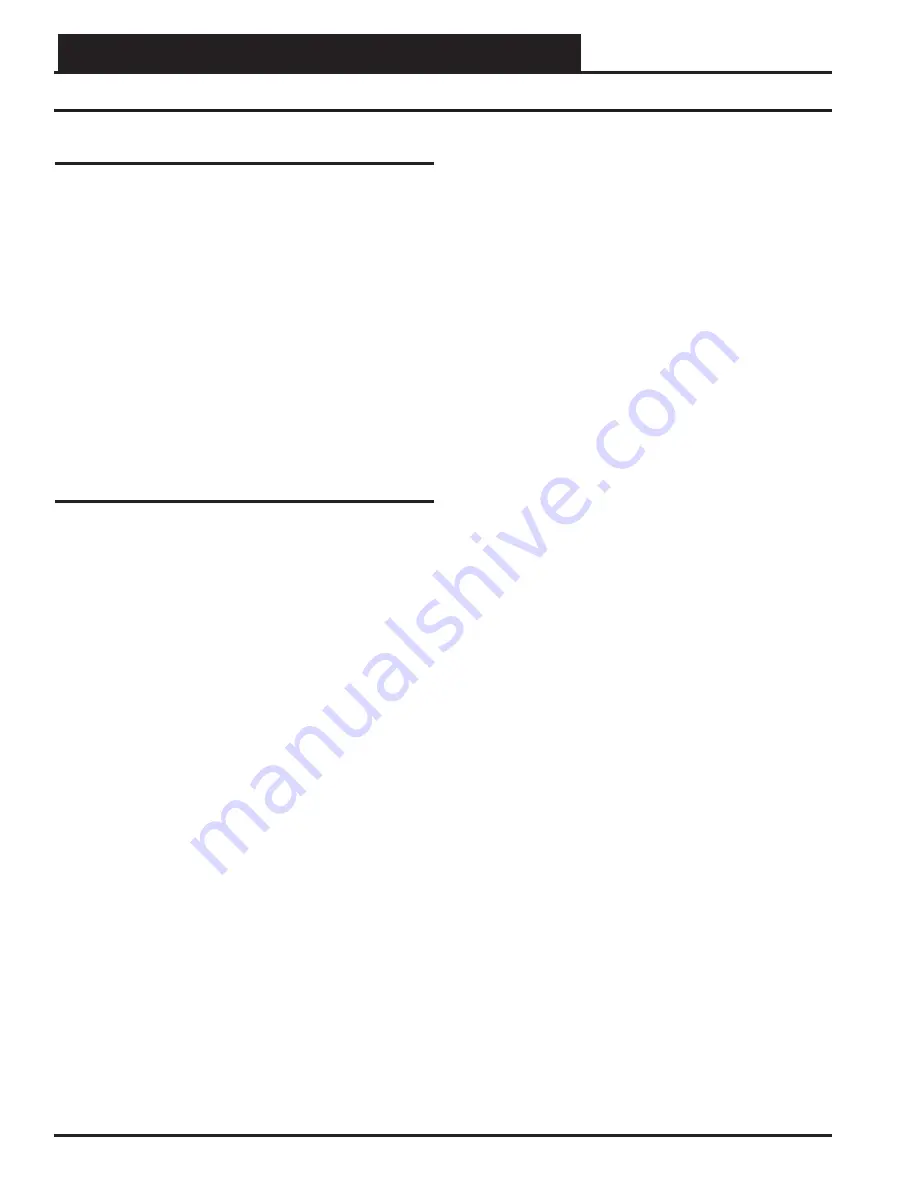
Zone
Zone
SECTION 2: SEQUENCE OF OPERATIONS
Main Chiller Controller Technical Guide
18
Main Chiller Controller Operation
Main Chiller Controller Operation
The chiller system consists of two primary systems:
1. Refrigeration Loop Control
1.1. Compressor control (executed by Compressor
Circuit Module)
1.2. Condenser control (by Main Chiller Controller)
1.3. Expansion/tank level control (by Main Chiller
Controller)
1.4. Economizer/sub-cooling control (executed by
Economizer/sub-cooling Module)
2. Vestibule Fan-Coil Control (by Main Chiller
Controller)
Refrigeration Loop Control
The Main Chiller Controller Refrigeration Loop Control sequence
consists of (5) primary control sections and safeties:
1. Compressor Control
1.1 Lead/Lag Control
2. Condenser Control
3. Expansion Valve Control
4. Economizer/Sub-cooling Control
5. Safeties Management (interspersed throughout)
Compressor Control
Compressor control is managed based on demands and utilizes the
Compressor Circuit Modules.
Run-time Accumulation
The Main Chiller Controller should maintain a total accumulated
run-time for each compressor to be used in Lead/Lag
management. These run-times should be individually clearable
in the event a compressor is replaced.
Lead/Lag Operation
Lead/Lag operation is embedded within the staging so that lead/
lag operation can be managed within a system that never (or
rarely) shuts down. The lead/lag philosophy is simple:
•
When staging up, the compressor with the least run
time stages up fi rst.
•
When staging down, the compressor with the most
run-time stages down fi rst.
•
There are no provisions for enforcing a running
compressor changeover to manage lead/lag.
Startup
1. The Controller will wait for one of (4) run
commands:
1.1 Remote Start/Stop activation Wet Contact
on Binary Input #1 of the Main Controller
1.2 Remote Start/Stop activation 5.0 VDC input
on Chiller Expansion Module Input #3
1.3 Command via WattComms
1.4 Command via BACnet
®
The WattComms and BACnet
®
commands should
aff ect the same internal variable such that an acti-
vation through either one will be seen as an acti-
vation by the other, and in turn, either command
can deactivate, regardless of which initiated the
activation. The Remote Start/Stop overrides the
WattComms or BACnet
®
commands if enabled
and its control cannot be defeated by an activation
or deactivation command from either.
2. The Controller will then open the butterfl y valve
over a period of 5 minutes and wait for the valve
to completely open before moving on.
3. The Controller will then wait for Proof of Water
Flow. (
NOTE:
This is an overlap to the water fl ow
safety in that compressors cannot be run without
water fl ow).
Staging
Staging should be based on demands above or below the current
modulation capacity of the running compressors. Staging
specifi cs should refer to the Turbocor
®
compressor manual for
setting and managing demand settings and timings during the
stage action.
Stage Up
1. During Stage Up, the controller will verify the following
conditions:
• The Leaving Water Temperature is higher than the
Leaving Water Temperature Setpoint.
• No compressors are active or all running compressors
are at maximum position.
• There is an enabled compressor available to activate.
• All running compressors have completed their startup
cycle.
• Stage Up and Minimum Off timers met.
• No safeties are active which would stop compressor
operation.