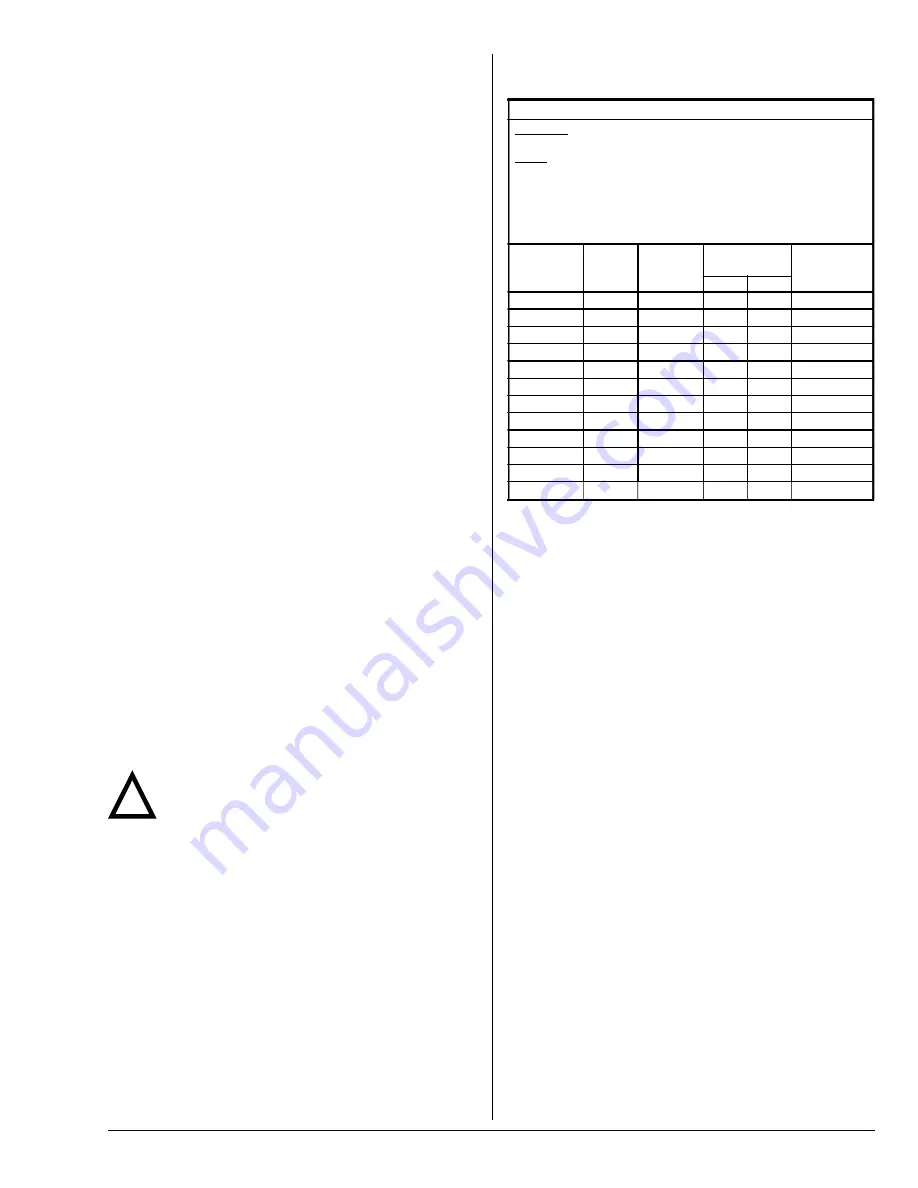
113546 - 2
www.adclaundry.com
15
!
Electrical Information _________________
Electrical Requirements
All electrical connections must be made by a properly licensed
and competent electrician. This is to ensure that the electrical
installation is adequate and conforms to local, state, and
national regulations or codes of the country of origin. In the
absence of such codes, all electrical connections, materials,
and workmanship must conform to the applicable requirements
of the National Electrical Code ANSI/NFPA NO. 70-LATEST
EDITION or in Canada, the Canadian Electrical Codes Parts
1 & 2 CSA C22.1-1990 or LATEST EDITION.
