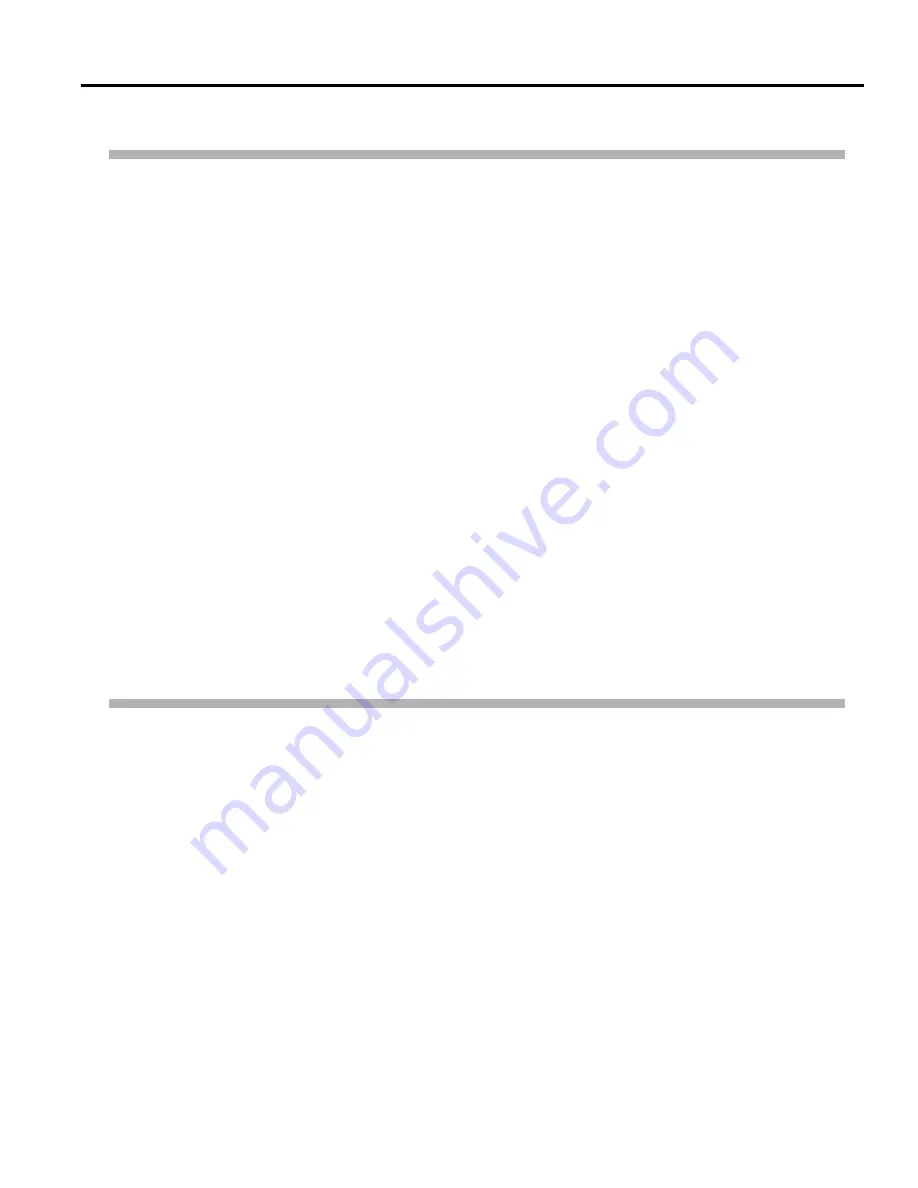
35
AT2000 XR Film Quality Troubleshooting
TROUBLESHOOTING
9.
FILM HAS SILVER / GREEN / BROWN COLOR
A. Confirm the following initial requirements for AT2000XR Automatic film processing;
1. Film is not outdated (within manufacturers recommended processing life) or defective.
2. Film used is designed for Automatic Processing.
3. Chemistry is not contaminated & within recommended useful life. Refer to
AVOIDING CHEMISTRY CONTAMINATION provided on page 37 to prevent problems.
4. WASH WATER is above 55°F.
5. WASH WATER is ON ( valve is open )
B. Check the chemistry temperature for being too COLD (optimum temp. setting of 82°F NOT achieved)
- Preview the processor's temperature setting as follows; POWER ON, push and hold the DISPLAY
SET-TEMP button on the keypad. The value displayed will start flashing, if NOT 82° then perform re-
adjustment as follows;
1. Open the flip lid on the top side of the Electronics Module, push and hold the DISPLAY SET- TEMP
button on the keypad and rotate the potentiometer until 83 is displayed.
2. Once reaching 83, slowly rotate counterclockwise until 82°F is achieved. (The processor's heat
control & display can be reviewed FUNCTION MODES FUNCTION CHART, page 15)
3. If chemistry temperature is below 82°F, and the display pre-set is 82°F - Analyze the heat control
components per the check sequence listed in TROUBLESHOOTING GUIDE SECTION 1 -
CHEMISTRY TEMPERATURE CONTROL PROBLEMS, Item D provided on page 27.
C. Check the CHEMISTRY REPLENISHMENT level control and pumping rate;
1. Inspect the fixer Drain Tube washer condition - Must be in good condition & seats well.
2. Analyze the chemistry replenishment for insufficient amounts per the check sequence listed in
TROUBLESHOOTING GUIDE SECTION 1 - REPLENISHER PUMP PROBLEMS provided on
page 26.
D. Check the FIXER Agitator freely spins (chemistry circulation)
1. Disassemble the agitator assemblies as shown by the BASE ASSEMBLY section, (page 48).
2. Analyze the agitator per the check sequence listed in the TROUBLESHOOTING GUIDE SECTION
1 - CHEMISTRY AGITATOR PROBLEMS provided on page 26.
10. FILM IS WET / TACKY AFTER PROCESSING
A. Confirm the following initial requirements for AT2000XR Automatic film processing;
1. Film is not outdated (within manufacturer's recommended processing life) or defective.
2. Film used is designed for Automatic Processing.
3. Chemistry is not contaminated & within recommended useful life. Refer to
AVOIDING CHEMISTRY CONTAMINATION provided on page 37 to prevent problems.
4. Chemistry used is designed for roller transport processors.
5. The room should be properly vented, and below 80°F.
6. Verify there is a minimum of 10 (room volume) air changes per hour in the room.
B. Check the baffles in the Wash/Dry rack, verify they are installed correctly. Refer to the detail view of
assembly in the ROLLER TRANSPORT PARTS illustration (page 50) and note that the Inner Baffle is
installed before the Outer Baffle
C. Check the WASH WATER for inadequate, or no flow of water into wash tank by analyzing the wash
water for insufficient amounts per the check sequence listed in TROUBLESHOOTING GUIDE
SECTTION 1 - WASH WATER PROBLEMS provided on page 28.
D. Check the CHEMISTRY REPLENISHMENT level control and pumping rate;
1. Inspect the fixer Drain Tube washer condition - Must be in good condition & seats well. Analyze
the chemistry replenishment for insufficient amounts per the check sequence listed in TROU-
BLESHOOTING GUIDE SECTION 1- REPLENISHER PUMP PROBLEMS provided on page 26.
E. Check the air temperature and air movement exiting the dryer at the film exit by verifying that the air
exiting is warm and blowing out. If not, perform procedures listed in TROUBLESHOOTING GUIDE
SECTION 1- DRYER FAN / AIR HEATER PROBLEMS provided on page 26.