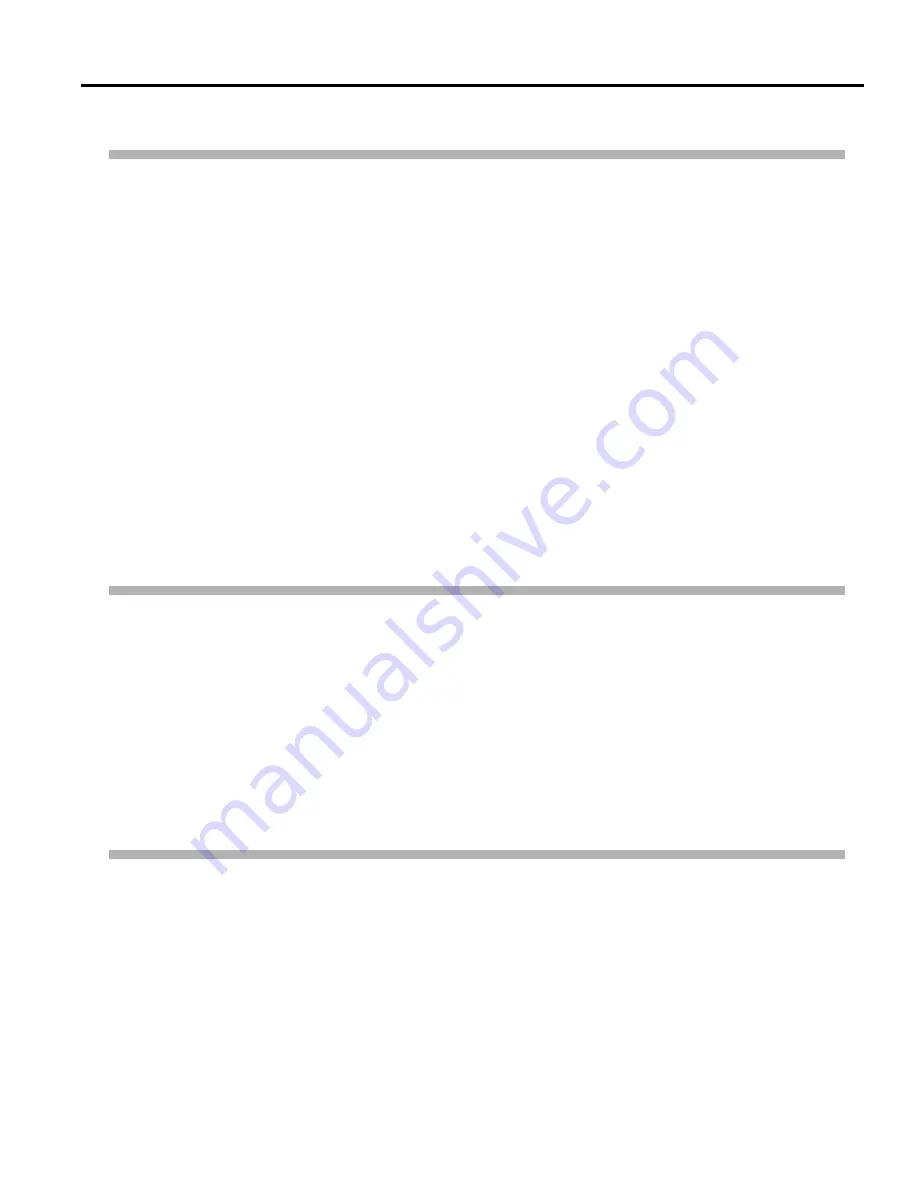
25
4.
PROCESSOR STOPS IN MID-CYCLE (Stops before film exits the dryer)
A. Check for a low voltage condition due to another large motor (i.e.; refrigerator, compressor) on the
same circuit – If the other motor starts during a process cycle, it can draw too much voltage and interrupt the
cycle causing the AT2000XR to reset to stand-by.
If on a shared circuit, relocate to another circuit / dedicated circuit to eliminate problem.
B. Check for a temporary power outage – End results will be same as in item A
C. Check all the transport racks for squareness and inspect the gears for any broken parts;
1. If NOT square, place on level surface and loosen the tie rod screws but don’t remove. Firmly hold
down the rack plates so they sit flat against the surface and retighten the screws.
2. If any gears are broken, replace the appropriate gear if feasible or the affected transport.
D. Check the cleanliness of the transport racks – Failure to maintain the processor per the requirements
can cause the transport rollers to become “slimy” and allow the films to slip during processing.
If at all questionable, clean the transports and reiterate that the AT2000XR requires routine main-
tenance, which is fully described in detail in the USER’S MANUAL.
E. Reiterate if films are not fed straight when inserting into film inlet, they can get caught in the transports.
NOTE:
Pedo films must be processed lengthwise
F.
Check the process time for both speeds – Hold Film Shutter open for 5 seconds then release;
1. If ENDO speed processing time after releasing the shutter is LESS THAN 2 min 40 sec, replace
Electronics Module (p/n 45415)
2. IF NORMAL speed processing time after releasing the shutter is LESS THAN 5 min 55 sec, replace
Module (p/n 45415)
5.
DRIVE MOTOR “NORMAL” SPEED DOES NOT RUN
A. Check that the Top Cover assembly is seated squarely on the Base – If not, the interlock switch may
not be engaged which will prevent the transport drive motor from running.
B. Check the interlock switch by verifying continuity between the switch leads when tripped. Refer to the
SYSTEM SCHEMATIC, page 20, to test at J10, pins 1 & 2. After disconnecting from the electronics
module, measure 115 vac on the two Molex pin connectors originating from the electronics module.
C. Check all the transport racks gears for any broken parts;
If any gears are broken, replace the appropriate gear if feasible or the affected transport.
D. Check that the Drive Motor connector J3 is properly attached inside the connector compartment.
E. Refer to the TEST POINT CHART, page 19, connect a voltmeter to J3, pins 2 & 3, and select the nor-
mal mode. Start a process cycle. Make sure the unit is in the process mode and measure the voltages.
1
If voltage is 103.5 – 126.5VAC, replace the Drive Motor (p/n 45472)
2
If voltage is NOT 103.5 – 126.5VAC, replace Electronics Module (p/n 45415)
6.
DRIVE MOTOR “ENDO” SPEED DOES NOT RUN
A. Check that the Top Cover assembly is seated squarely on the Base – If not, the interlock switch may
not be engaged which will prevent the transport drive motor from running.
B. Check the interlock switch by verifying continuity between the switch leads when tripped. Refer to the
SYSTEM SCHEMATIC, page 20, to test at J10, pins 1 & 2. After disconnecting from the electronics
module, measure 115 vac on the two Molex pin connectors originating from the electronics module.
C. Check all the transport racks gears for any broken parts;
If any gears are broken, replace the appropriate gear if feasible or the affected transport.
D. Check that the Drive Motor connector J3 is properly attached inside the connector compartment.
E. Refer to the TEST POINT CHART, page 19, connect a voltmeter to J3, pins 1 & 3, and select the endo
mode. Start a process cycle. Make sure the unit is in the process mode and measure the voltages.
1
If voltage is 103.5 – 126.5VAC, replace the Drive Motor (p/n 45472)
2
If voltage is NOT 103.5 – 126.5VAC, replace Electronics Module (p/n 45415)
TROUBLESHOOTING
AT2000 XR Operation & Function Troubleshooting