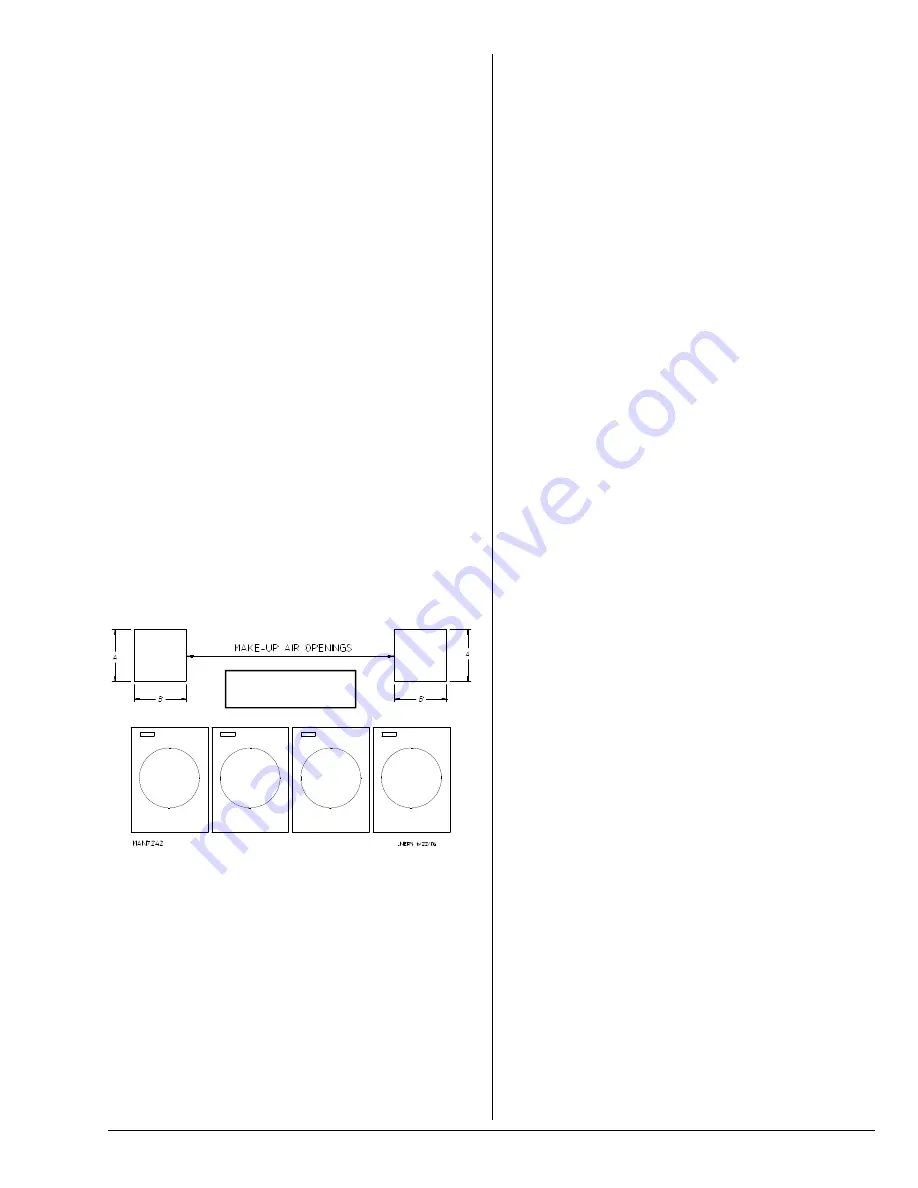
113546 - 2
www.adclaundry.com
11
Exhaust Requirements ________________
Exhaust ductwork should be designed and installed by a
qualified professional. Improperly sized ductwork will create
excessive back pressure, which results in slow drying,
increased use of energy, and shutdown of the burner by the
airflow (sail) switch, burner hi-limits, or lint chamber hi-limit
protector thermostat. The dryer must be installed with a proper
exhaust duct connection to the outside.
The dryer shall not be exhausted into any gas vent, chimney,
wall, ceiling or concealed space of a building.
The design of the flue system shall be such that any
condensate formed when operating the appliance from cold
shall either be retained and subsequently re-evaporated or
discharged.
CAUTION: This dryer produces combustible lint and
must be exhausted to the outdoors.
Improperly sized or installed exhaust ductwork can
create a potential fire hazard.
The ductwork should be laid out in such a way that the
ductwork travels as directly as possible to the outdoors with
as few turns as possible. There should be a minimum
6-inch (15.24 cm) clearance between the back guard and the
first bend in the ductwork for ease of servicing. Single or
independent dryer venting is recommended. It is suggested
that the use of 90° turns be minimized; use 30° and/or 45°
bends instead. The radius of the elbows should preferably
be 1-1/2 times the diameter of the duct. All ductwork should
be smooth inside with no projections from sheet metal screws
or other obstructions, which will collect lint. When adding
ducts, overlap the duct being connected. All ductwork joints
must be taped to prevent moisture and lint from escaping into
the building. Back draft dampers must be installed in all
commonly ducted systems. (This dryer comes equipped with
a back draft damper installed.) Inspection doors should be
installed at strategic points in the exhaust ductwork for periodic
inspection and cleaning of lint from the ductwork.
IMPORTANT:
It is recommended that exhaust or booster
fans not be used in the exhaust ductwork system.
Exhaust back pressure measured by a manometer/
magnehelic in the exhaust duct must be no less than 0 and
must not exceed 0.7 in WC (1.7 mb).
Fresh Air Supply Requirements _______
This appliance may only be installed in a room that meets the
appropriate ventilation requirements specified in the national
installation regulations.
When the dryer is operating, it draws in room air, heats it,
passes this air through the tumbler, and exhausts it out of the
building. Therefore, the room air must be continually
replenished from the outdoors. If the make-up air is
inadequate, drying time and drying efficiency will be adversely
affected. Ignition problems and sail switch “fluttering” problems
may result, as well as premature motor failure from
overheating. The dryer must be installed with provisions for
adequate combustion and make-up air supply.
Air supply (make-up air) must be given careful consideration
to ensure proper performance of each dryer. As a general
rule, an unrestricted air entrance from the outdoors of 250
inch
2
(1,612.9 cm
2
) is required. (Based on 1-inch
2
[6.5 cm
2
]
per 1,000 Btu [252 kcal].)
It is not necessary to have a separate make-up air opening
for each dryer. Common make-up air openings are acceptable.
However, they must be set up in such a manner that the make-
up air is distributed equally to all the dryers.
To compensate for the use of registers or louvers used over
the openings, this area must be increased by approximately
33%. Make-up air openings should not be located in an area
directly near where exhaust vents exit the building.
Allowances must be made for remote or constricting
passageways or where dryers are located at high altitudes or
predominantly low pressure areas.
NOTE:
Component failure due to dry cleaning solvent
fumes will void the warranty.
EXAMPLE: For a bank of four dryers, two unrestricted
openings measuring 22-3/8” by 22-3/8” (56.8 cm by 56.8 cm)
are acceptable. With louvers, two openings measuring 25.8”
x 25.8” (65.5 cm x 65.5 cm) are acceptable.
IMPORTANT:
Make-up air must be free of dry cleaning
solvent fumes. Make-up air that is contaminated by dry
cleaning solvent fumes will result in irreparable damage to
the motors and other dryer components.
A = 22-3/8” (56.8 cm)
B = 22-3/8” (56.8 cm)
Summary of Contents for AD120i
Page 30: ...ADC Part No 113546 2 08 13 14...