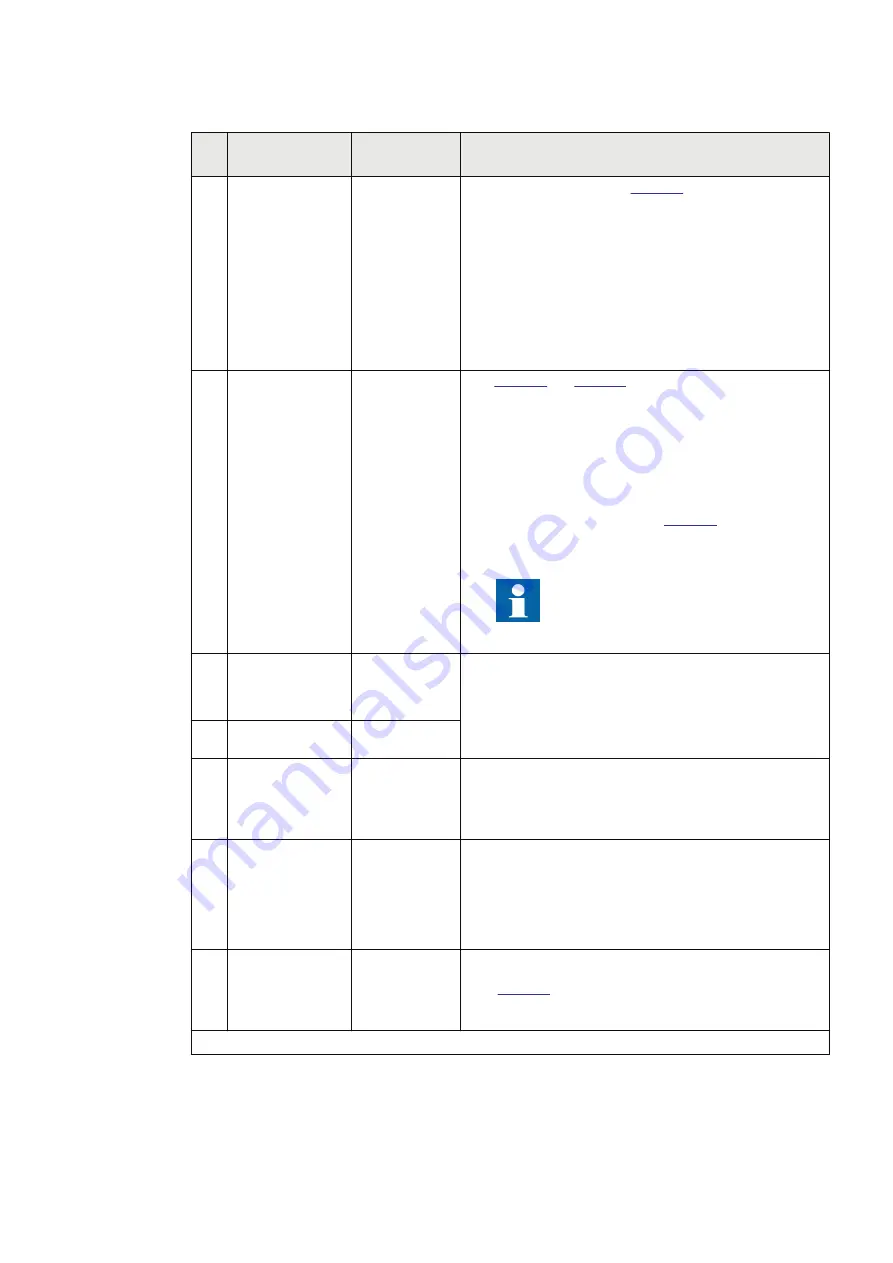
Table 10: GOOSE engineering process
Step REB500
configuration tool
HMI500
System
engineering tool
Remark
1
Pre-configuration:
•
REB500
System must
be
configured
•
System name
must be
defined
•
GOOSE client
must be
enabled
-
Enabling GOOSE Client (see
)
2
The REB500 IEC
61850-8-1 model is
exported in an ICD
file.
-
In addition to the ICD file that describes the IED functions, the
project-specific configuration file is also exported:
•
Edition 1: CID file (.cid)
•
Edition 2: IID file (.iid)
Selection of the Edition
Configuration/Communication/SCS Configuration/IEC
61850-8-1 options/Edition x (see
This Export SCS data process is used initially and after a
configuration change.
Each time the export is started, the original
values of REB500 setting parameters are
implemented.
3
The REB500 ICD
file is transferred
to the system
engineering tool
-
The IED name of the REB500 in the System engineering tool
must match the System name in the REB500 configuration
tool.
4
-
The REB500 ICD
file is imported
5
-
The data flow
engineering is
made in the
System
engineering tool
Setting instruction: For correct operation the GOOSE max
repetition time should be set to 1 second.
6
-
Export of the
Station
configuration
description
(SCD file) and
transfer to the
HMI500
Containing GOOSE data set, report control block, source IED
and destination IED
7
The available
GOOSE data
attributes are
imported (from
SCD file)
-
Configuration/Communication/SCS Configuration/IEC
61850-8-1 options/Import GOOSE data attributes button
(see
Table continues on next page
1MRK 500 132-UEN B
Section 4
HMI500
Distributed busbar protection REB500
43
Operation manual
© Copyright 2019 ABB. All rights reserved