are not exempted by the
Air Resources Board may not be used. The use of any
non-exempted add-on or modified parts will be grounds for
disallowing a warranty claim. The manufacturer will not be liable
to warrant failures of warranted parts caused by the use of a
non-exempted add-on or modified part.
(11) The manufacturer issuing the warranty shall provide any
documents that describe that manufacturer’s warrant procedures
or policies within five working days of request by the Air
Resources Board.
(D)
Emission Warranty Parts List
(1) Fuel Metering System
(a) Carburetor, internal parts, and pressure regulator.
(b) Cold start enrichment system.
(2) Air Induction System
(a) Intake manifold.
(b) Air filter.
(3) Ignition System
(a) Spark Plugs.
(b) Magneto or electronic ignition system.
(c) Spark advance/retard system.
(4) Exhaust System
(a) Exhaust manifold.
(5) Miscellaneous Items Used in Above Systems
(a) Electronic Fuel Cut-off control.
(b) Vacuum, temperature, time sensitive valves, and switches.
(c) Hoses, belts, connectors, and assemblies.
Amano Pioneer Eclipse Corporation will furnish with each new engine
written instructions for the maintenance and use of the engine by the
owner.
Exception
: This warranty does not apply to any machine models that do
not have a catalyst muffler.
Small Off-Road Engine Certification Warranty Form
Summary of Contents for Pioneer Eclipse PE420GP Series
Page 1: ...Propane Hard Floor Machine PE420GP Operator s Manual...
Page 2: ......
Page 35: ...35 Electrical Schematic...
Page 36: ...36 Connections...
Page 38: ...38 Connections HD...
Page 39: ...39 Connections HD continued...
Page 62: ......
Page 63: ......