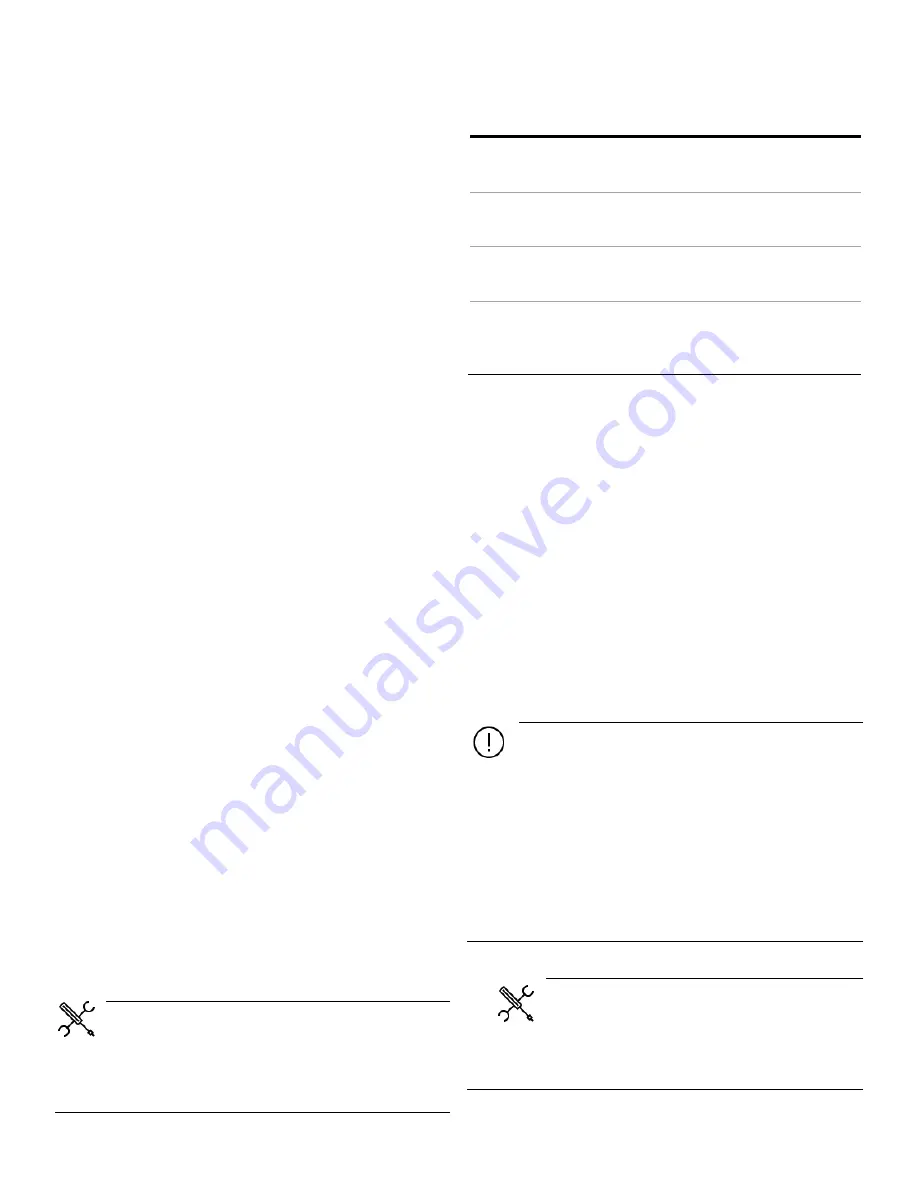
5 4
S P I R I T
I T
F L O W - X
I N S T R U C T I O N M A N U A L | I M / F L O W X - E N
12
I/O Diagnostics and calibration
This chapter describes the diagnostics and calibration features
for the digital and analog I/O.
I/O diagnostics
A Spirit
IT
Flow-X flow computer with a standard Spirit
IT
application provides a set of displays with diagnostic
information on the digital and analog I/O of the flow modules
that are part of the Spirit
IT
Flow-X flow computer.
To access the diagnostics displays:
On the LCD or web display select
Diagnostics, IO
from the
main menu.
Select the applicable flow module (only in case of a flow
computer with more than one flow module)
Select the type of I/O
I/O calibration
The analog inputs, PT100 inputs and analog outputs can be
calibrated at up to 5 calibration points.
Calibration points
For each type of I/O up to 5 calibration points can be defined.
For analog inputs and analog outputs the calibration points are
defined as percentage of span, while for PT100 inputs the
calibration points are defined in
ᵒ
C (metric applications) or
ᵒ
F
(metric applications). The number of calibration points may
range from 1 through 5.
The reference values should be in an ascending order, e.g. 0, 50,
100 %. Non-used reference values shall be set to 0. If a reference
value is smaller than or equal to the previous value, then this
point and any further points are not taken into account.
Typical calibration points for analog inputs and outputs are:
0, 0, 0, 0, 0
A single offset value is applied over the entire range
0, 100, 0, 0, 0
Calibration at 2 points, low and high range
0, 50, 100, 0, 0
Calibration at 3 points, low, mid and high range
0, 25, 50, 75, 100
Calibration at 5 points, low and high range and 3 mid ranges
Display → IO, Module <x>, Calibration, Settings
Display → Calibration, Module <x>, Settings
With x the applicable module number, i.e. the flow module to
which the signal is physically connected
Analog
input cal.
point 1..5
750
The calibration points for the calibration
of the 6 analog inputs
PT100
calibration
point 1..5
750
The calibration points for the calibration
of the 2 PT100 inputs
Analog
output cal.
point 1..5
750
The calibration points for the calibration
of the 4 analog outputs
Inactivity
timeout
limit
750
The input selected for calibration is
automatically reset in case of inactivity
longer than this limit. Enter 0 to disable
the automatic reset function.
If the calibration points are modified, the calibration of all
applicable inputs initially remains unaltered. At the start of the
next calibration of one of these inputs, any of the points that
have been altered, added or removed since the last calibration
are reset for this input only. E.g. when an analog input has been
calibrated at 5 points (reference values at 0, 25, 50, 75 and 100
%) and the number of calibrations has been redefined to 3
points (e.g. 0, 50, 100, 0, 0 %), then at the start of the next
calibration the 2nd and 3th calibration values will be reset to 50
and 100 % respectively and the 4th and 5th calibration values will
be reset to zero (= not used).
Analog input calibration
The procedure to calibrate an analog input is based on a loop
calibrator that, depending on the type of input, can provide a 4-
20 mA, 0-20 mA, 1-5 Vdc, or 0-5 Vdc signal.
During calibration the process input (e.g. pressure,
temperature) that uses the analog input will follow the
calibration value. So, before putting an input into calibration,
please be sure that one of the following conditions is met:
There’s no flow
The run has been set to maintenance mode
The process value has been set to override mode
The input has been frozen using the ‘Freeze all analog and
PT100 inputs’ command
1
Go to the analog input calibration display.
Display → IO, <Module x>, Calibration, Analog inputs
Display → Calibration, Module <x>, Analog inputs
With x the applicable module number, i.e. the flow module to
which the signal is physically connected.