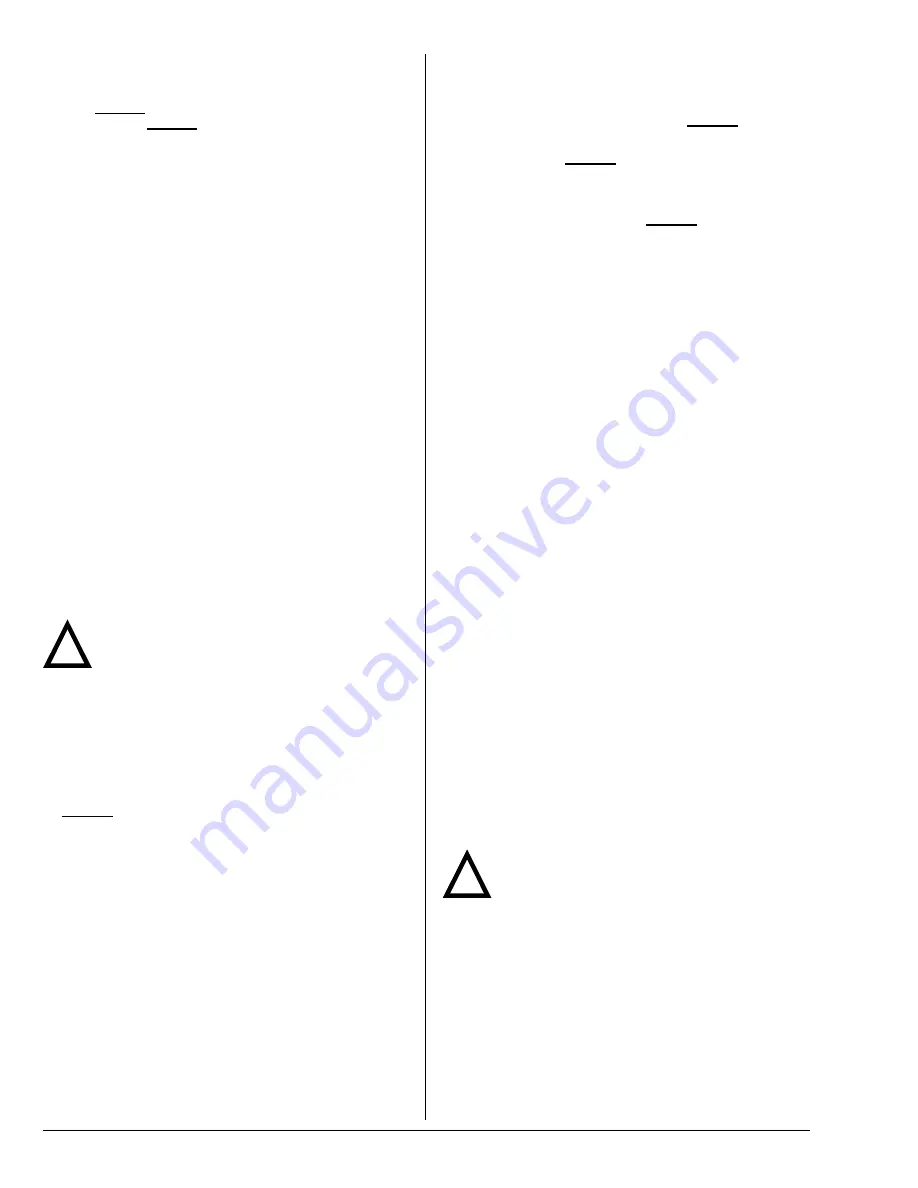
22
American Dryer Corp.
113546 - 2
!
Regulated Gas Valve
Refer to “Gas Pressure Adjustment” (this page) to adjust
the gas valve to the appropriate burner pressure listed
on
page 19
. The supply pressure must also match what
is listed on
page 19
for the type of gas to be used.
IMPORTANT:
Conversion must be performed by competent
technicians in accordance with local and state codes.
IMPROPER ASSEMBLY OR ADJUSTMENTS CAN CAUSE
HAZARDOUS CONDITIONS.
Gas Pressure Adjustment
IMPORTANT:
When converting from one gas to another
with regulated gas conversion kit, the following procedures
must be performed.
Disconnect electrical power to the dryer.
