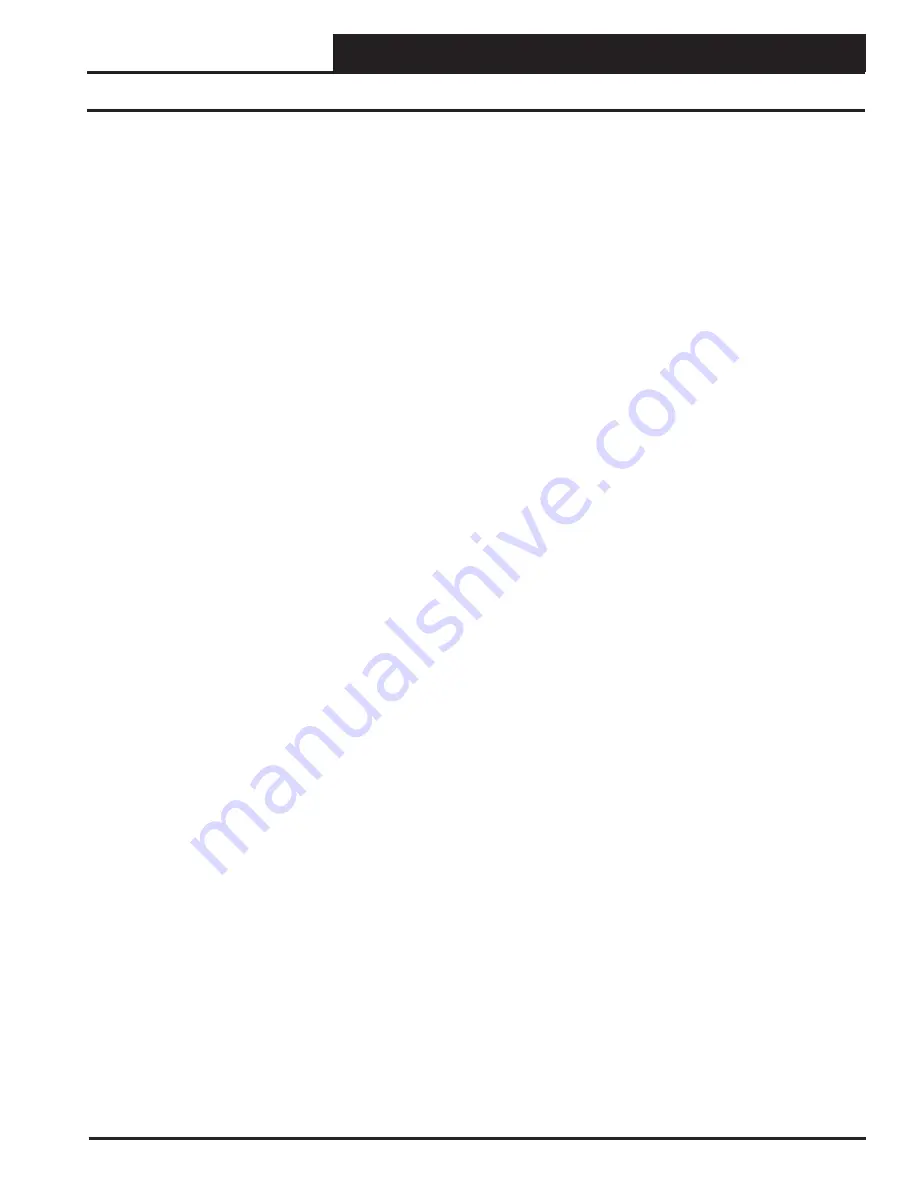
Main Chiller Controller Technical Guide
SECTION 2: SEQUENCE OF OPERATIONS
19
• No Turbocor
®
Faults are active for the designated
compressor activating.
• If this is not the fi rst compressor to start,
Wait at least 10 minutes for the Condenser Ratio to
be 2.4 (adjustable) or lower.
After 10 minutes, ignore the ratio if it hasn’t dropped
low enough and start anyway.
2. Select next compressor to start based on whether lead/
lag or sequential operation is selected:
• Lead/lag operation: Based on current accumulated
run-times for all available compressors, select the
available compressor with the lowest run-time.
• Sequential operation: Select the next available
compressor in the straight sequence 1, 2, 3.
3. Establish the demand for all compressors based on
the number of currently running compressors:
• No compressors currently running: Demand = Start
demand
• One compressor currently running: Demand = 2
Compressor start demand
• Two compressors currently running: Demand = 3
Compressor start demand
4. Set the desired demand for all running compressors
and for the new compressor to be started (this will
start the new compressor).
5. Wait for indication the new compressor is fully
activated and begin/continue modulation.
Stage Down
1. During Stage Down, the controller will verify the
following conditions:
• Leaving Water Temperature is lower than the Leaving
Water Temperature Setpoint – Cooling Stage Window.
• At least one compressor is active and all running
compressors are at stage up/down minimums based
on the number of running compressors.
• All running compressors have completed their
startup cycle.
• Stage Down and Minimum Run timers met.
2. Select the compressor to shut down based on whether lead/
lag or sequential operation is selected:
• Lead/lag operation: Based on current accumulated
run-times for all running compressors, select the
compressor with the longest run-time and signal
it to shutdown (do not wait for the shutdown to
complete at this point).
• Sequential operation: Select the numerically highest
running compressor in the straight sequence 1, 2,
3 and signal that compressor to shutdown (do not
wait for the shutdown to complete at this point).
3. If there are additional compressors still running:
• Since the stage down demand has been set for the
number of running compressors, it will resume
modulating from this level when operations allow
it to continue.
• Wait for indication the compressor being shut
down is fully deactivated and continue
modulation from the current stage down level.
4. If no compressors are running, return to startup and wait
for demand or shutdown.
Modulation
1. Modulation demand is based on the Leaving Water
Temperature and a resettable setpoint.
2. The current setpoint is determined based on the reset
input and the reset high and reset low settable set
points.
3. All running compressors modulate together.
4. A PID loop is used to calculate a demand factor to
apply to the compressors. This demand factor
should be sent to all running Compressor Circuit
Modules to drive compressor operation.
Shutdown
1. Verify conditions for shutdown:
(1) Emergency stop was activated.
(2) A phase brown-out condition occurred.
(3) A Refrigerant Leak has been detected.
(4) Remote start/stop was deactivated.
(5) No outstanding run command from WattComms
or BACnet
®
.
Main Chiller Controller Operation