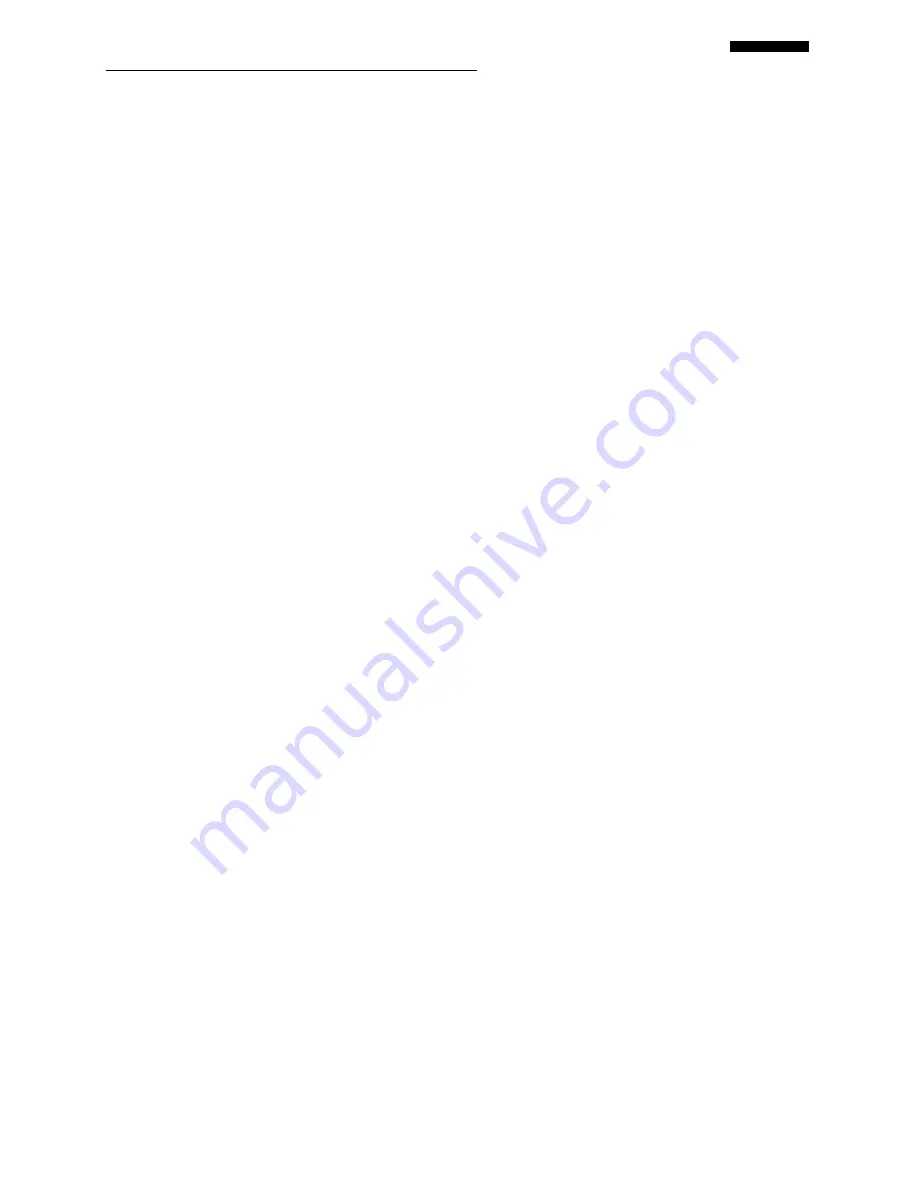
Gen II
User Manual
9-5 – Transient Balance
Chapter 9
Revision 2.10, Apr 2020
by noting the direction the fan rotates as viewed from behind the fan looking forward
out of the intake.
9.1.1.6.
Using the [
] key, move to the “
Num Baln Planes
” field. Use the [
] key to select
the total number of rotational balance planes on this engine type.
9.1.1.7.
Using the [
] key, move to the “
Num Optional Planes
” field. Use the [
] key to
select the total number of optional rotational balance planes on this engine type. An
optional plane is usually one which you may move to and continue balancing when
attempts to balance on the primary balance plane do not yield the desired results.
9.1.1.8.
Using the [
] key, move to the “
Balance Wt Type:
” field. The balance weight type
is a description of the balance weights for this application. Use the right arrow key to
select from Actual, Class, or Both. Class weights are balance weights designed
specifically for use with the engine. Class weights usually have a part number for the
set and a designation for each weight in the set. Weights are fixed values for each
individually designated weight. Actual means the weights are not designed
specifically for the engine, such as standard AN washers or slug weights. The
weights are designated as units of measure (grams or ounces) in the solution offered
by the analyzer rather than a specific class weight by name.
9.1.1.9.
If you selected “Class” or “Both” in the “Balance Wt Type:” field, the “
Num Class
Wt Sets
” field will be available. Using the [
] key, move to the “Num Class Wt Sets”
field. Use the [
] key to select the total number of class weight sets available for use
on this engine. If you choose a number here, be prepared to define each class weight
on a following screen.
9.1.1.10.
Use the [
] key to move to the “
Label Detail Wts:
” field. Detail weights are those
weights that are installed at the factory and cannot be removed. If these weights
occupy positions normally used for trim balancing, you may label those occupied
positions so that the balance solution will be calculated disregarding those locations.
In addition, if the engine has holes that are typically unusable for trim balancing, bolts
used to attach the spinner for example; this setting can define those holes as unusable
also. The choices here include “No”, “Job”, and “Setup”. With the selection set to
“Job” you have the opportunity to define these holes at the start of each job. This
selection is better suited for engines where the number of unusable holes changes on
each engine. If the detail weight holes are in fixed locations, you can define these
locations by selecting “Setup”. They would be saved in the setup and you would not
have to indicate them at the start of each job. Storing the detail weight locations in
the setup may also keep you from having to unnecessarily define the hole layout as
“Uneven” in paragraph 9.1.5.16 below.