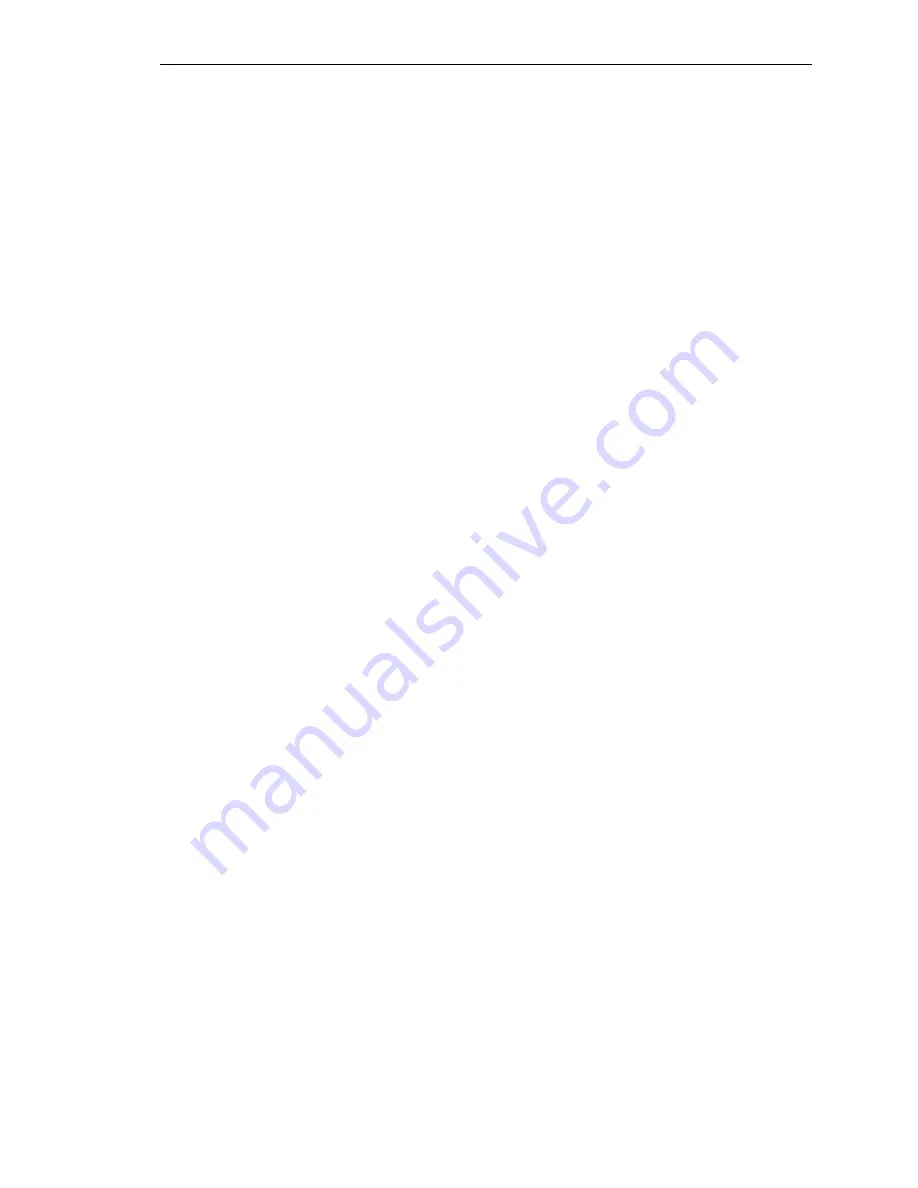
11
Limiting Joint Travel
The joint motion or travel is limited by both software and hardware. The
programmable software limits are known as softstops; the fixed
hardware limits are called hardstops. (See Figures 2-5 to 2-8 and Table 2-
1.)
Softstops
The robot controller uses softstops to determine the range of motion it
will allow the robot to move under program control, or to be moved by
an operator using the manual control pendant. If a robot joint travels
beyond a softstop, the controller will automatically shut off arm power
(high power), thereby activating the brakes. Furthermore, the controller
will not allow the robot power to be turned on while any joint is beyond
its softstop. If this situation occurs, use the brake release button (see the
section on Brakes later in this chapter) and manually move the arm back
within the softstop limits.
Under operator control (using the manual control pendant to move the
robot) the robot will stop very abruptly when it encounters a softstop.
This abruptness is due to the high-torque motors, there is no hardstop at
these locations.
Occasions may arise when it becomes mandatory to limit the travel of
one or more of the joints within the normal working envelope. This can
be easily accomplished by adjusting softstops using the CONFIG_R
utility program, which is supplied with the system.
NOTE
For further information concerning joint travel limitation,
refer to the Instructions for Adept Utility Programs manual
furnished with your system.
Hardstops
In most cases the softstop will prevent joint travel from contacting a
hardstop; however, contact is possible during high-speed operation. The
hardstops are designed to withstand large forces without damaging the
robot.
The hardstops for Joints 1, 2, and 3 are fixed mechanical stops. The
hardstop for Joint 4 is designed to slip slightly if impacted sufficiently. If
the Joint 4 hardstop slips, it should be reset. Refer to the procedure in
Chapter 4 on how to diagnose a slipped Joint 4 hardstop.
Summary of Contents for AdeptThree
Page 1: ...AdeptThree Robot User s Guide PRELIMINARY VERSION...
Page 3: ......
Page 8: ......
Page 14: ...AdeptThree User s Guide 6 NOTES...
Page 21: ...13 Figure 2 7 Joint 3 Hardstop...
Page 25: ...17 Figure 2 11 AdeptThree Robot Working Envelope...
Page 28: ...AdeptThree User s Guide 20 NOTES...
Page 31: ...23 Figure 3 1 AdeptThree with Calibration Fixture...
Page 40: ...AdeptThree User s Guide 32 Figure 3 6 Mounting Spool to Floor Installation Detail...
Page 44: ...AdeptThree User s Guide 36 Figure 3 8 Quill Flange Dimensions...
Page 50: ...AdeptThree User s Guide 42 Figure 3 11 Tower Card User Signal and Voltage Lines...
Page 54: ...AdeptThree User s Guide 46 NOTES...
Page 57: ...49 Figure 4 1 Joint 3 and Joint 4 Lubrication...
Page 60: ...AdeptThree User s Guide 52 NOTES...
Page 64: ...Adept CC Controller 56 NOTES...
Page 68: ...AdeptThree User s Guide 2...