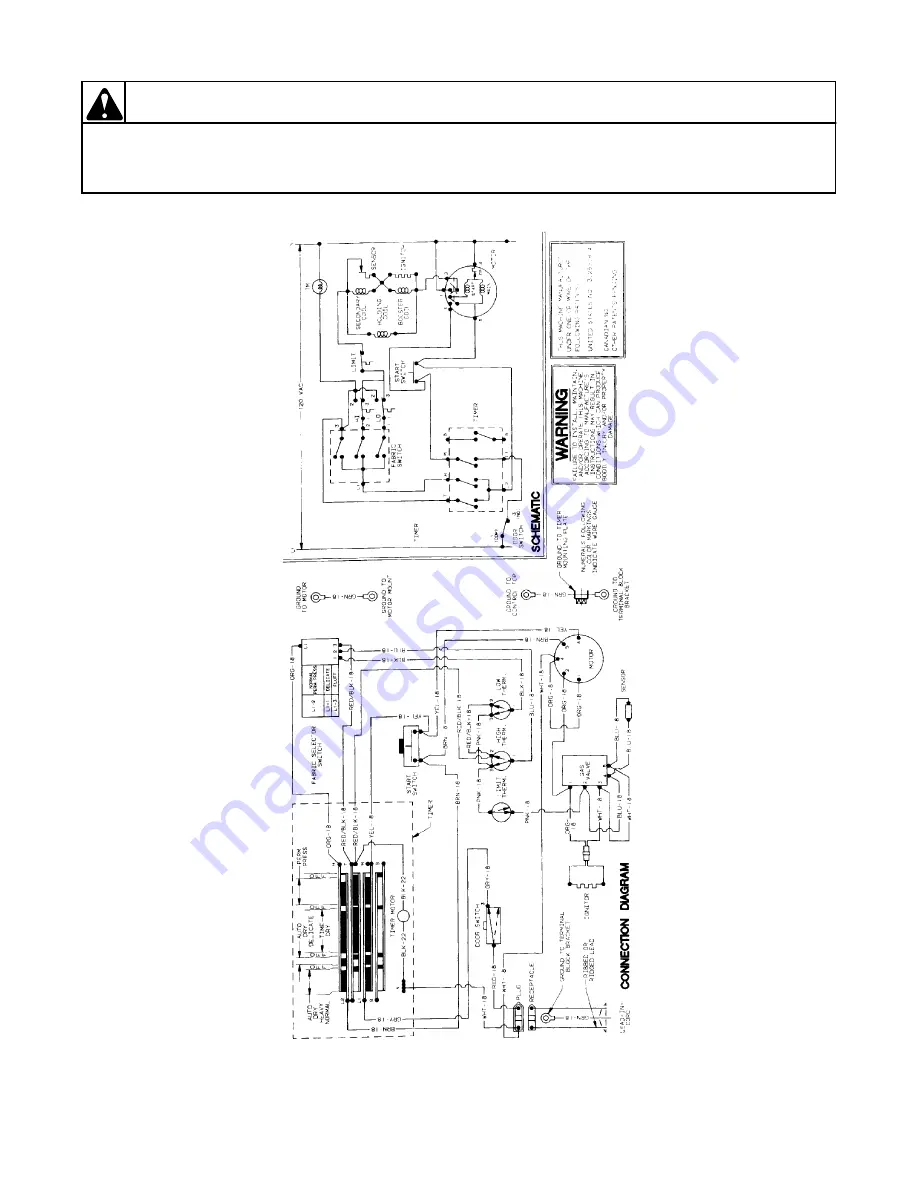
60549
107
Section 10 Wiring Diagrams
Failure to install, maintain, and/or operate this machine according to the manufacturer's
instructions may result in conditions which can produce bodily injury and/or property damage.
W030
WARNING
© Copyright, Alliance Laundry Systems LLC – DO NOT COPY or TRANSMIT
MODELS NG4519 AND NG4319
Through Serial No. S6242593XD