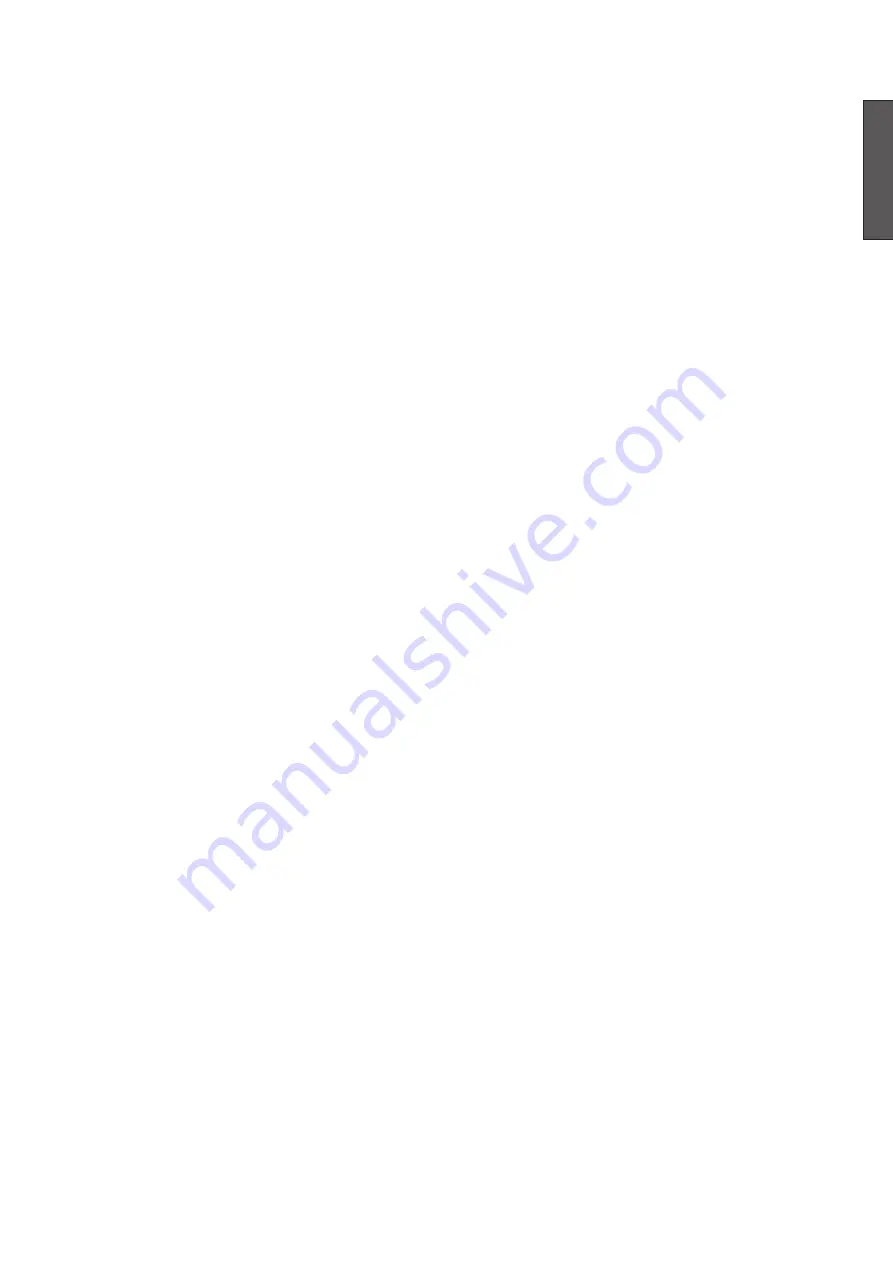
19
D C D r i v e s
19
D C D r i v e s
en
gl
is
h
Overview of the Installation and Commissioning Process
•
Wire analog inputs (e.g., speed reference) and outputs (e.g.,
meters for motor voltage, current) to terminal block XAI.
•
Wire high speed serial interface if needed. (Requires
optional fieldbus interface board.)