IMPORTANT:
Failure to comply with these codes or
ordinances, and/or the requirements stipulated in this
manual can result in personal injury or component failure.
NOTE:
Component failure due to improper installation will
void the warranty.
Each dryer should be connected to an independently protected
branch circuit. The dryer must be connected with copper wire
only. Do not use aluminum wire, which could cause a fire
hazard. The copper conductor wire/cable must be of proper
ampacity and insulation in accordance with electric codes for
making all service connections.
NOTE:
The use of aluminum wire will void the warranty.
An individual ground circuit must be provided to each dryer,
do not daisy chain.
Component failure due to improper voltage application will
void the warranty.
The manufacturer reserves the right to make changes in
specifications at any time without notice or obligation.
IMPORTANT:
A separate protected circuit must be provided
to each dryer.
The dryer must be connected to the electric supply shown
on the rating plate. In the case of 208 VAC or 240 VAC, the
supply voltage must match the electric service
specifications of the rating plate exactly.
The wire size must be properly sized to handle the related
current.
Warning
208 VAC and 240 VAC are not the same. Any
damage done to dryer components due to improper
voltage connections will automatically void the warranty.
Check your national and local code for breaker and wire size.
4/24/14
* Not available until September, 2014.
Grounding
A ground (earth) connection must be provided and installed
in accordance with local, state, and national regulations or
codes of the country of origin. In the absence of these codes,
grounding must conform to applicable requirements of the
National Electrical Code ANSI/NFPA NO. 70-LATEST
EDITION, or in Canada, the installation must conform to
applicable Canada Standards: Canadian Electrical Codes
Parts 1 & 2 CSA C22.1-1990 or LATEST EDITION. The ground
connection may be to a proven earth ground at the location
service panel.
For added personal safety, when possible, it is suggested that
a separate ground wire (size per local codes) be connected
from the ground connection of the dryer to a grounded cold
water pipe. Do not ground to a gas pipe or hot water pipe.
The grounded cold water pipe must have metal-to-metal
connection all the way to the electrical ground. If there are
any nonmetallic interruptions, such as, a meter, pump, plastic,
rubber, or other insulating connectors, they must be jumped
out with a wire (size per local codes) and securely clamped to
bare metal at both ends.
IMPORTANT:
For personal safety and proper operation, the
dryer must be grounded.
Provisions are made for ground connection in each dryer at
the electrical service connection area.
Electrical Service Specifications
Gas Models Only
ELECTRICAL SERVICE SPECIFICATIONS (PER POCKET)
IMPORTANT
:
NOTES
: A.
B.
C.
208 VAC AND 230/240 VAC ARE NOT THE SAME. When ordering,
specify exact voltage.
When fuses are used they must be dual element, time delay, current
limiting, class RK1 or RK5 ONLY. Calculate/determine correct fuse
value, by applying either local and/or National Electrical Codes to
listed appliance amp draw data.
Circuit breakers are thermal-magnetic (industrial) motor curve type
ONLY. For others, calculate/verify correct breaker size according to
appliance amp draw rating and type of breaker used.
Circuit breakers for 3-phase (3ø) dryers must be 3-pole type.
SERVICE
VOLTAGE
PHASE
WIRE
SERVICE
APPROX.
AMP DRAW
CIRCUIT
BREAKER
60 Hz
50 Hz
120
1ø
2
12.8
*
—
20
208
1ø
2
12.8
—
20
220
1ø
2
10
10
15
230
1ø
2
10
10
15
240
1ø
2
10
10
15
208
3ø
3
10
—
15
220
3ø
3
10
—
15
230
3ø
3
10
—
15
240
3ø
3
10
—
15
440
3ø
3
6.28
—
15
460
3ø
3
6.28
—
15
480
3ø
3
6.28
—
15
Summary of Contents for AD120i
Page 30: ...ADC Part No 113546 2 08 13 14...