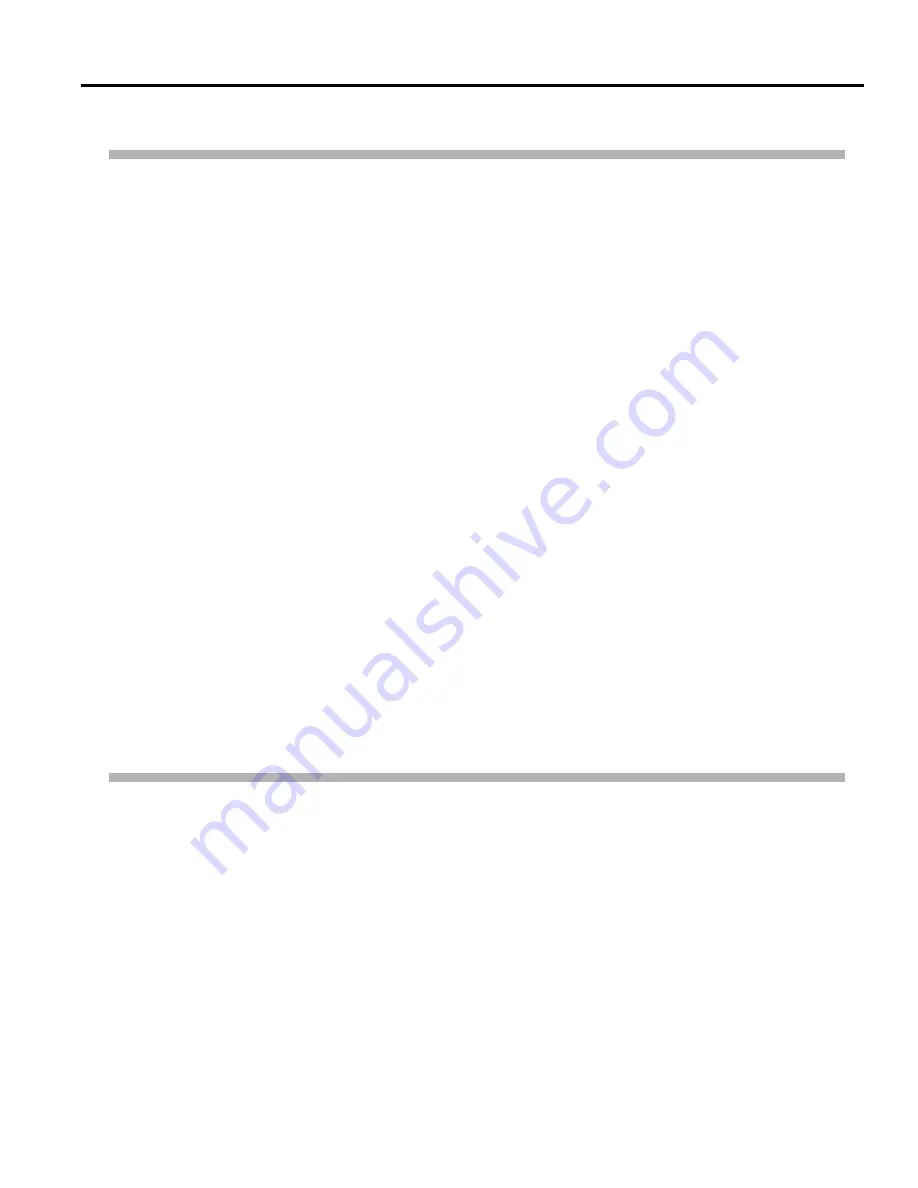
27
10. CHEMISTRY TEMPERATURE CONTROL PROBLEMS
A. Verify the wash water temperature is 55°F – 80°F, if NOT, adjust as required and continue.
1
Cooler than 55°F water results in thermal heat transfer from the adjacent Fixer tank.
2
Warmer than 80° water results in damaged film and temperature rise in chemistry.
B. Check the room temperature - Above 82°F air temperature adds to processor chemistry heating.
1 If higher than 82°F exists, advise that additional ventilation is required to lower room temp.
2 Advise a minimum of 10 (room volume) air changes per hour are required.
C. Chemistry temperature is either too HOT or too COLD (optimum temp. setting of 82°F NOT achieved) –
Preview the processor’s temperature setting as follows; POWER ON, push and hold the DISPLAY
SET-TEMP button on the keypad. The value displayed will start flashing, if NOT 82° then readjust as
follows;
Open the flip lid on the top side of the Electronics Module, push and hold the DISPLAY SET-TEMP
button on the keypad and rotate the potentiometer until 83 is displayed. Once reaching 83, slowly
rotate counterclockwise until 82° is achieved. (The processor’s heat control and display can be
reviewed FUNCTION MODES FUNCTION CHART, page 14)
D. Chemistry temperature is either too HOT or too COLD and the display pre-set is 82°F –
Analyze the heat control components one-by-one using the TEST POINT CHART, CONNECTOR
DIAGRAMS and the SYSTEM SCHEMATIC, page 19;
1
Check the resistance value of the THERMISTOR PROBE @ J5, pins 1 & 3 on thermistor’s
connector side, and refer to the resistance vs. temperature chart. The measured value on the
probe must be within 1% of the chart value. If not, replace Thermistor probe (p/n 45970)
2
Check the resistance value of the wiring harness for continuity @ J1, pins 13 & 14 and refer to the
resistance vs. temperature chart. The measured value must be within 1% of the chart value. If
NOT, inspect the wiring harness for corrosion on connector pins or poor lugging.
3
Check the resistance value of the HEATER PAD @ J4, pins 1 & 2 on the heater’s connector side.
The measured value must be 52.5 – 60 ohms, if NOT, replace Heater Pad (p/n 45950) as shown-
by the BASE ASSEMBLY- HEATER PAD section, (page 54).
4
Check the resistance value of the wiring harness for continuity @ J1, pins 3 & 10. The measured
value must be must be 52.5 – 60 ohms. If NOT, inspect the wiring harness for corrosion on
connector pins or poor lugging.
5
Check voltage @ J4, pins 1 & 2. If voltage is NOT 103.5 – 126.5VAC, or if all prior checks are
satisfactory, replace the Electronics Module (p/n 45415)
11. KNOCKING/ THUMPING NOISES DURING PROCESS CYCLE
A. Transport and / or drive train is jammed or out of adjustment - Remove the transport rack assembly as
depicted in the ROLLER TRANSPORT section, (page 57).
1
Check the baffles in the Wash/Dry rack, verify they are installed correctly. Refer to the detail view
of assembly in the Roller Transport Parts illustration (page 58). Note the inner baffle is installed
before the outer baffle.
2
Check transport racks for;
a. Properly seated on worm gear & latched in place. Reseat & latch if dertermined so.
b. Transport racks do not have broken gears. Replace rack if broken gears are found.
c. Latches are broken or dislodged from the drive block. Rectify problem as required.
d. Racks are square (not twisted) when resting on a flat surface, if not then adjust as mentioned
in Film Sreaking Troubleshooting (page 32)
3
Check for thumping sounds coming from the front top of the processor, if so then check shutter
guard, it may be bent inward slightly and is rubbing against the inlet rollers of the Developer
Transport Rack. If this is the case, re-adjust as necessary to alleviate the interference by loosening
the retaining screws & pivoting the bar. Re-tighten the screws when adjustment is complete.
4
Check for film jams (films stuck in racks), if so; Allieviate the jam as necessary to get the rack('s)
working.
TROUBLESHOOTING
AT2000 XR Operation & Function Troubleshooting