•
The DCS880 allows you to choose the usage of each digital
and analog input and output. The converter has factory
default settings which can be changed by loading a macro,
but some designations are universal. They include:
- Digital input DIL: Off2 (fast current off)
- Digital input DI1: On/Off (maintained) or On-Start
(pulsed)
- Digital input DI2: Start/Stop (maintained) or Off-Stop
(pulsed)
- Digital input DI3: Fault reset
-
XR01: DC contactor US
-
XSMC: Main Contactor (AC),
On (3 Amps max. at 115 – 230 Vac)
•
Other signals may be required depending on your
application (e.g., motor fan acknowledge input, Off2 input,
fan-on output, brake output).
•
You will select the macro and / or choose the configuration
for digital and analog inputs and outputs in step 2 of the
commissioning process, or by updating group 20
parameters.
•
Check all wire terminations (with continuity tester) before
proceeding to the next step.
Step 4:
Connect the drive system to incoming power and the motor
to the converter (both field and armature) as well as
accessory equipment (motor fan, thermal switch, brake, etc.).
•
See hardware manual for typical cable size and tightening
torque recommendations.
•
IMPORTANT: Be sure all safety equipment is properly sized
for your application
Step 5:
Apply control power to the converter.
•
IMPORTANT: See section “Safety and Operating
Instructions” in this manual before proceeding.
• Apply power to terminal block 99 and X2. The keypad
should light up and show the menu screen. The converter
fans should start to run (if converter has fans).
Step 6:
Commission the converter using Drive Composer Pro
(preferred) or the control panel.
•
IMPORTANT: See safety alerts and general instructions in
the section “Commissioning” before proceeding.
•
Connect DCS880 PC tools of your computer to DCS880.
•
If no PC is available, commission your drive using the
control panel as follows:
- On the control panel, press the softkey to select MENU.
- Using the down arrow, select ASSISTANTS. Then press
SELECT.
- Starting with “BASIC SETUP” for date and time, press
SELECT.
- Second step „DCS880 SETUP“ for name plate data and
autotunings, press SELECT.
Step 1:
Check converter for damage. Contact ABB Technical Support
if damage is found. In North America, call
1-800-435-7365 (1-800-HELP-365)
Step 2:
Select supporting hardware for the converter:
For specific recommendations for fuses, reactors, and
contactors, see the DCS880 hardware manual or technical
catalog.
Circuit breaker or disconnect:
Current rating = Idc * 0.816 * 1.25 (min)
= Idc * 0.816 * 2.50 (max)
Where: Idc = nominal DC motor current
Fuses:
AC Line Fuses: To properly protect the converter, semi-
conductor fuses on the incoming AC power line are required
in all cases.
DC Output Fuses:
Fuses between the motor and the
converter are required for all regenerative (4-Q) converters.
This is to protect the motor and converter if a commutation
fault should occur. NOTE: DC output fuses are the same type
and size as AC line fuses.
Line reactor:
All thyristor-based dc converters cause notching in the AC
line due to motor commutation. A properly sized line reactor
will mitigate the effect on the line. Unless the converter uses
a dedicated isolation transformer, each converter requires
its own line reactor.
AC or DC contactor:
A contactor is required to safely disconnect the motor from
the incoming power when the converter is off. The contactor
can be installed between the line and the converter (an AC
contactor) or between the converter and the motor (a DC
contactor). Do not use both.
IMPORTANT:
Other equipment may be necessary depending
on application and local codes.
Step 3:
Mount and wire the converter and supporting hardware
inside an industrial enclosure with adequate cooling
(DCS880 modules have rating of NEMA type OPEN).
The following control and signal wiring is required:
•
If using an AC contactor, we recommend wiring an
auxiliary contact to the digital input you have designated
as 20.34 Mains contactor acknowledge source or 20.06
Run/Stop source.
•
If using a DC contactor, you must wire an auxiliary contact
from the contactor to the digital input you have
designated as 20.34 Mains contactor acknowledge source.
•
Wire 115 or 230 Vac 1-phase power to terminal block 99 for
converter control power.
•
Wire 1-phase power to converter for cooling fans. See table
and wiring diagrams in this manual.
- H1 ... H3 frames: Fan internal supplied.
-
H4 frame: use 230 Vac. Fan terminal X2 is on top of the
converter.
• Wire tachometer or encoder to terminal block XTAC (tacho)
or XENC (encoder).