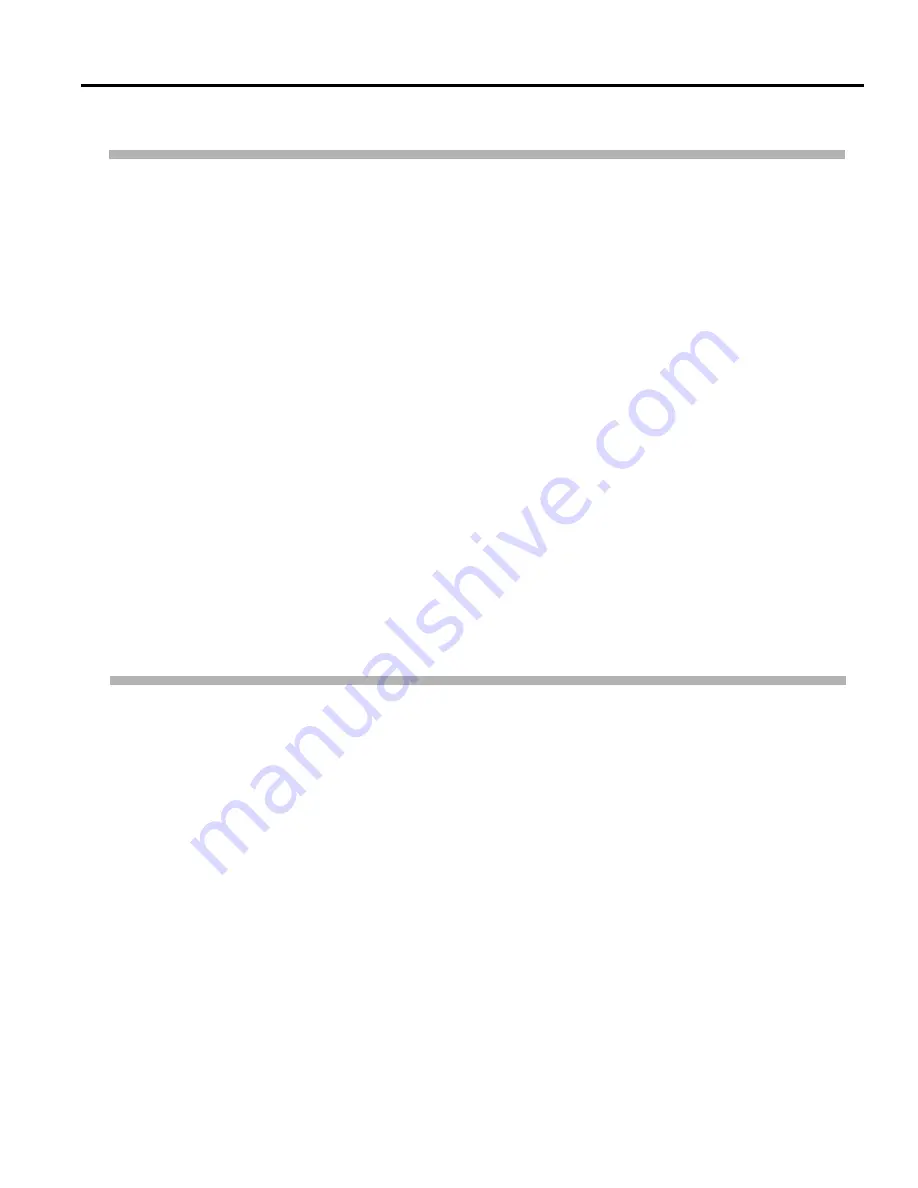
33
AT2000 XR Film Quality Troubleshooting
TROUBLESHOOTING
5.
FILM HAS STREAKING CONSISTENTLY REPEATING
A. Confirm the following initial requirements for AT2000XR Automatic film processing;
1. Chemistry is not contaminated and within recommended useful life. Refer to
AVOIDING CHEMISTRY CONTAMINATION provided on page 37 to prevent problems.
2. Film used is designed for Automatic Processing
3. Confirm that a CLEANING FILM has been processed after the READY light illuminates. This is
done at the daily start up, and every 2 hours of idle time.
4. Check the wash drain tube and verify it DOES NOT have a rubber washer.
5. Check the solution levels are at the proper height.
6. Check & verify the drive motor continually runs during a processing cycle.
B. Check the leveiness of the processor by making sure that the leveling frame "Bubble" indicates proper
level of unit, adjust feet as necessary.
C. Check the cleanliness of the Transport Racks. Clean the racks, if necessary, per the MAINTENANCE
requirements in the USER'S MANUAL.
D. Check the squareness of the Transport Racks;
1. Place a transport rack (independently) onto a FLAT & LEVEL surface, the rack should rest evenly
on it's side plates. If it does not, loosen (but don't remove) the screws and twist the rack assembly
to get it to sit flush. Once attained, re-tighten the screws and verify the rack assembly is still sit-
ting flush (re-perform procedure if necessary). Check all TRANSPORT RACKS in this manner to
verify squareness.
2. Check for damaged gears & rollers on rack assemblies - Replace (if feasible) as required
6.
FILM HAS STREAKING RANDOMLY
A. Confirm the followng initial requirements for AT2000XR Automatic film processing;
1. Chemistry is not contaminated and within recommended useful life. Refer to
AVOIDING CHEMISTRY CONTAMINATION provided on page 37 to prevent problems.
2. Film used is designed for Automatic Processing
3. Chemistry used is designed for roller transport processors.
4. Check the wash drain tube and verify it DOES NOT have a rubber washer.
5. Check the solution levels are at the proper height.
B. Check the CHEMISTRY REPLENISHMENT level control and pumping rate;
1. Inspect the both developer & fixer Drain Tube washer condition - Must be in good condition
2. Confirm that both developer & fixer Drain Tubes firmly seat in their drain sockets.
3. Analyze the chemistry replenishment for insufficient amounts per the check sequence listed in
TROUBLESHOOTING GUIDE SECTION 1 - REPLENISHER PUMP PROBLEMS provided on
page 26.
C. Check the Agitators freely spin (chemistry circulation) - Disassemble the agitator assembies as shown
by the BASE ASSEMBLY section, (page 48). Analyze the agitator per the check sequence listed in
TROUBLESHOOTING GUIDE SECTION 1 CHEMISTRY-AGITATOR PROBLEMS provided on page
26.