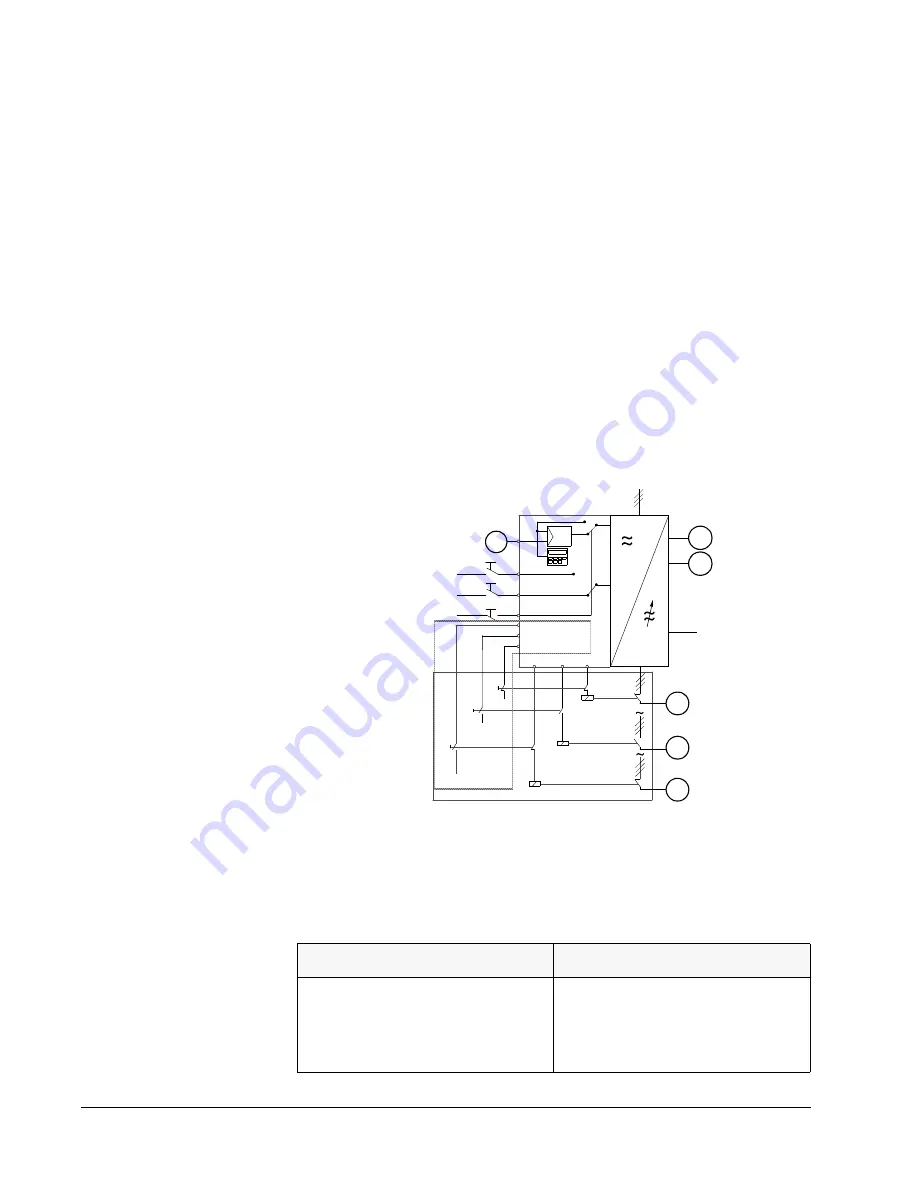
Chapter 5 – Standard Application Macro Programs
5-12
ACH 500 Programming Manual
Application 4 –
Pump and Fan
The main application areas of Pump and Fan Control (PFC) are pumping and
ventilation systems where speed regulation of a drive motor and automatic
start/stop of a maximum of three constant speed motors are beneficial. PFC
can easily be connected to a custom made automatic motor alternation system
for controlled changing of drive motors. In this way, all the motors run equal
duty times. This Application macro allows you to choose between manual and
automatic control. A reference (setpoint) value can be given either internally
through a LCD panel or externally through screw terminals. A maximum of
two actual values can be connected through the screw terminals. Actual
values can perform different mathematical operations (addition, subtraction,
multiplication, minimum, maximum, and square root) to get a correct final
actual value for the PI-controller.
The PI-controller can also be bypassed and actual value used as the speed
reference.
Operation Diagram
Figure 5-7 Operation Diagram
Input and Output
Signals
Table 5-5 Input and Output Signals
Input Signals
Output Signals
Actual value 4 – 20 mA
Analog Output AO1: Output Frequency
Analog Output AO2: Motor Current
Relay Output RO1: First Motor Control
Relay Output RO2: Second Motor Control
Relay Output RO3: FAULT
f
A
M
3
∼
Motor
Relay Output
Motor 1
Input
R03*
FAULT
Current
Output
Frequency
PIþ
Aþ
Bþ
PT
START/STOP/Aþ
START/STOP/Bþ
A/B Select
(Manual/Auto)þ
DI 4 (Interlock 3)
*þ
DI 3 (Interlock 2)þ
DI 2 (Interlock 1)
þ
RO3*
RO2
RO1
M
3
∼
Motor 2
M
3
∼
Motor 3
Regulated
Speed
Constant
Speed
Constant
Speed
1 ON/OFF
2 ON/
OFF
3ON/
OFF
* DI4 and RO3 are reserved for motor 3 control if two
lag motors are select with the parameter 40.2.17
Ref.þ
ACT1þ
Power
If interlock function is used.