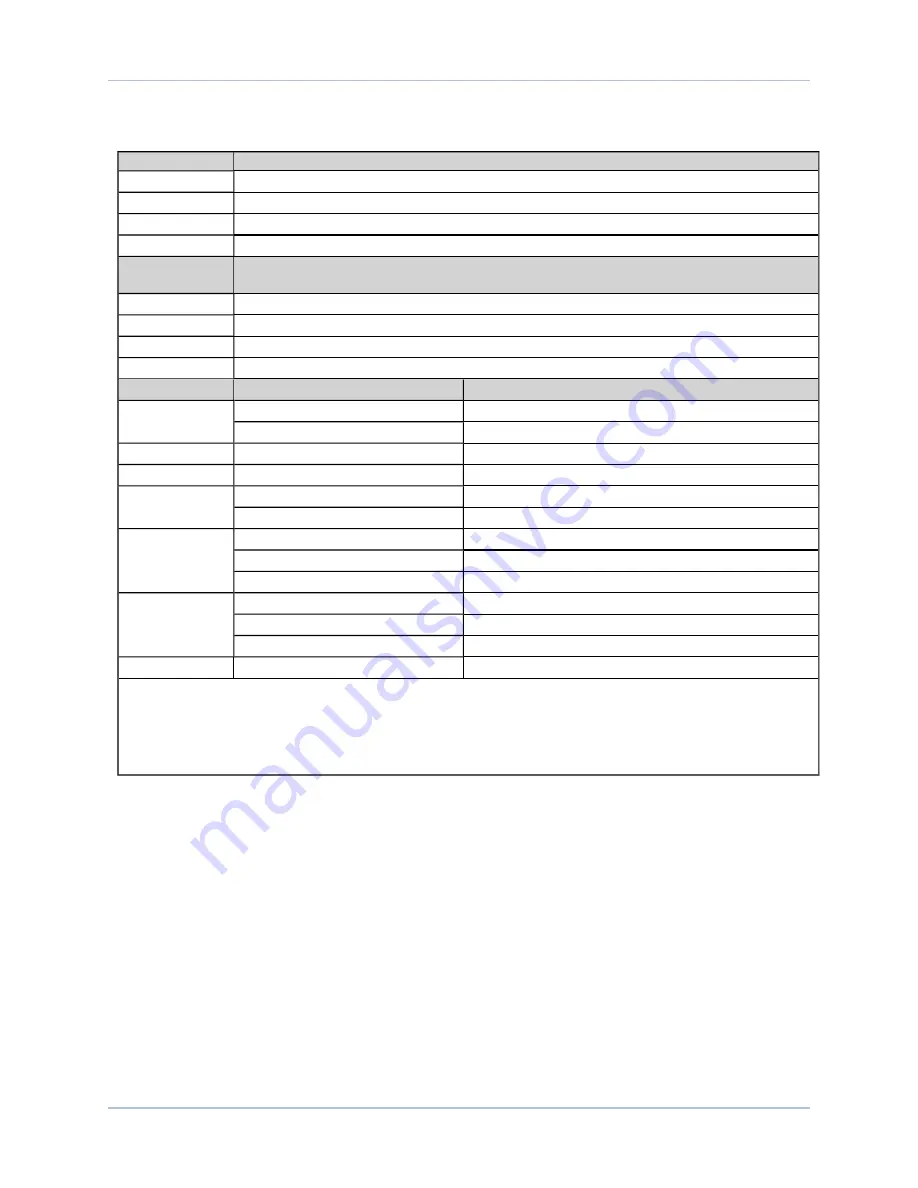
BL
Wiring Configurations
Table 3-1:
Velocity Command Mode BL Configuration
DIP
Switch
Setting
2
1 through 4
Select peak current limit
5 through 8
Select continuous current limit
9 (Test)
Open
5
10 (Mode)
Open
5
Potentiometer
1
Setting
3
INPUT
1/3 CW from full CCW (recommended starting point)
GAIN
Full CW (recommended starting point)
TACH
Full CW (recommended starting point)
BAL
N/A
Jumpers
Setting
4
Description
JP7
1-2 OUT, 2-3 IN
5
Analog Tachometer Feedback
1-2 in, 2-3 out
Electronic (encoder) Tachometer Feedback
JP9
1-2 in, 3-4 out, 5-6 out, 7-8 out
Six-step mode
JP13
1-2 in, 3-4 out, 5-6 out, 7-8 out
Six-step mode
JP3
1-2 IN, 2-3 OUT
5
Brushless mode
1-2 out, 2-3 in
Brush mode
JP4, JP10,
JP12
JP4: 1-2 IN, 2-3 OUT
5
0° Commutation
JP10: 1-2 OUT, 2-3 IN
5
Half Step AC Commutation
JP12: 1-2 OUT, 2-3 IN
5
Half Step AC Commutation
JP4, JP10,
JP12
JP4: 1-2 out, 2-3 in
30° Commutation Offset
JP10: 1-2 in, 2-3 out
Full Step AC Commutation
JP12: 1-2 in, 2-3 out
Full Step AC Commutation
JP8
1-2 IN, 2-3 OUT
5
Standard Mode
1. These initial settings will usually generate a stable system under the assumption that the tachometer feedback gain is around 6
volts/Krpm, or, if an encoder is used and the line resolution is between 1,000 and 1,500 per revolution.
2. For more information about the DIP
Switch, refer to Section 2.4. DIP Switch.
3. For more information about the Potentiometer, refer to Section 2.5. Potentiometers (POTs).
4. Refer to Section 4.1. Control Board Assembly for jumper locations.
5. Default
To minimize the possibility of electrical shock and bodily injury, decouple the motor from the mechanical sys-
tem to avoid injury if the motor begins to spin.
Starting with a zero input command signal, apply power to the amplifier. If the motor spins uncontrollably,
remove power and switch the polarity of the tachometer input signal. If an encoder is being used, switch the
sine and cosine input signals. Verify compliment signals (Sin & Sin-N, Cos & Cos-N) are of correct phasing.
Again, apply power to the amplifier. If the motor begins to oscillate, turn the TACH pot CCW until the oscil-
lation stops. The GAIN and TACH potentiometers can be adjusted to provide maximum stiffness on the
motor shaft.
Use the BAL pot to cancel any bias in the internal or external control circuit that would cause the motor to
rotate when the input command signal is zero. If the TEST switch is closed, the effects of the BAL pot will be
magnified. This is useful when applying a test bias signal (for velocity or torque modes) to the amplifier with-
out introducing an external command signal.
32
Chapter 3
www.aerotech.com
Summary of Contents for BL 10-40
Page 4: ...BL Table of Contents iv www aerotech com...
Page 6: ...BL List Of Figures vi www aerotech com...
Page 8: ...BL List of Tables viii www aerotech com...
Page 10: ...x www aerotech com BL Declaration of Conformity...
Page 16: ...BL Introduction 6 Chapter 1 www aerotech com...
Page 38: ...BL Installation and Configuration 28 Chapter 2 www aerotech com...
Page 54: ...BL Wiring Configurations 44 Chapter 3 www aerotech com...
Page 68: ......