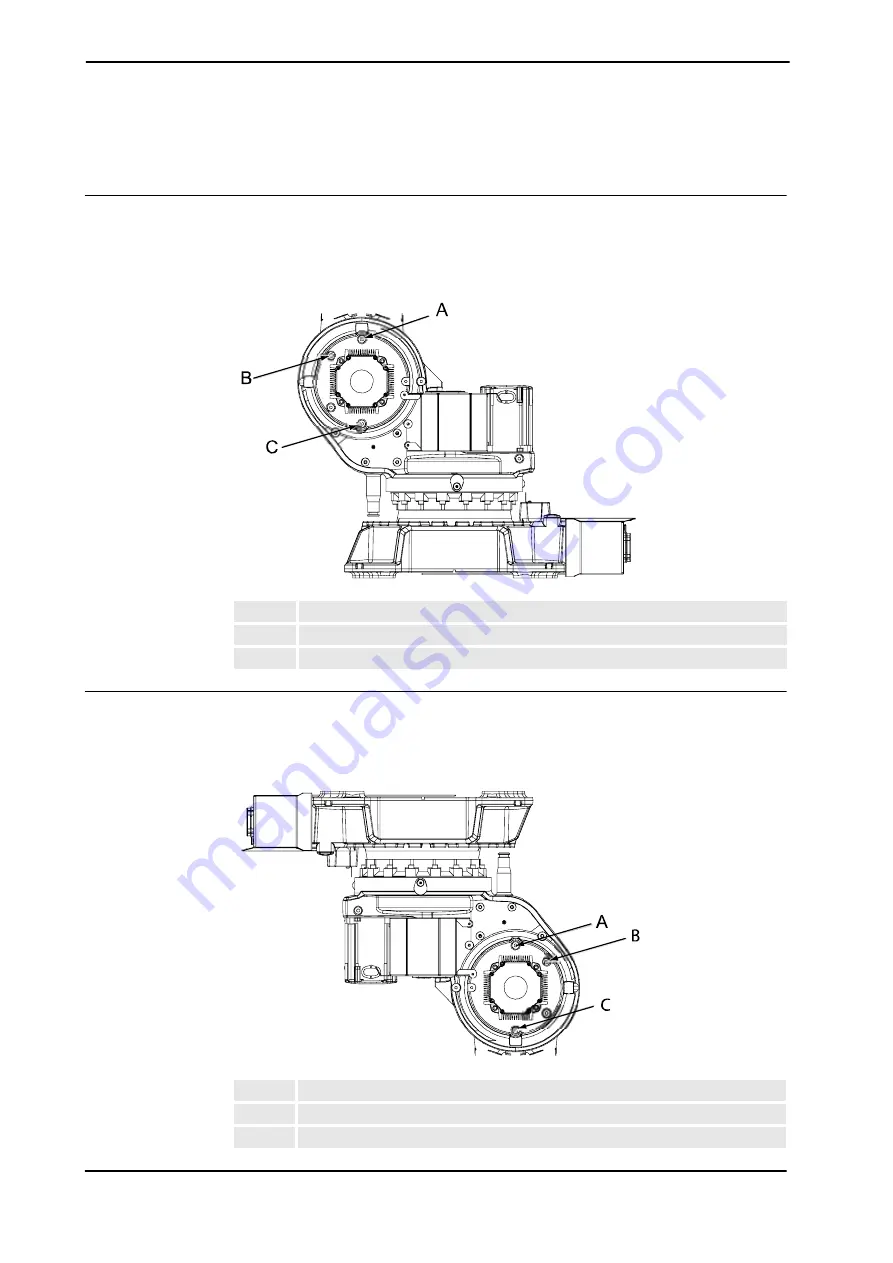
3 Maintenance
3.3.2. Inspection, oil level gearbox axis 2
3HAC027151-001 Revision: B
98
©
Co
py
rig
h
t 200
6-
200
8 ABB. All righ
ts reser
v
ed.
3.3.2. Inspection, oil level gearbox axis 2
Location of gearbox, floor mounted
The axis 2 gearbox is located in the lower arm rotational center, underneath the motor
attachment.
The figure below shows the robot floormounted.
xx0600002959
Location of gearbox, suspended
The figure below shows the robot mounted suspended.
The gearbox, axis 2, is located in the lower arm rotational center, underneath the motor
attachment.
xx0600002960
A
Oil plug, filling
B
Oil plug, inspection
C
Oil plug, draining
A
Oil plug, filling
B
Oil plug, inspection
C
Oil plug, draining
Continues on next page