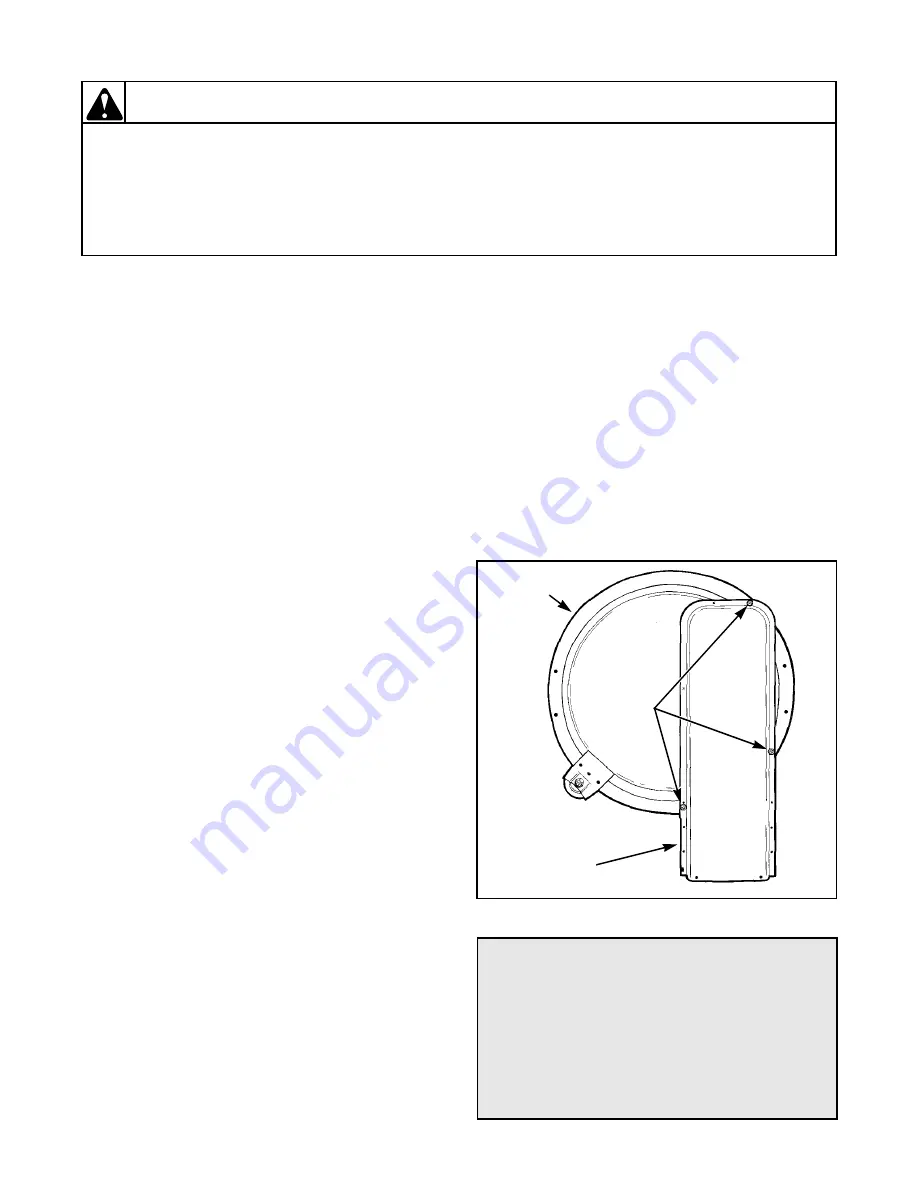
62
505872
Section 5 Service Procedures
To reduce the risk of electric shock, fire, explosion, serious injury or death:
• Disconnect electric power to the dryer(s) before servicing.
• Close gas shut-off valve to gas dryer(s) before servicing.
• Never start the dryer(s) with any guards/panels removed.
• Whenever ground wires are removed during servicing, these ground wires must be
reconnected to ensure that the dryer is properly grounded.
W001R1
WARNING
© Copyright, Alliance Laundry Systems LLC – DO NOT COPY or TRANSMIT
g. Manually rotate cylinder until one of the baffles
is at the 6:00 position and carefully remove
cylinder out through front of dryer.
NOTE: On models using unpainted, corrosion
resistant, coated steel cylinder, the cylinder must be
installed with the side marked “FRONT” or the
arrow pointing toward front of dryer.
h. Gas Models:
(1) Disconnect igniter wires at disconnect
blocks, sensor wires from sensor terminals,
and wires from gas valve coils at the quick
disconnect blocks. Refer to Figure 19.
(2) Remove screw from right side of burner
housing, holding burner tube in place.
Refer to Figure 23.
(3) Gently move burner tube toward rear of
dryer to disengage tab from slot on left side
of burner housing. Refer to Figure 19.
(4) Carefully rotate burner tube and igniter
counterclockwise so tab is at 8 o’clock
position.
(5) More air shutter end of burner tube slightly
to right and CAREFULLY remove burner
tube and igniter assembly out through front
of dryer.
IMPORTANT: The igniter is very fragile. Be careful
not to damage it during removal.
(6) Remove screw holding burner housing to
heat shroud. Refer to Figure 19.
(7) Remove screw holding front of burner
housing to dryer base and remove housing
out through front of dryer. Refer to
Figure 23.
(8) Remove four screws holding shroud to
heater box and remove shroud out through
front of dryer. Refer to Figure 19.
i. Electric Models:
(1) Remove two screws holding element and
plate to heater box, then pull element down
and away from heater box. Refer to
Figure 23.
j. Remove screw holding heat shield to dryer
base. Refer to Figure 35.
k. Remove one screw holding rear bulkhead to
terminal block bracket. While supporting
bulkhead, remove the four screws holding rear
bulkhead to mounting brackets, then lift
complete assembly out of dryer. Refer to
Figure 35.
l. To remove heat shield from heater box:
(1) Remove two screws holding heat shield to
heater box. Refer to Figure 35.
m. To remove heater box from rear bulkhead:
(1) Refer to Figure 37 for removal.
n. Rear mounting brackets:
(1) Remove five screws holding rear mounting
brackets to rear of dryer cabinet. Refer to
Figure 26.
Figure 37
DR011-SV-1
HEATER
BOX
REAR
BULKHEAD
HEATER
BOX
ATTACHING
SCREWS
To Test Heater Assembly:
(Electric Models)
1. Disconnect wires from heater assembly.
NOTE: Refer to appropriate wiring diagram
when rewiring heater assembly.
2. Set meter to read Ohms. Apply meter probes to
the heater assembly terminals. Meter should
read 10.4 Ohms ± .30 Ohms cold.