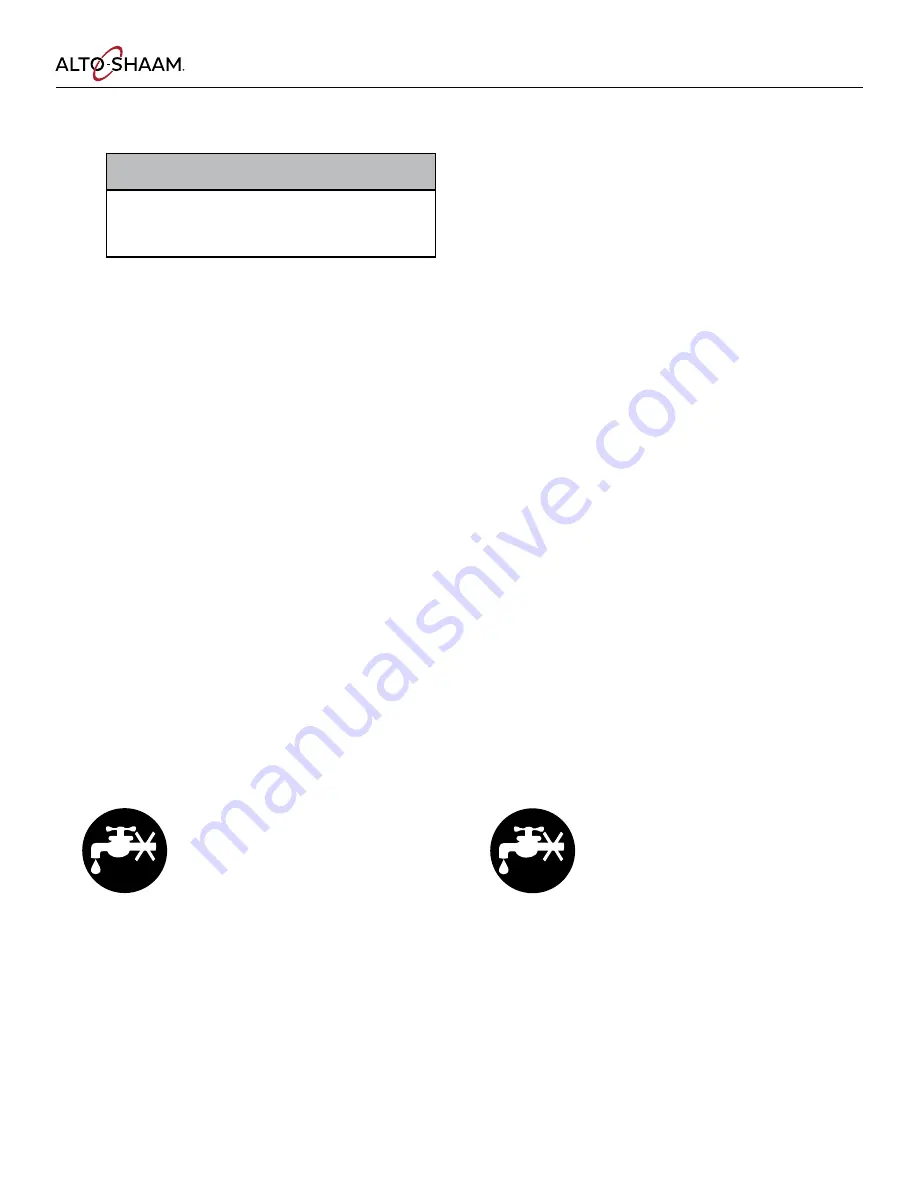
MN-35947
•
Rev 15
•
01/18
•
Combitherm® CT PROformance™ and CT Classic Series Installation Manual
•
51
Installation
Use a drinking quality, cold water supply only .
Water Quality Requirements
Water quality is of critical importance when installing
steam producing equipment of any kind, particularly
high temperature steam producing equipment. Water
that is perfectly safe to drink is composed of chemical
characteristics that directly affect the metal surfaces
of steam producing equipment. These chemical
characteristics differ greatly from region to region
throughout the U.S. and the world. Varying combinations
of pH; alkalinity; hardness; chlorides; total dissolved
solids; and other chemical characteristics, when subjected
to high temperatures, will cause water to have a tendency
to either scale or corrode.
Alto-Shaam has consulted with people who understand
the properties of water in order to provide water quality
standards that meet the broadest possible range of
acceptable water quality requirements to help protect
your investment.
We strongly urge water testing to ascertain the water
quality on site prior to the installation of any steam
producing equipment. Since water quality is an important
issue, Alto-Shaam is committed to provide as much
information as possible to help protect the investment
made in this equipment.
A water fi ltration system, when properly installed,
maintained, and combined with the required levels of
steam producing equipment maintenance, will help lessen
the affect water has on metal surfaces. It will not, however,
provide complete protection against all water damage
from region to region.
due to the complexity of water chemistry, it is important
to understand that water quality plays a signifi cant role in
the longevity of steam producing equipment. Water quality
and required maintenance of steam generating equipment
is the direct responsibility of the owner/operator. damage
incurred as a direct result of poor water quality and/or
surfaces affected by water quality is also the responsibility
of the owner/operator. damage due to water quality that
does not meet the minimum standards shown below is not
covered under the Alto-Shaam Combitherm warranty.
It is the sole responsibility of the owner/operator/
purchaser of this equipment to verify that the incoming
water supply is comprehensively tested and if required,
a means of “water treatment” provided that would meet
compliance requirements with the published water
quality standards published at right. Non-compliance
with these minimum standards will potentially damage
this equipment and/or components and VOId the
original equipment manufacturer’s warranty. Alto-Shaam
recommends using OptiPure® [www.optipurewater.com]
products to properly treat your water.
Alto-Shaam will continue our efforts to provide viable
solutions to ease the impact of water quality as it relates to
heat producing equipment.
WARNINg
Significant damage to the appliance cavity, elements, or
heat exchanger could result from improper water quality.
Failure to meet the water quality requirements and
observe this precaution will void the warranty.
WATER QuALITY REQuIREmENTS
Notice: To prevent water pipes from
bursting, the incoming water
supply should be off when the
appliance is not in use.
Notice: Verify that the water supply
is open before starting the
cleaning program.