To adjust gas valve’s internal regulator, remove the regulator
vent cap (figure 5). Turn the plastic adjustment screw in the
valve. Turn the screw clockwise to raise pressure and
counterclockwise to lower pressure.
Gas (burner) pressures are measured with the burner in
operation for all burner adjustment conditions. Refer to “Gas
Pressure Test Procedure” for instructions on this procedure.
Therefore once the necessary adjustments have been made,
the dryer must be operated in a heating cycle to verify that the
pressure is correct. If it is not correct, you must discontinue
the power to the unit and make further adjustments. Repeat
these steps as many times as necessary to achieve the correct
burner pressure. Once the adjustment of the valve is
complete, the vent cap must be replaced and sealed with, for
example, paint to prevent maladjustment by the user. Operate
the dryer through one complete cycle to ensure proper
operation.
Warning (CE Dryers)
This appliance must only be operated with the gas
type indicated on the dryer’s rating plate. If the
appliance is converted (gas type changed), a new rating
plate must be obtained from American Dryer Corporation
(dryer’s serial number is required to purchase a conversion
kit).
Gas Pressure Testing
For proper operation, the gas pressure must be correct,
consistent and maintained at the gas pressure rates shown
on
page 19
. Provisions are made at the gas valve for taking
gas pressure readings.
There are two types of devices used to measure gas pressure.
They are the spring/mechanical type gauge and the
manometer. The use of the spring/mechanical type gauge is
not recommended because they are very easily damaged and
are not always accurate. The preferred type of gauge is the
manometer because it is a simple device to use and is highly
accurate. A manometer is simply a glass or transparent plastic
tube with a scale graduated in inches or millibars. When it is
filled with water and pressure is applied, the water in the tube
rises, showing the exact gas pressure.
Gas Pressure Test Procedure
Turn gas cock in gas supply line to “OFF” position.
CE Dryers: Back out miniature screw inside pressure tap and
attach manometer. Refer to figure 5 on
page 21
.
Non-CE Dryers: Install pressure tap and attach manometer.
Refer to figure 5 on
page 21
.
Turn gas cock to “ON” position.
Start the dryer in Heat Mode and wait for ignition. Gas manifold
pressure should be as shown on
page 19
.
If the gas pressure needs to be adjusted, refer to “Gas
Pressure Adjustment” (this page).
Once test is complete, turn gas cock to “OFF” position.
Remove manometer. Tighten screw inside the pressure tap
(50 Hz dryers) or reinstall plug (60 Hz dryers).
Turn gas cock to “ON” position and check for leaks with soap
solution with main burner “ON.”
Water Information_____________________
(For Optional Fire Suppression System)
Before You Start
Check Local Codes and Permits
Call your local water company or the proper municipal authority
for information regarding local codes.
IMPORTANT:
It is your responsibility to have all plumbing
connections made by a qualified professional to ensure that
the plumbing installation is adequate and conforms to local,
state, and federal regulations or codes.
It is the installer’s or owner’s responsibility to see that the
required water pressure, pipe size, or connections are
provided. The manufacturer assumes no responsibility if
the fire suppression system is not connected, installed, or
maintained properly.
Installation
Water Supply
The fire suppression system must be supplied with a minimum
water pipe size of 1/2-inch (12.7 mm) and be provided with 40
psi +/- 20 psi (2.75 bar +/- 1.37 bar) of pressure.
If the rear area of the dryer or the water supply is located in
an area where it will be exposed to cold/freezing temperatures,
provisions must be made to protect these water lines from
freezing.
Warning
If the water in the supply line or water solenoid
valve freezes, the fire suppression system will be
inoperative!!
Water Connections
The water connection is made to a 3/4”-11.5 NH hose or 3/4”
B.S.P. adaptor, depending on the destination country. A flexible
supply line/coupling must be used in an effort to avoid
damaging the electric water solenoid valve.
NOTE:
The 3/4”-11.5 NH is a standard hose coupling screw
thread. It is not to be confused with 3/4” N.P.T., or 3/4
B.S.P. The sealing of an NH connection is made with a
washer as opposed to the mating threads of an N.P.T. or
B.S.P. assembly. The 3 thread designs are not compatible.
!
Summary of Contents for AD120i
Page 30: ...ADC Part No 113546 2 08 13 14...