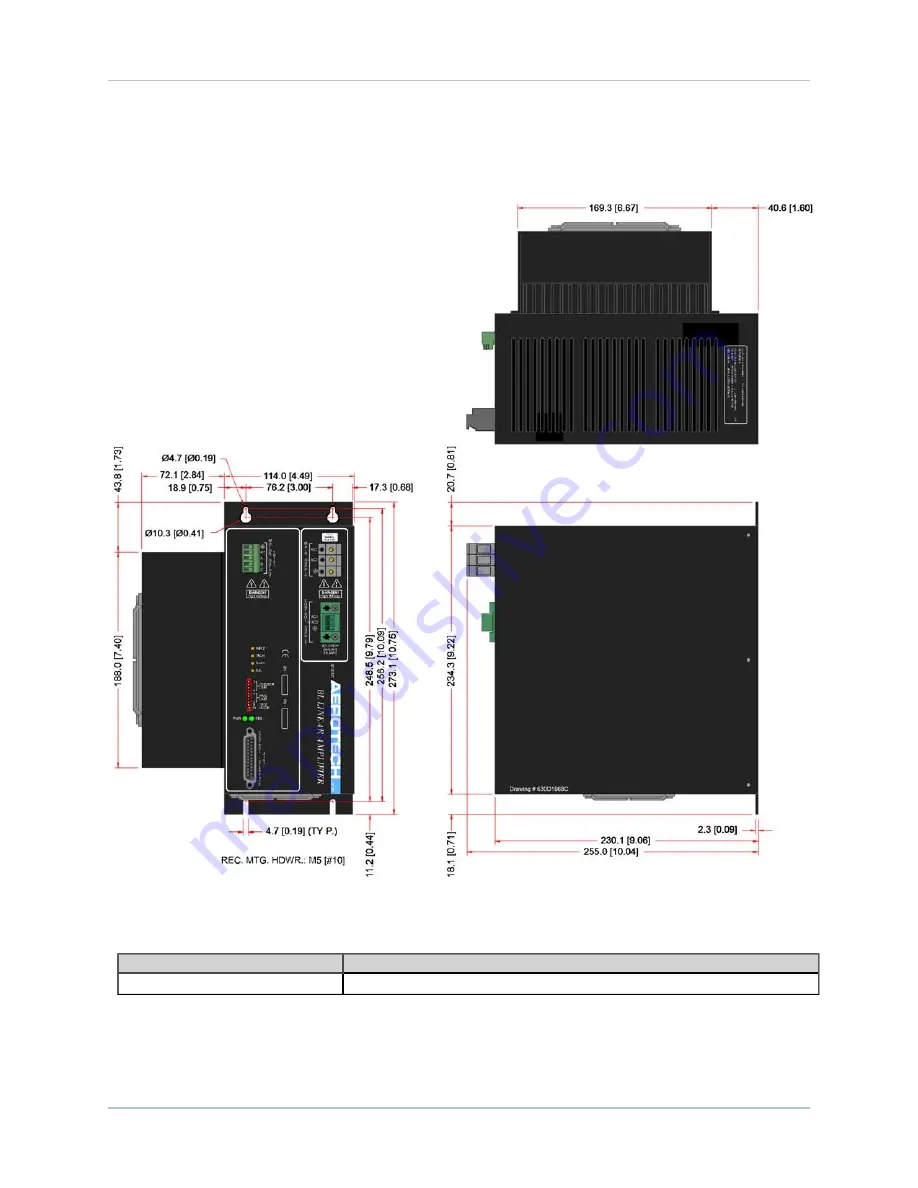
BL
Introduction
1.2. Mechanical Design
Each unit should be separated from other drives and surrounded by 50 mm (2") of free air space. A space of
100 mm (4") should be allowed along the front of the unit for cable connections.
Figure 1-3:
Dimensions
Table 1-3:
Physical Specifications
Model
Weight
BL
8.5 kg [18.8 lb]
4
Chapter 1
www.aerotech.com
Summary of Contents for BL 10-40
Page 4: ...BL Table of Contents iv www aerotech com...
Page 6: ...BL List Of Figures vi www aerotech com...
Page 8: ...BL List of Tables viii www aerotech com...
Page 10: ...x www aerotech com BL Declaration of Conformity...
Page 16: ...BL Introduction 6 Chapter 1 www aerotech com...
Page 38: ...BL Installation and Configuration 28 Chapter 2 www aerotech com...
Page 54: ...BL Wiring Configurations 44 Chapter 3 www aerotech com...
Page 68: ......